La Manifattura Additiva (AM) è uno dei vari processi di creazione di oggetti
solidi tridimensionali da un file digitale.
A differenza dei metodi di manifattura sottrattiva che iniziano con un solido
blocco di materiale e poi tagliano via l'eccesso per creare una parte finita,
la produzione additiva crea una parte (o caratteristiche delle parti) strato per
strato dalla geometria descritta nel modello di un progetto 3D.
Per molti decenni, i processi AM sono stati utilizzati per la prototipazione
rapida. Negli ultimi anni, la manifattura additiva ha riscosso un incredibile
interesse in tutte le sfaccettature del settore: dalle applicazioni aerospaziali
alle semplici realizzazioni domestiche una tantum dei consumatori. Questa tecnologia
ha immensa versatilità e flessibilità, grazie alla sua capacità
di creare geometrie complesse con proprietà personalizzabili dei materiali. La manifattura additiva offre una grande libertà nel design: oggetti di
qualsiasi forma o geometria sono prodotti da un modello 3D o da un progetto inserito
nella stampante 3D da un computer.
La manifattura additiva dei metalli consente di progettare
e costruire parti leggere in tempo reale, poiché i modelli 3D possono
essere stampati o fabbricati direttamente utilizzando una sorgente laser
o una sorgente a fascio di elettroni e un letto di polvere. La stampa 3D
in metallo può produrre parti altamente personalizzate con funzionalità
migliorate che non sono possibili attraverso i processi tradizionali.
La stampa 3D in metallo è una tecnica AM che include processi come la
fusione laser selettiva (SLM), in cui la polvere
metallica fine viene fusa strato per strato per creare parti metalliche tridimensionali.
Inoltre, la fusione selettiva del laser, in particolare, consente la produzione
di componenti con cavità e sottosquadri, con pareti sottili e vuoti nascosti.
La fusione laser selettiva di diversi tipi di leghe si adatta
perfettamente alle esigenze delle applicazioni leggere coinvolte nella tecnologia
dei veicoli e dei motori. La miscelazione di diverse materie prime come titanio,
alluminio, acciaio inossidabile o leghe a base di nichel e la scoperta di nuove
leghe con varia forza e resistenza alla temperatura, è quasi impossibile
attraverso i metodi di produzione convenzionali.
Questo articolo fornisce spunti per aiutarvi a comprendere il potenziale dei
trattamenti termici nel vuoto per parti stampate in 3 dimensioni,
con particolare attenzione alla SLM (fusione laser selettiva) del
Ti6Al4V.
Manifattura additiva: benefici e principi funzionali
La manifattura additiva è una tendenza tecnologica dirompente che influenzerà
il futuro dell'industria manifatturiera. Secondo il rapporto annuale sulla
AM di Wohlers Associates, il fatturato globale del settore della stampa
3D di prodotti e servizi di manifattura additiva ha superato i 2,2 miliardi
di dollari nel 2014. Il mercato globale per la stampa e i servizi 3-D dovrebbe superare
i 21 miliardi di dollari entro il 2020.
Concettualmente, la AM è costituita da un modello CAD digitale di una
parte che viene convertito in una parte tridimensionale solida semifinita.
Nella fusione laser selettiva (SLM), una delle tecnologie emergenti AM, una polvere
metallica viene fusa da un raggio laser concentrato comandato dal computer per formare
la parte. Questo processo ha un tasso di deposizione inferiore rispetto ad altre
tecnologie AM ma si ottiene un prodotto più dettagliato.
Le possibilità e i benefici della SLM (fusione laser
selettiva) sono molti e stimolanti. Il vantaggio più importante è
il fatto che solo il materiale necessario per realizzare il pezzo viene effettivamente
processato. Pertanto, per la produzione sarà necessario meno materiale di
input. Inoltre, a differenza della manifattura sottrattiva, la manifattura additiva
non ha vincoli di progettazione sulla geometria della parte e consente la libertà
di progettare per funzionalità. Infine, la manifattura additiva consente
lo sviluppo di una parte per arrivare con grande velocità sul mercato.
Potenziale dei trattamenti termici sottovuoto per le parti AM
I metalli che vengono elaborati tramite il metodo SLM sono già numerosi
e includono leghe di titanio, inconel, alluminio, acciaio cobalto-cromo, ecc. Tipicamente,
il processo SLM viene eseguito all'interno di una camera inerte al fine di
controllare l'ossidazione della sorgente metallica interessata dal calore.
