Additive manufacturing using metals and alloys
The term Additive Manufacturing (AM) refers to the process that allows the joining
of materials, using technologies that are also very different from each other and
according to a layer upon layer method (additive manufacturing), to make objects
(e.g. component parts, semi-finished products or finished products) starting from
3D digital models, as opposed to traditional production methods
(turning, milling, etc.) which instead require subtraction from a solid (Subtractive
Manufacturing).
The AM techniques require that the three-dimensional object is created starting
from computerized 3D models and using different materials including metal, plastic,
ceramic, composite or biological ones.
In the additive manufacturing of metals and alloys, these are used in the form
of powders or wires.
The raw material is selectively melted by a focused heat source and then consolidated
during cooling, to finally form the designed piece.
The processes of AM that more than others employ metallic materials, are those included
in the categories Powder Bed Fusion (PBF) and Direct Energy Deposition
(DED), in particular: Selective Laser Melting (SLM), Direct Metal Laser
Sintering (DMLS), Electron Beam Melting (EBM), Laser Engineered
Net Shaping (LENS), Direct Metal Deposition (DMD).
Among the commercial metallic materials currently available to be processed through
AM processes there are: pure Ti, Ti-6Al-4V alloy, some stainless steels such as
316L, and PH 17-4, maraging steel 18Ni300, the AlSi10Mg alloy, CoCrMo alloys and
Ni-Cr Inconel 625 superalloy.
To the list just proposed, the materials shown in Table 1 can be added.
Titanium |
Aluminum |
Tool steels |
Superalloys |
Stainless steels |
Refractory |
ELI Ti |
6061 |
H13 |
IN718 |
316 |
MoRe |
TiAl |
|
Cermets |
Stellite |
420 |
Ta-W |
CP Ti |
|
|
|
347 |
Alumina |
Table 1 - Metallic materials for AM
Precious metals, such as gold, silver and platinum have been indirectly treated,
that is molds for the lost-wax casting technique have been made using 3D printing,
in which the cited materials have been cast; the same materials are also used directly,
for example, with the SLM technique.
Among the metallic materials just listed, stainless steels are those that find application
in the greatest number of sectors: aerospace, medical,
energetic, automotive, naval,
etc.
The mechanical characteristics (resistance to static and dynamic stresses) and
the density of the pieces produced by additive manufacturing with these materials
have long been studied and are currently very high, that is, similar if not higher
than those of traditionally manufactured parts. Their resistance to corrosion is
less well known and investigated. This property is fundamental in specific applications,
such as, for example, those in the nautical sector.
Study of the corrosion resistance of metal parts made with AM: characteristics
of the studied materials and the analysis carried out
To investigate the corrosion behavior of stainless steel parts produced
by additive manufacturing, the Metallurgy section of the Department of
Chemistry and Industrial Chemistry (DCCI) of the University of Genoa in collaboration
with TAV VACUUM FURNACES, the Saiem Srl company of Cairo Montenotte (Savona) and
the CNR-ICMATE of Padua started the study of 316L steel samples made using the SLM
technique (Selective Laser Melting). Specifically, Saiem Srl has
produced a series of samples, of dimensions 1x1x1 cm3 (Figure 1) using
the TRUMPF Tru Print 1000 system and pre-bonded powders specially designed and tested
for use with the cited 3D printer.
As can be seen from the image (Figure 1), the pieces produced have surfaces with
different morphology and roughness.
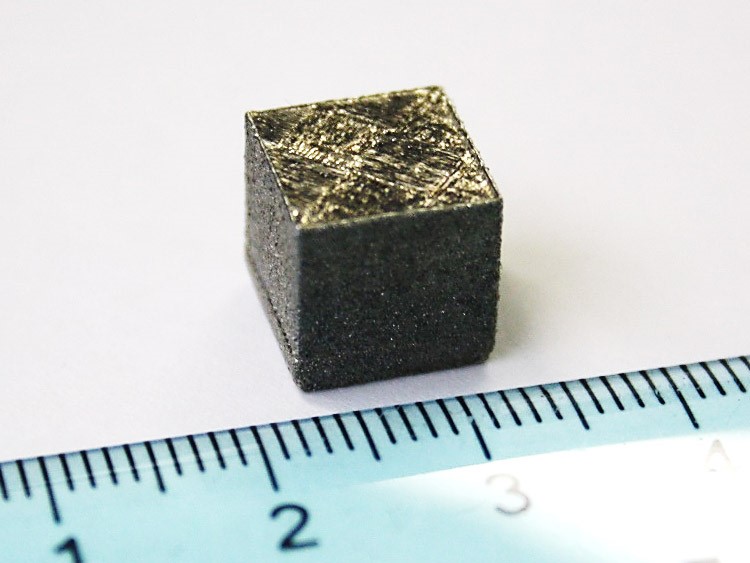
Figure 1 - Cube 1x1x1 cm3 realized through
SLM
The final made parts have the composition indicated in Table 2, corresponding
to that of 316L austenitic stainless steel (X2 CrNiMo17-2-2, DIN EN 10088-1).
