We know that even a properly-designed joint can turn out imperfectly if correct brazing is not followed. Successful vacuum brazing relies on proper technique as well as the correct materials and furnace capability to continuously control the brazing cycle.
In this article I’m going to discuss the basic steps required in correct brazing procedures. And I’m going into a fair amount of detail in order to be as informative as possible. To fully understand how to achieve a perfect brazing, I’m going to explain how exactly the vacuum brazing process works, the benefits of brazing in a vacuum furnace, and the key features of vacuum brazing furnaces.
How vacuum brazing works
Brazing is a method of joining two or more metals by melting a filler metal, or the brazing alloy.
When alloys are used instead of a pure metal for the process in a vacuum furnace, they do not contain fluxes, there is therefore no need to remove the slag by mechanical methods and the weld appears clean. The alloy must not include elements that can sublimate or evaporate, since the desired joint characteristics will not be achieved and the furnace could be contaminated.
In general alloys do not fuse together at a well-defined temperature as do pure metals, but within a range. When possible therefore eutectic alloys should be sought. These have a similar behavior to pure metals, where the solid and liquid elements co-exist only at the eutectic temperature.
There are a significant number of filler metalsfor vacuum brazing available. In some alloys, generally with high temperature uses, there are still in many cases a situation of a “solidus” and “liquidus” phase being present at a single temperature, made up of more than two forms of metal. Other alloys, commonly used in vacuum furnaces, nevertheless show a broad intermediate “solidus-liquidus” phase with a temperature rise between the two important phases. In this case the time for a complete fusion increases as this takes place at a higher temperature, which will be the brazing process temperature.
Why brazing in a vacuum furnace
The vacuum furnace can ensure reaching the melting temperature with extreme precision and without over-shoot. Also note that the problems of resistance to oxidation and corrosion of the alloy itself become negligible in the vacuum furnace.
For the brazing to be successful the filler must melt (whether in the form of a paste or as a metallic wire or tape) at its own specific melting temperature and not at a higher temperature. This primarily avoids the liquid being at a temperature at which its surface tension would be lower, and therefore wetting a greater surface area, with the resulting joint lacking the correct filling. The liquid must spread precisely within the joint cavity between the metals, creating an intermediate layer.
Capillary action ensures the alloy penetrates into the joint spaces in its liquid state. These are created by mechanical processing, exactly where the joint is required. Mechanical processing is required to obtain the right tolerances in the elements of the joint and must determine the exact bed dimension for the bond. The gap must be created so as to avoid too restrictive tolerances, in which case the bond could be difficult to fill and, at the other end of the spectrum, a weak joint would result from too great a tolerance, potentially with gaps or porosity. In fact, the alloy is drawn inside the surfaces to be joined at the wettability temperature, against the force of gravity.
An alloy is required with a melting temperature far from the melting temperature of the metals being joined, but at the same time with suitable mechanical characteristics for the joint. Moreover, in order to achieve perfect brazed joints, the joint surface must be clean, without traces of processing oils or greases, in order to have good wettability.
Brazing is simple and easy in a vacuum furnace. Due to the nature of the vacuum, heat is evenly distributed and part production is consistent. But let’s see more in detail the specific features of a vacuum furnace for brazing.
Did you like this article up to here?
Before you continue, follow us on our Twitter page pressing the button here below!
In this way, we'll be able to keep you updated on most advanced technologies for heat treatments not only with our posts, but also with the best articles that we collect around the web.
Vacuum brazing furnace: the key features
The vacuum furnace, given its high uniformity within the hot zone of the entire temperature curve, is the ideal system to carry out an identical heating cycle on a high number of loads as well as continuous brazing on larger pieces. It is furthermore capable of repeating the same cycle accurately. The work pieces can be recognized as they are loaded via a bar code linked to the cycle programme. Each piece can thus be associated with its own heating cycle.
The vacuum furnace operating at the melting temperature of the filler is generally a higher temperature than the temperature at which oxides form. As a result even oxidized pieces lose the oxide layer in the vacuum, before reaching the filler melting temperature.
The vacuum furnace must be cleaned. This means leaving no contaminants on the load.
The vacuum furnace for applications in aerospace, particle physics and metallurgical research in general, is a complex and sophisticated system, manufactured with a metallic thermal chamber, dry pumping and the vessel construction criteria characteristic of an ultra-high vacuum furnace. The furnace conforms to the NADCAP requirements, while the cycle programming software allows automatic cycles with great precision.
- The metal chamber, containing the hot zone, is manufactured with multiple layers of metal reflecting shielding in molybdenum/lanthanum for the internal shields, the intermediate ones in molybdenum and in SS for the external shields. The level of cleaning in the vacuum environment required by the specification is obtained by avoiding the use of panels of insulating materials in the construction of the thermal chamber, such as aluminium fibre or graphite sponge, materials capable of retaining humidity or worse oil vapors.
- The vacuum seal vessel, created entirely in stainless steel, is ultrasonically cleaned internally before assembly and subsequently subjected to a seal test with a helium leak detector. The components are entirely ultra-high vacuum, metallic seals or Viton.
