This post is dedicated to the most influential PM event in Europe: Euro PM2017 Congress & Exhibition, held on 1-5 October, in Milan (Italy). The Powder Metallurgy (PM) sector is constantly undergoing technological development, and at TAV VACUUM FURNACES’s stand the innovations this produces could be experienced at first hand. Visitors' attention was caught especially by the vacuum system we exhibited inside the hall. Our furnace attracted a great deal of interest from the public, and potential users were very impressed with the equipment we offer. Many discovered new solutions to meet their specific needs.
In this post you will find answers to technical questions and simple curiosities from visitors to TAV VACUUM FURNACES’s stand, where our vacuum furnace welcomed thousands of curious yet competent visitors.
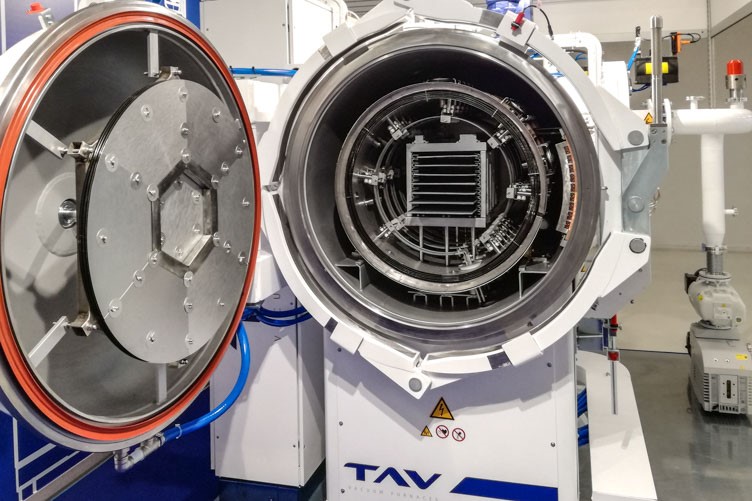
But, before addressing its main technical features, it is important to have a common understanding of what PM is...
What is Powder Metallurgy (PM)?
It is a versatile, cost-effective, and constantly expanding technology that is rapidly gaining worldwide popularity. Powder Metallurgy (PM) is a manufacturing process where various powder metals or alloys are compressed and then sintered (heated) to metallurgically bond the particles. Material blending can be used to create an end product with specific properties for a particular application or industry.
Over the past few decades, PM has become widely recognized as a superior way of producing high-quality parts for a variety of applications. This success is due to the advantages the process offers over other metal forming technologies such as die casting. As compared to the existing procedures, powder metallurgy offers significant advantages in material utilization, shape complexity, near-net-shape dimensional control, among others.
Today, Powder Metallurgy comprises several different technologies for fabricating semi-dense and fully dense components. They are:
- conventional Powder Metallurgy (PM), referred to as press-and-sinter;
- Metal Injection Moulding (MIM);
- Hot Isostatic Pressing (HIP);
- Additive Manufacturing (AM), also known as 3D printing.
Why choose Powder Metallurgy?
Conventional PM offers many advantages over the other consolidation methods. Created by mixing elemental or alloy powders and compacting the mixture in a die, the resultant shapes are then sintered in a controlled atmosphere furnace to bond the particles metallurgically. The powder metallurgy process yields net-shape, or near-net-shape parts, so that little or no machining is required to obtain a finished part in many cases. In order to eliminate machining operations, PM relies on its abilities to form complex geometrical shapes directly and to hold close dimensional tolerance control in the sintered product.
Complex geometries requiring irregular curves, eccentrics, radial projections, or recesses often can be produced only by powder processing. Hard metal components that require irregular holes, keyways, flat sides, or square holes that are difficult to machine can be readily made by PM.
Users often choose PM for manufacturing gears because it allows for a certain amount of customization of material properties to produce desired characteristics suitable for a particular application. Advantages of powder metallurgy include:
- High complexity shape capability
- Less material waste
- Controlled porosity
- Repeatability
- Excellent mechanical properties
- Tailored solutions using unique materials
- Great precision and good surface finish.
Is the PM process suitable for you?