Fe |
Cr |
Ni |
Mo |
Mn |
Si |
C |
N |
P |
S |
Bul. |
16.5-18.5 |
10.0-13.0 |
2.00-2.50 |
<2.00 |
<1.00 |
<0.030 |
<0.10 |
<0.045 |
<0.015 |
Table 2 - Chemical composition of the molded parts (wt.%)
For the study of microstructure and corrosion resistance, the samples were then
subjected to metallographic and electrochemical characterization, respectively,
the first through Scanning Electron Microscopy (SEM), Fluorescence
X-ray Spectroscopy and Optical Bright Field Microscopy
(LOM-BF), the second by means of Potentiometric Analysis is
Electrochemical Impedance Spectroscopy (EIS).
Part of the samples produced by Saiem Srl was further treated, that is, some cubes
were coated with TiN-based coating (both at TAV VACUUM FURNACES and at the CNR ICMATE
of Pd), others based on AlTiN (at the CNR) , others were subjected to a heat cycle.
The applied heat cycle, Figure 2, was performed at TAV VACUUM FURNACES.
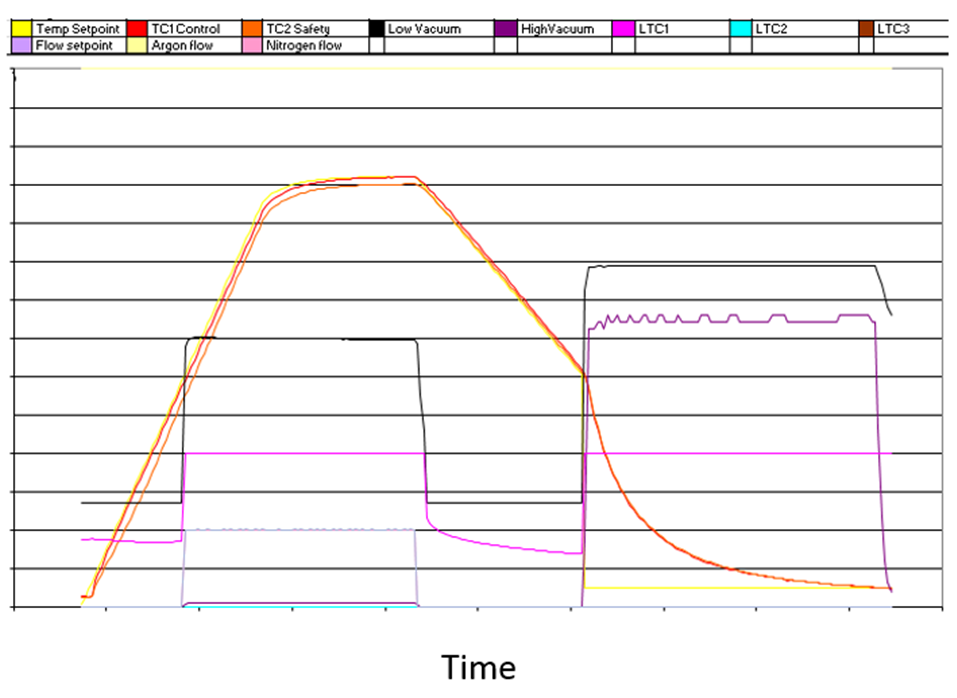
Figure 3. Applied heat cycle
Both the microstructural aspects and the corrosion behavior of these samples
(those coated with coatings of different composition or subjected to heat treatment)
were evaluated. In particular, it was decided to verify whether the treatments applied
resulted in an improvement or deterioration of the corrosion resistance of the studied
samples.
