In the wide array of additive manufacturing technologies available today, Binder Jetting stands on its own for the ability to combine the flexibility and part complexity typical of the Additive Manufacturing processes with a productivity rate unmatched by other AM technologies.
Developed from a MIT patent from the early 1990s, Binder Jetting (BJT) is a powder-bed based process where, contrary to powder bed fusion technologies such as SLM and EBM, the material is compacted through the selective deposition of a liquid binder instead of melting.
That means Binder Jetting is able to process a wide array of materials including ceramics and polymers, even though the spotlight in the last few years certainly has been on the BJT production of metal parts.
To achieve their final strength and density, metal BJT printed parts then rely on sintering inside a sintering furnace.

TAV MIM5 Debinding and Sintering Furnace
In this article we’re going to go through the Binder Jetting workflow, compare it to other 3D printing and powder metallurgy processes and discuss what are the advantages and application fields of this technology.
What’s Binder Jetting?
Binder Jetting basically consists in the selective deposition of a liquid binder through a printing head, following the “slice” (i.e. the 2D section) of a CAD file. The build platform then lowers itself and a fresh layer of powder is spread by the recoater. The process is repeated layer after layer until the build is completed.

Workflow of the Binder Jetting production cycle
The printing head contains hundreds of nozzles, meaning that a high volume of binder can be deposited rapidly still maintaining an high accuracy and resolution of the parts.
Usually, BJT parts do not need specific supports since the workpiece is already supported by the loose powder inside the building volume.
As already mentioned, Binder Jetting is a “cold process” because no melting of the material is involved , and for this reason there’s no need for pre-heating of the powder bed to avoid cracking or distortion of the part, even though heat can be applied after the processing of a layer to accelerate the drying of the binder.
After printing the entire powder bed is cured at low temperature (around 200°C) to further dry and compact the part while still surrounded by the loose powder.
For its characteristics, this process could be applied virtually to any metallic powder, even though some requirements in term of powder flowability and particle size distribution are present to ensure a homogeneous spreading of the powder, good wettability with the binder, good surface roughness and sufficiently high final density of the part. At the moment, the most common metals for metal binder jetting production are probably the austenitic 316L stainless steel and the martensitic 17-4 PH stainless steel. Other qualified materials available from machine producers include 304L stainless steel, Inconel 625 and Inconel 718, H13, D2 and M2 tool steel, Ti6Al4V titanium alloy and copper.
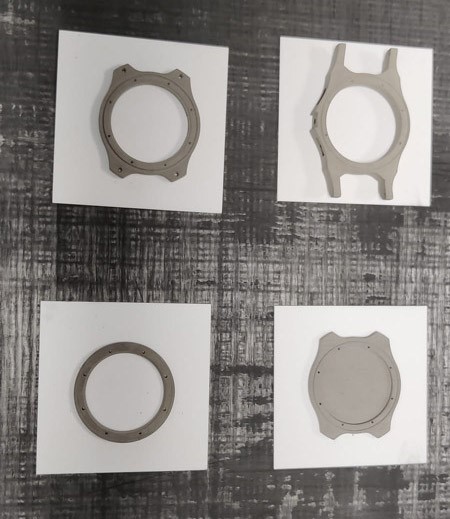
Watch parts in the green state, printed with ExOne X1 25PRO BJT machine (courtesy of Cor.Sa 3D)
Finally, after the curing step, the part needs to go through an infiltration or sintering cycle to achieve its final mechanical properties.
Infiltration consists in densifying the part through the introduction of a different material which does not deteriorate the property of the base metal. Typically, steels are infiltrated using copper, which penetrates inside the open pores allowing to obtain a good final density.
Instead, the only way to obtain a tough and dense single-alloy metal part is through sintering, i.e. keeping the part at an adequate temperature for an adequate time to promote atomic diffusion between the powder particles and fuse them together.
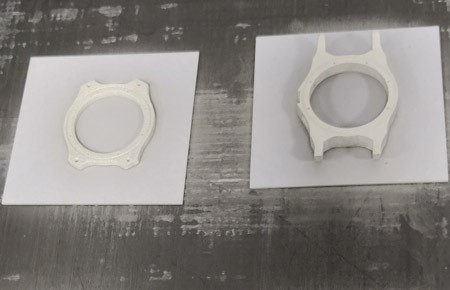
Sintered watch parts, printed with ExOne X1 25PRO BJT machine and sintered in TAV MIM3 vacuum furnace (courtesy of Cor.Sa 3D)
Transforming good looking parts into strong parts: the sintering process
Vacuum sintering furnaces are usually the go-to choice for sintering of Binder Jetting parts, thanks to the ability to provide bright and shiny sintered parts, the tight process parameters control and the possibility to work with different debinding and sintering atmospheres.