Wherever there is a need for the highest possible lifecycle performance in conditions of extreme heat, wear and corrosion, PM technology can be a cost-saving design option. Powder metallurgy components are proven to have outstanding wear resistance and mechanical properties and provide exceptional reliability needed for anything from aerospace bearings to industrial saw teeth.
PM is especially suited to the production of large series of pieces with narrow tolerances and can be used to produce both simple and more complex parts. Powder Metallurgy can help you reach your cost reduction goals without sacrificing quality and strength. Intricate sintered metal casting parts can be cast and then machined, but powdered metal parts can often be produced at a fraction of the cost generating substantial cost savings of up to 90%.
The net-shape capability of powder metallurgy is the primary advantage in the process, but there is also no waste in the shaping of parts. Your company’s sustainability targets can be met by making PM a critical part of your fabrication process.
Once you have thought about that, you could start to challenge the market by having a competitive strength in the production of high quality products. But for the sake of this example, let’s see where Powder Metallurgy applies, turning finally to TAV’s vacuum furnace that gained considerable interest at Euro PM2017.
Did you like this article up to here?
Before you continue, follow us on our Twitter page pressing the button here below!
In this way, we'll be able to keep you updated on most advanced technologies for heat treatments not only with our posts, but also with the best articles that we collect around the web.
What are the applications of PM technology?
PM provides cost-effective complex parts for a variety of applications. Since it is a net-shape processing technology, PM yields parts requiring little or no secondary machining operations. The powder metallurgy process is well-suited to producing high-strength gears for the automotive industry.
Captive applications of PM include materials that are difficult to process by other techniques, such as refractory metals (e.g. tungsten, molybdenum and tantalum) and reactive metals (e.g. titanium). Some super alloy and material combinations can only be achieved by powder processing.
Today's advanced materials are seldom made of metals and metallic alloys alone. They often incorporate ceramics and composite materials. These include:
- cermets;
- nanostructured materials;
- alumina composites WIDIA (metal matrix + WC and TiC);
- polycrystalline diamond (PCD);
- polycrystalline cubic boron nitride (PCBN);
- partially stabilized zirconia (PSZ).
PM makes available to designers a wide variety of material systems from which to choose.
The technology of utilizing metal powders offers the engineer a means of conserving materials, reducing machining and securing a uniform product at a reasonable cost. This unique metal-forming method allows the production of parts with close tolerances and a minimum of scrap. It is used to manufacture products such as filters, bearings and gears, cutting tools and dies, medical implants, heat shields, magnets and fuel cells. Industries benefitting from PM technology include:
- Automotive
- Aviation and Aerospace
- Machining
- Medical technology
- Electronics.
TAV’s vacuum sintering furnace for PM
After having illustrated several reasons that determine the quality of Powder Metallurgy, here we are at TAV’s vacuum furnace, which was showcased at Euro PM2017 and attracted significant interest from visitors.
We displayed a sintering furnace with the following technical features:
- Dimensions: 300 mm x 300 mm x 450 mm (w x h x d)
- Max. load weight capacity: 100 kg
- Hot zone: circular all-metal
- Max. operating temperature: 1450 °C
- Availability of High Vacuum (HV) system (not displayed for obvious need of space).
Thanks to a MIM Box and appropriate gas streams, the system enables users to perform vacuum debinding and sintering in one process cycle, without contamination of the components or hot zone. Vacuum debinding and sintering in one process cycle offers economic benefits in terms of cost and lead time reduction.
If you would like to find out more about debinding and sintering in the same furnace, have a look at perfect vacuum sintering.
The metallic hot zone offers energy efficiency and flexibility, as well as the clean environment required by many industrial sectors addressing contamination-sensitive challenges. It is therefore suitable for the manufacture of sintered components used in medical, aerospace and industrial applications.
If you want to increase knowledge of metal hot zones, read vacuum furnace hot zone: graphite vs metal.
Of course, the equipment was intended for a standard PM product. In addition to the vacuum system described, TAV VACUUM FURNACES provides long-term technical solutions suitable for most of the applications related to Euro PM. Our great flexibility lies not only in the range of vacuum furnaces and their performance but also in each individual furnace, which can be equipped and customized to suit unique applications.
Need more info?
To discuss your vacuum furnace requirements, feel free to contact us using the form here below.