Before we examine just how useful vacuum brazing furnaces can be for car, truck
and motorcycle manufacturers, it is probably best to define exactly what this process
is for those who are not yet experts in this particular field.
Essentially,
brazing makes two metals bond with one another by applying a metallic filler. For
a good join to be made, this filler must possess a lower melting point than the
temperature than either of the two metals that are being joined would liquefy at.
When the filler is melted it must make physical contact with either side of the
join, forming a solid bond once it solidifies.
Obtaining a Strong Joint
In most cases, this is achieved by vehicle manufacturers by using the right sort
of filler metal for the particular join. In fact, there are plenty of options to
choose between - the filler could come in the form of a wire, a thin plate or even
a paste, for instance. It simply depends on the sort of application that the process
is being conducted for.
Of course, in order to achieve a high-quality bond - both for physical properties
of stress resistance and the ability to withstand corrosion - it is preferable
to have a highly controlled environment. This is because grime and even
airborne particles could contaminate the brazing process, something that the leading
players in the automotive sector wish to avoid at all costs.
This is where vacuum brazing comes in which is what we will discuss next.
Later, you will also discover how the leading vacuum brazing furnace technologies
work to ensure that the stringent quality control measures required of all metal
joins in the automotive sector are maintained.
Automotive Heat Treatments and Vacuum Furnace Technology
For an effective brazing heat treatment, the cleanest level of atmosphere should
be obtained which, for a highly precise engineering sector like the automotive industry,
really means generating a vacuum.
Because a vacuum furnace can minimise
the contamination of any impurities in the local environment to virtually zero,
the joined metal will be high mechanically resistant and long-lasting. This is especially
important for car makers where complicated parts must be connected to one another,
often with non-standard shapes.
Given that the automotive sector also relies on many joining points in a relatively
small space, vacuum furnace brazing also makes a great deal of sense. As such, the
industry will often use this heat treatments for applications such as water heat
exchangers joints. In the automotive sector, the use of aluminium as a principle
element for top-notch heat exchangers is becoming ever more popular.
Both
AA 3xxx and 4xxx aluminium alloys are commonly used materials in
the sector, for example. The main reason why these particular alloys are so useful
is that they afford a very low specific weight whilst still offering a high level
of thermal conductivity.
As outlined above, one of the cleanest environments for precision brazing
applications in the automotive sector is a vacuum. Therefore, readers with
an interest in automotive heat treatments and aluminium alloys, in particular, should
read on for a more in-depth analysis of the individual properties of semi-automatic
vacuum brazing furnaces which makes them so suited to the common applications
required of the automotive industry.
Did you like this article up to here?
Before you continue, follow us on our LinkedIn page pressing the button here below!
In this way, we'll be able to keep you updated on most advanced technologies for heat treatments not only with our posts, but also with the best articles that we collect around the web.
Three Station Design for Vacuum Brazing Furnaces
The brazing furnaces made by TAV VACUUM FURNACES are ideal for the automotive
industry because their design is composed of three distinct stations. These are:
- A precision heating furnace
- A functional loading station
- A useful cooling station
To understand how these three stations function in ways which suit the vehicle
manufacturing sector, we will deal with each in turn.
Heating Furnace Technology
Furnace Vessels
The vessel is an essential part of a furnace’s world-class heating process
technology. This is because it makes a separate enclosure that isolates the internal
section of the furnace.
Essentially, it contains the hot chamber and prevents
the outside environment from interfering with the brazing process.
In terms
of its design, the furnace has an extended horizontal axis, an elliptical shape,
ideal for many automotive heat treatments.
There are a pair
of flat doors, one at the front and one at the rear, for ease of access. These can
be operated manually. In addition, TAV's vacuum brazing vessels have a front door
which operates automatically.
This is used for both loading and unloading the
vessel.
Hot Chambers
The hot chamber in a heating furnace is constructed from high-quality panels
made of stainless steel with resistors fashioned from nickel-chrome. The hot chamber comes with dimensions of 180cm by 45cm by 365cm and inside there are in excess of 20 independently
controlled heating zones.
Together, these make the hot chamber extremely controllable
with the ability to fine tune the temperature, just as required.
In fact, maintaining the uniformity of heat in the chamber is extremely
important for automotive vacuum furnace applications.
Therefore, vacuum
furnaces should never vary by more than three degrees from the set temperature in
either direction. As this survey graph adequately demonstrates, the desired ±3°C temperature uniformity is achieved even with repeated use.