Sintering cycles for BJT parts include low temperature soaks to burn off all the cured binder residuals. For the organic liquid binders typically used in binder jetting, the evaporation starts at around 200°C and is completed before the furnaces temperature reaches 500°C, even though this temperature interval can be slightly affected by the actual binder composition and debinding atmosphere. Proper debinding parameters are critical to avoid cracking, deformations or the formation of carbon-based binder residual that will lead to carbon diffusion inside the part hindering the corrosion resistance and worsening the final part properties. For high volume production, it is also possible to carry out this step in a dedicated debinding furnace, that will increase productivity and facilitate the cleaning process. In any case, whether the choice is to use separated furnaces for debinding and sintering or to carry out the entire process in a single-step debinding and sintering furnace, it is important that the furnace is equipped with a proper trapping system to prevent the vaporized binder from reaching the vacuum pumps. If you want to discover more about debinding and the characteristics of a state of the art debinding furnace, check out our article on “HOW TO PROPERLY DEBIND PARTS PRODUCED BY METAL ADDITIVE MANUFACTURING”.
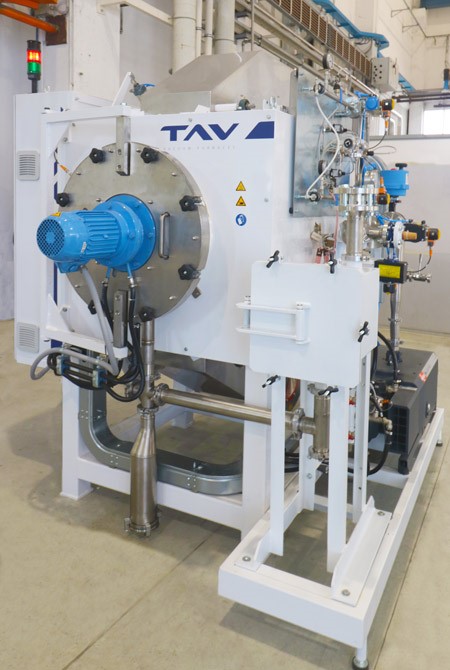
TAV D3 Debinding Furnace
Sintering parameters (i.e. time and temperature) should be fitted to the part material and size. Sintering cycle should also include intermediate dwellings and different heating rates to maximize temperature homogeneity on the part while minimizing cycle time. In general, most of the Metal Injection Molding (MIM) best practices regarding sintering can be transferred to Binder Jetting even though effects such as shrinkage and deformations must be kept under consideration even more carefully for Binder Jetting parts as, this technology allows to produce larger parts with a more complex geometry. Moreover, the different production method doesn’t make use of external pressure during the forming stage, leading to parts with a higher tendency to lose shape during sintering. Sintering of BJT parts in vacuum furnaces can be carried with different atmospheres, including:
- Vacuum
- Nitrogen or Argon
- Nitrogen/Hydrogen or Argon/Hydrogen mixtures
- Pure Hydrogen (both at low pressure, below 10 mbar and in overpressure, slightly above 1 bar)
The choice of sintering atmosphere should be fitted to the material and to the desired part properties. To have more insight into the choice of sintering atmosphere, check out our article VACUUM SINTERING OF STAINLESS STEELS: HOW TO CHOOSE THE RIGHT SINTERING ATMOSPHERE.
Both graphite and all metal vacuum sintering furnaces are suitable: the choice should be made, again, keeping into consideration the part material and the final applications. All Metal vacuum sintering furnaces are the go-to choice for oxygen-sensitive materials (such as titanium) allowing for more material versatility. On the other hand investment and operating costs are in favor of graphite vacuum sintering furnaces. Moreover, vacuum sintering furnaces usually include a multi-level retort, such as state of the art TAV MIM-Box, to maximize loading capacity inside the useful volume. Similarly, to what previously discussed for the hot zone, TAV MIM-Box is also available in both graphite and all metal configuration. If you want to discover more about the differences between metal and graphite hot zone vacuum sintering furnaces we invite you to read our STEP BY STEP GUIDE TO VACUUM SINTERING.