- The pumping system does not provide for the use of lubricated pumps, but a dry primary pump instead. The roots pump (lobe booster pump) is a typical pump in which the seal is entrusted to the tolerances between the lobes and stator. The ultra-high vacuum pump can be turbomolecular or a cryogenic pump. However, oil vapor diffusion pumps can also be used, if a cryogenic trap with supplied liquid nitrogen or a double stage Polycold system is fitted. Both these systems are capable of drawing condensable vapors and impeding the backscatter of oil vapors.
As we have seen, vacuum furnace brazing is simple and easy. You can obtain perfect brazed joints and no secondary fabrication or finishing is required. Do you want more details to solve your braze problems? Just ask and I’ll be happy to provide you with more information for a perfect brazing.
Did you like the article?
Subscribe to our Telegram channel and stay up to date on most advanced technologies for heat treatments.
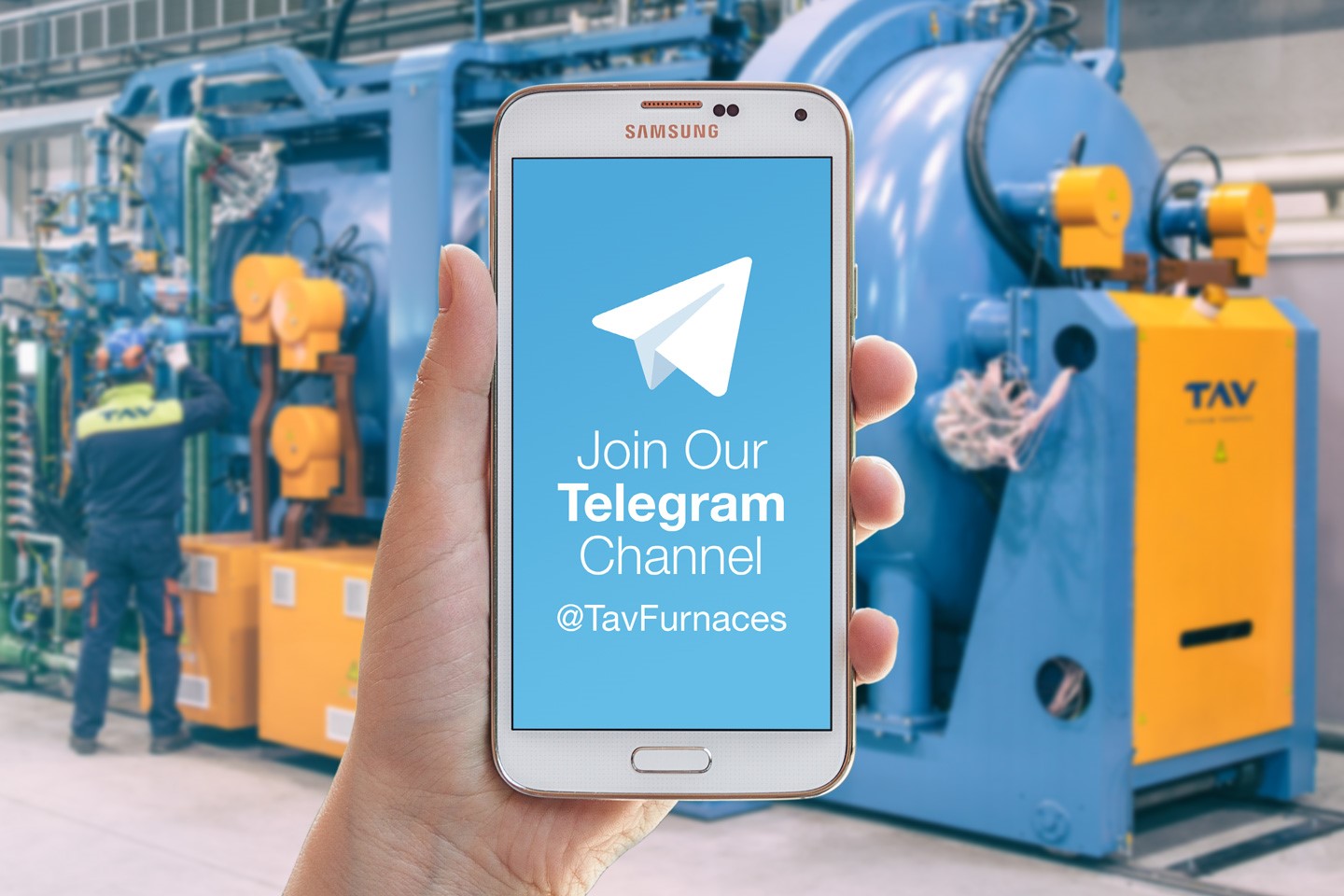
Don't you have Telegram?
If you do not have Telegram yet, use one of the following buttons to install it:
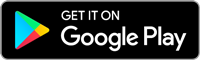
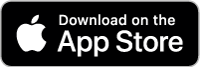