Poiché le parti prodotte con la manifattura additiva sono
semifinite e hanno geometrie complesse che sono anche impossibili da lavorare, la
regola è minimizzare la rimozione del materiale durante l'elaborazione
a valle. Pertanto, le parti finite non devono mai presentare decarburazione o superfici
contaminate dalla successiva lavorazione termica. Un forno in vuoto
ben mantenuto che funziona totalmente privo di ossigeno, dotato di pompe di diffusione
per raggiungere livelli di vuoto profondi e con controlli di temperatura molto precisi, è
quindi un componente fondamentale all'interno del mondo della manifattura additiva.
Inoltre, poiché nella maggior parte dei casi è desiderabile produrre
parti senza sollecitazioni interne, le parti SLM vengono sempre trattate
termicamente dopo la fabbricazione. Sono previsti trattamenti termici aggiuntivi
per ottimizzare il comportamento meccanico, ad esempio l'allungamento al cedimento,
la resistenza a fatica, ecc.
Le proprietà meccaniche affidabili sono un prerequisito essenziale per
la produzione in serie di componenti industriali. È noto dalla letteratura
che AM genera nuove sfide in termini di proprietà dei materiali a causa del
rapido raffreddamento, dei difetti o della ruvidità superficiale intrinseca.
Mentre i valori di resistenza alla trazione sono stati ben caratterizzati per diversi
trattamenti termici e condizioni superficiali, una complessità significativa
si presenta se i fattori di influenza sulle prestazioni alla fatica
devono essere determinati.
L'eccellente resistenza e tenacità, combinata con la resistenza alla
corrosione, il basso peso specifico e la biocompatibilità della lega
di titanio Ti-6Al-4V, lo rendono ideale per molte applicazioni di ingegneria
ad alte prestazioni nel settore aerospaziale e automobilistico, ed anche per la
produzione di impianti biomedici.
Vediamo ora il comportamento alla fatica di SLM Ti6Al4V e l'influenza del
tipo di trattamenti termici dopo il processo SLM.
Ti è piaciuto fino a qua l'articolo?
Prima di continuare nella lettura, seguici sulla nostra pagina Facebook cliccando il pulsante qui sotto!
In tal modo rimarrai aggiornato sulle tecnologie più avanzate per i trattamenti termici non solo con i nostri articoli, ma anche con le migliori pubblicazioni che raccogliamo in giro per la rete.
Microstruttura di SLM Ti6Al4V dopo i trattamenti termici
La microstruttura di Ti6Al4V prodotta con il processo SLM è
diversa dalle controparti battute o colate. È caratterizzato da una solidificazione
direzionale e un raffreddamento nella direzione della costruzione. La solidificazione
direzionale e il raffreddamento fanno sì che i grani crescano nella direzione
di costruzione attraverso gli strati, risultando in una microstruttura colonnare.
Questa microstruttura colonnare conferisce al materiale stampato proprietà
meccaniche anisotropiche dove le proprietà nella direzione di costruzione
(z) possono essere molto diverse dalle proprietà nel piano perpendicolare
alla direzione di costruzione (x, y).
Figura 1
a) Microstruttura colonnare dopo trattamento
termico antistress (SR)
b) Microstruttura uniforme e fine dopo trattamento termico
ad alta temperatura in vuoto (VT)
Quando un trattamento termico di distensione in Argon a 380°C
viene applicato, le sollecitazioni interne sono ridotte ma la microstruttura colonnare
grossolana rimane inalterata, vedi Fig. 1a. D'altra parte, il trattamento termico
ad una temperatura più elevata (740°C per 2 ore) in un forno
a vuoto elimina le tensioni residue e modifica la microstruttura in una
più fine ed equiassica, vedere Fig. 1b.
Comportamento alla fatica di SLM Ti6Al4V dopo i trattamenti termici
Un programma di test di fatica di SLM Ti6Al4V è stato
effettuato utilizzando una geometria rotazionale standard del campione di flessione
e un nuovo metodo di prova a fatica utilizzando campioni miniaturizzati. Il nuovo
metodo è stato sviluppato con l'obiettivo di ridurre al minimo il costo
dei programmi di test di fatica (cioè il volume dei mini campioni è
circa 1/7 di quello del campione di piegatura standard) garantendo al contempo una
maggiore flessibilità di utilizzo, ovvero valutazione della superficie, direzionalità
e effetti notch. La Fig. 2 dimostra che il nuovo metodo di test con mini campioni
fornisce risultati di fatica coerenti con i dati ottenuti dai campioni standard.