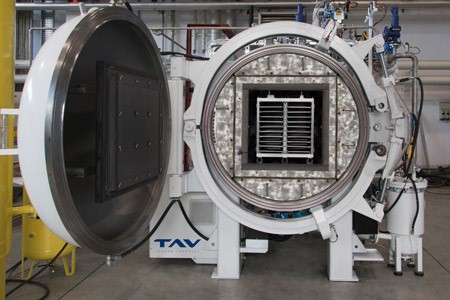
Hot Zone and MIM-Box of the TAV MIM5 Debinding and Sintering Furnace
The Binder Jetting Industry today
If we only consider metal parts production, at the moment there are only few manufacturers of Binder Jetting machines: ExOne, Digital Metal and Desktop Metal, even though HP and GE Additive have also been developing a BJ system for some time that are expected to be released in the near future.
The peculiarities of Binder Jetting makes it a competitive technology compared to other processes both inside and outside the Additive Manufacturing world.
The layer-wise nature of BJT allows it to have the same design freedom typical of the Powder Bed Fusion processes. Compared to PBF processes, the cost per part when operating at production rate is certainly lower. Moreover, being a “cold” process, BJT doesn’t induce residual stresses inside the part that require further heat treatment, as is the case with PBF. On the other hand, optimization of the Binder Jetting production process requires not only good knowledge of the printing phase but also of the debinding and sintering post processing. At the moment, the number of Binder Jetting systems installed worldwide is comparatively much lower than PBF systems, even though the technology has been around for more than two decades. The larger diffusion of PBF systems also means that lots of studies are available on those technologies, allowing for a deeper understanding of the process and post process parameters. Finally, the presence of published standards for PBF processes has certainly helped the growing of on-field applications for PBF parts in the aerospace, automotive and biomedical industries, while BJT parts applications are still mostly limited to consumer products.
Metal Injection Molding (MIM) is undoubtedly the most common powder metallurgy process for the production of small to medium-sized component. MIM allows to produce parts in a wide array of metal alloys (we can state that all of the metal alloys that are available today for BJT have been part of the MIM industry for quite some time) with very good resolution of the features and surface finishing. However, MIM has some limitation on the design complexity related to the impossibility to mold certain features (inside cavities, undercuts, internal bores, spirals, sharp edges, …). Moreover, the latest generation BJT machines can produce parts that are quite larger than typical MIM produced parts, even though size constrains for both technologies are more related to the available equipment and sintering than the process itself. Cost per part for low volume production is unquestionably in favor of Binder Jetting, which allows for unlimited product flexibility at virtually no costs. For high volume production however production costs are still in favor of Metal Injection Molding. We can expect to find the break-even point for cost production between the two technologies between 10.000 and 30.000 produced parts, depending on part characteristics. Finally, another interesting aspect to be reviewed is response time to new demands. With Binder Jetting, new designs can be implemented and produced in few hours, while MIM requires at least few weeks for the preparation of the dedicated tooling, which gives the edge to BJT for the production of prototypes, critical spare parts or, in general, parts requiring a very low lead time. That’s why increasingly more MIM companies are adopting Binder Jetting not as an alternative, but as a complementary technology to help covering all the market demands.
An interesting alternative to BJT is given by Material Jetting (MJT), where droplets containing both the base material and the binder are selectively jetted altogether. Metal MJT is a quite new technology, that at the moment has only been patented and commercialized by the Israel based company XJet through their NanoParticle Jetting technology. The main advantages of MJT are related to the ultra-thin layer thickness and the subsequent high part resolution, thanks to the nanoscale dimensions of the particles that are being jetted, and the ease of handling of the feedstock which, not containing any sort of loose powder, is exempt from any particular safety requirement.
Conclusions
Binder Jetting has unquestionably evolved from a promising technology, mostly limited to prototyping, to a serious alternative for both conventional subtractive manufacturing and additive manufacturing.
It has to be expected that, with the diffusion of Binder Jetting and the growing experience on the technology, a deeper knowledge of the design for BJT, the process parameters and the optimization of the sintering cycles will spread among the industry.
In the meantime, relying on experts from the powder metallurgy and sintering industry, such as TAV VACUUM FURNACES, will certainly accelerate the learning curve of new Binder Jetting adopters, helping them make the most out of the technology.
TAV VACUUM FURNACES would like to thank Cor.Sa 3D for its contribution to this article.