Today, with industry so focused on the bottom line, the cost of downtime has a big impact on profitability. If furnace starts to wear, it is possible to start producing parts with unacceptable quality and not know it for a long time. Eventually, machine wear will seriously affect not only productivity but also product quality. Regularly scheduled inspections and maintenance is a critical requirement of keeping your vacuum furnace running at peak efficiency.
The term “if it’s not broken, don’t fix it” still applies to many industries. But furnace maintenance plays a key role in quality assurance, which is another basis for the successful competitive edge of your company. Lack of maintenance or inadequate maintenance can result in production stops, late shipments to customers, and significant costs for emergency repairs.
Due to increasing costs of downtime, I want to emphasize on the importance of maintenance to the ongoing success of a business. In the first part of the article, I will explain you the advantages and the indeed vital necessity of preventative maintenance routines to making sure that your downtime stays at a minimum and your furnaces remain in tip top shape.
What is Preventative Maintenance (PM)?
Preventative maintenance is designed to retain the healthy condition of equipment and prevent the development of conditions that lead to failures. It refers to regular, routine maintenance to help keep furnace up and running, preventing any unplanned downtime.
Preventive maintenance involves the systematic inspection of furnace where potential problems are detected and corrected in order to prevent equipment failure before it happens. In practice, a preventive maintenance program may include things such as lubrication, cleaning, oil changes, adjustments, repairs, replacement of minor components (e.g. drive belts, gaskets, filters, o-rings, etc.), and partial or complete overhauls that are regularly scheduled. The exact preventive maintenance required will vary based on operation and type of furnace.
But PM includes much more than simply performing regular maintenance on vacuum furnace. It also involves maintaining accurate records of every inspection and servicing, as well as knowing the lifespan of each component to understand the replacement frequency. These records can help maintenance technicians anticipate the appropriate time to change each part and can also help diagnose problems when they occur.
Preventative maintenance is crucial to keep the performance of your vacuum systems optimal. By performing maintenance at regular intervals, furnace life can be extended dramatically and reduce the number of major mechanical failures that occur. Timely repair of known faults reduces the likelihood of emergency breakdowns.
Preventive Maintenance vs Corrective Maintenance
By performing a regular preventive maintenance, you are assured your vacuum furnace remains to operate under safe conditions, both for the machine and the operators. Possible issues can be nipped in the but before they have a chance to cause harm. Ideally, a PM schedule will prevent all equipment failure before it occurs. Reactive or corrective maintenance involves the repair or replacement of components which have failed or broken down. It is carried out after a fault is detected to restore normal operating conditions.
Corrective maintenance is done AFTER problem while preventive is BEFORE problem. Preventative maintenance is designed to prevent unplanned downtime by reducing corrective maintenance of vacuum furnaces. Preventative maintenance reduces reactive maintenance, resulting in lower cost. In essence, you will repair things less often if you be proactive and head off those expensive disasters. You pay penalties when you respond to problems rather than preventing those problems.
There are a variety of costs associated with unplanned outages, such as lost production, overtime, idle equipment, expedited shipments, and other hidden costs. When we leave a potential disaster just waiting to happen, maintenance can end up costing more in the long run. So, now let’s just wait and see how corrective maintenance adds up to a costly problem for your company.
Did you like this article up to here?
Before you continue, follow us on our LinkedIn page pressing the button here below!
In this way, we'll be able to keep you updated on most advanced technologies for heat treatments not only with our posts, but also with the best articles that we collect around the web.
Reactive maintenance: what are the hidden cost?
When we talk about reactive maintenance, it is understood that the equipment has broken down and that the intervention is intended to restore the unit to its proper state. Reactive maintenance deals with existing failures, whether they are mechanical, electrical, or controls-related. The aim is to temporarily repair the defect in order to be able to use the furnace again in the shortest time possible. The cost of repair is determined by a number of factors, such as response time, repair time, and stock availability.
But the cost of breakdown repair extends far beyond the repair labour and materials. Because a breakdown is never planned, it causes production to stop for an undetermined period. And, as Murphy’s Law would have it, it’s usually at the worst time of the month or the busiest time of the day. For every minute that production stops, your company is losing money. It may miss deadlines, which impacts the rest of the supply chain and can increase the risk of losing customers. It’s no surprise then that the true cost of a machine breakdown has been estimated as between five to eight times the maintenance costs.
Higher costs occur when a greater loss of production is incurred and it takes more time, resources and materials to correct the problem than it did to prevent it. It’s not only the downtime that costs the business; the hidden costs of reactive maintenance include:
- uncontrollable and unpredictable budget costs;
- shorter life expectancy for furnace;
- repeat failures and breakdowns;
- employees’ idle time;
- potential safety issues.
When preventative maintenance is scheduled, these costs can be avoided.
A planned preventive maintenance may cause small nuisance for production, but that is nothing compared to actual furnace downtime caused by a breakdown. Because it is planned, production can propose the optimal time for short-term and long-term maintenance scheduling.
PM procedures take less time than emergency repairs and replacements. Unplanned downtime could cost thousands of euros, not to mention if you end up have to replace the furnace what that cost would be. With regular maintenance, your vacuum furnaces can run safely and reliably for decades.
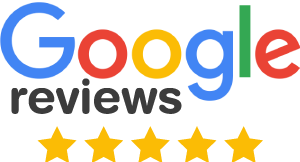
Do you like this blog?
For us your opinion matters, so we would be very pleased if you could write a review about us or our blog.