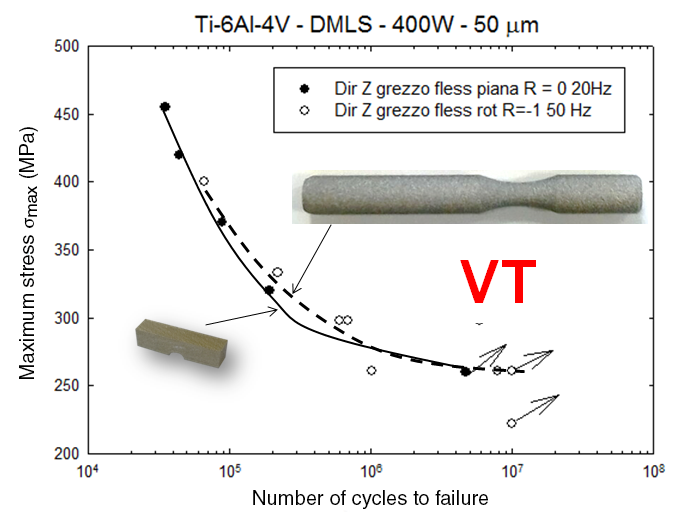
Figura 2
Curve di fatica di SLM Ti6Al4V finali dopo
il trattamento termico in vuoto (VT) ottenuto utilizzando una geometria campione
standard e una geometria di provino in miniatura.
L'influenza del trattamento termico sulla fatica è
discussa con l'aiuto di Fig. 3. Dati di prova per i tre orientamenti dei provini
dopo un trattamento termico di distensione (SR). La dispersione nei dati è
piuttosto bassa e le curve di tendenza della fatica si comportano bene. Tuttavia,
le vite dei campioni con asse lungo parallelo alla direzione di costruzione (asse
Z) sono notevolmente diverse e più corte rispetto agli altri due orientamenti
dei campioni (1 e 2) con l'asse lungo perpendicolare alla direzione di costruzione. È
dimostrata e quantificata la presenza di un comportamento anisotropico della fatica
di DMLS (Direct Metal Laser Sintering) Ti-6Al-4V dopo il trattamento
di riduzione dello stress (SR) dovuto alla struttura colonnare di Fig.
1.a.
I dati dei test per i tre orientamenti dei mini campioni dopo il trattamento
termico in vuoto (VT) ad alta temperatura sono mostrati nello stesso grafico
di Fig. 3. La dispersione dei dati è ancora bassa, ma tutti e tre i set di
dati dei campioni, indipendentemente dalla direzione dell'asse lungo, sono
molto simili e dimostrano un comportamento isotropico alla fatica della struttura
equiassiale di Fig. 1b. Inoltre, le curve rappresentative mostrano un significativo
incremento della resistenza a fatica del materiale VT rispetto al peggiore materiale
SR.
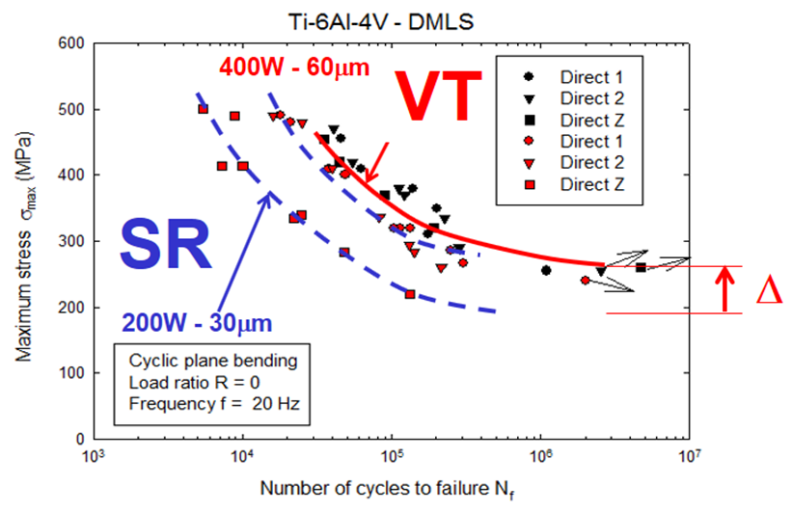
Figura 3
Curve di affaticamento direzionale di SLM
Ti6Al4V finali dopo il trattamento termico per la distensione in Argon (SR) e dopo
trattamento termico in vuoto (VT) utilizzando campioni in miniatura
Spero che questo articolo dedicato principalmente alla fusione laser selettiva
(SLM), il processo di stampa 3D utilizzato per creare stampe 3D
in metallo, vi sia piaciuto. Se avete domande sulla manifattura
additiva o sui trattamenti termici sottovuoto, fate un commento qui sotto
e vi risponderò.
Date un'occhiata anche alle diapositive qui sotto, che ho presentato di recente su questo argomento alla Metal Additive Manufacturing Conference organizzata da TAV VACUUM FURNACE.
Ti è stato utile l'articolo?
Aiutaci a diffonderlo in rete utilizzando Twitter.
A te basta solamente cliccare il pulsante qui sotto, ma a noi farai un enorme favore.