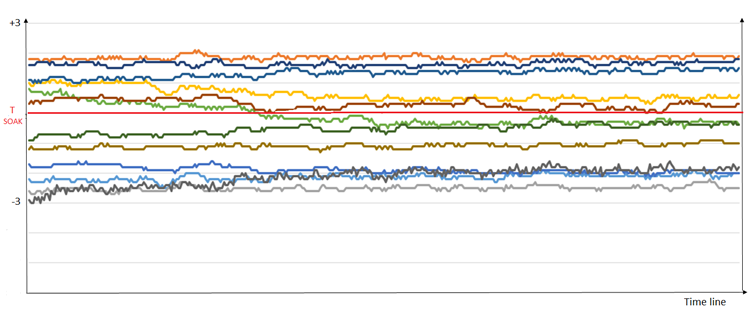
TUS example at a specific temperature with 12 TLC
Vacuum Systems
The final part of the vacuum furnace technology that should be discussed is the
vacuum system itself.
After all, it is this which allows the hot chamber and
the furnace vessel to do such a good job.
There are three pumping groups to
ensure a good vacuum is maintained while the furnace is in use.
Two groups are
made up of pair of rotary piston pumps. One is a positive displacement
lobe pump, known as a Roots pump, and the other is an oil diffusion pump.
The
third pumping group comprises a conventional mechanical pump, another Roots
pump as well as a cryo-trap. These are deployed to remove unwanted humidity
in addition to any impurities that might be released into the chamber during a treatment.
Without a load, the vacuum level that can be achieved with this vacuum system
is an astonishing 10-6 mbar (range).
Loading and Cooling Stations
The other two stations needed to conduct vacuum brazing in a precise manner are
loading and cooling stations.
Expertly designed steel shelves fixtures hold the required parts. They help to
keep them together along with the filler metal that will be used for the brazing
process itself.
Any load from 900 kilos up to 2,200 kilos can be processed simultaneously
with these loading stations.
When a brazing heat treatment has been completed, the load is automatically transferred
to a cooling station chamber. This is where the processed metal joins can be cooled
down in a controlled manner with recirculated air.
Key Heat Treatment Considerations
Although you will, by now, have gained some useful insights into expert
automotive heat treatments in vacuum environments, it is also worth considering
a few other factors.
For example, prior to the required brazing temperature
being reached, it is essential that the load should be kept at a lower temperature
until all of the working oil plates from the heat exchangers has been removed.
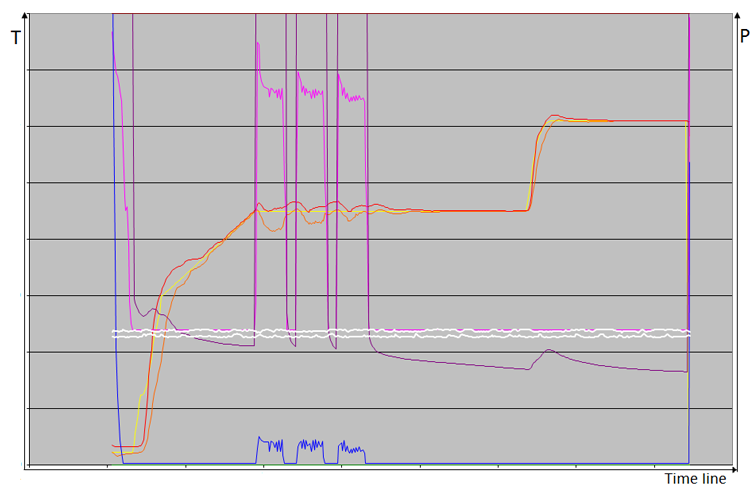
Typical brazing cycle. Line yellow is the setpoint, line
orange is the temperature TC, line blue is the high vacuum level and purple line
is the partial pressure in mbar detected.
Another factor comes after the brazing process itself.
After the brazing
step, the furnace reaches high nitrogen static partial pressure starting the cooling
phase, as indicated in the following graph. After completion, furnace's front door
opens automatically and loading station can be removed from within.
Conclusion
There are many applications that the automotive sector can put vacuum brazing
technology to. However, it is only reliable when high-performance vacuum furnaces
are used.
If you want more information leave a message here below and turn to
our expertise.
Do you need more info?
Write to our engineers and discover all the vacuum furnace applications for the automotive sector.