Did you like this article up to here?
Before you continue, follow us on our Twitter page pressing the button here below!
In this way, we'll be able to keep you updated on most advanced technologies for heat treatments not only with our posts, but also with the best articles that we collect around the web.
Laboratory results
Metallographic characteristics of the samples
The microstructural analysis concerned the longitudinal and transverse sections
of the "as they are" samples and the longitudinal sections of the samples
subjected to heat treatment.
The study of SEM and LOM-BF micrographs allowed to find a high density
of the produced pieces. There are few visible pores and characterized by
spherical shapes with a diameter between 1 and 10 mm (attributable to gases trapped
in the material during the production of the piece), or by irregular shapes (these
pores are due to the printing process itself and can have dimensions from macroscopic
to sub-micrometric).
The microstructure of the samples, investigated after attack with aqua regia
(HNO3:HCl:H2O 3:10:10 in volume), highlighted the presence of elongated and oriented
grains along the direction of the piece construction, corresponding to the direction
of the heat progress (Figure 4), single melting pools, with dimensions
of about 100 mm along the horizontal axis, twin grains and a cellular structure
in which the intracellular spaces are less than 1 mm (Figure 5).
The microstructure just described, especially the observed cellular structure,
is typical of metal parts produced by additive manufacturing techniques,
characterized by solidification processes with high cooling speeds and a high degree
of subcooling.
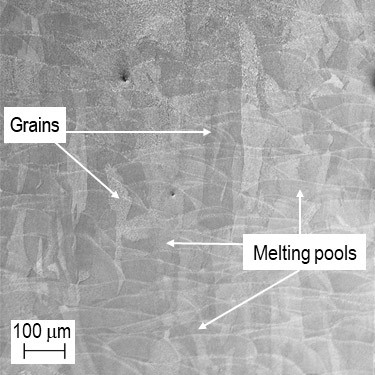
Figure 4 - SEM-SE: Microstructure of the sample
along the longitudinal section after attack with aqua regia (magnification
200x).
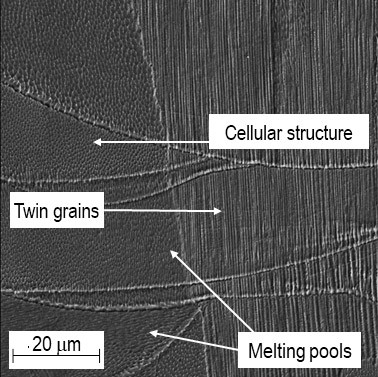
Figure 5 - SEM-SE: Microstructure of the sample
along the longitudinal section after attack with aqua regia (magnification
8500x).
In the case of samples subjected to heat treatment, the microstructure is different
from that found when observing the samples as printed, since it is characterized
by large grains and in which details such as melting pools, twin grains and the cellular structure, are no longer appreciable.
Electrochemical characteristics of the samples
The electrochemical measurements concerned the lateral and lower surfaces of
the sample produced by SLM in order to verify its corrosion behavior in relation
to a commercially used reference sample of 316L.
Electrochemical polarization tests
These measurements have shown a variable passive behavior, typical of a material
characterized by a surface oxidation film that greatly limits the corrosion kinetics
by acting on the anodic semi-reaction.
Comparing the sample obtained by SLM with a commercial 316L sample, minor pass intervals
can be noted for all exposed faces, that is the lower and lateral faces, with higher
corrosion current densities for the lateral face.
The major critical issues, found on the lateral surface, can be correlated to its
morphology and to the number and distribution of the porosities that determine additional
interface phenomena, to be further investigated.
Work continued with the assessment of the corrosion behavior of the "as is" side
face and of the same face subjected to various surface treatments and heat treatment.
Measurements showed that surface treatments resulted in greater protection of the
sample. In particular, among the treatments applied, the one that provided
the best protection was the one based on TiN deposited at TAV VACUUM FURNACES.
Electrochemical impedance spectroscopy (EIS)
Representing the massive sample, the lower surface of the sample printed using
SLM was considered, compared with a reference sample of AISI 316L. The EIS measured
for the lower surface was comparable to that obtained from the reference sample,
with a slight imbalance towards a better corrosion behavior on the part of the printed
sample.
The similarity between the results obtained is attributable to the comparable surface
finish, obtained in both cases by polishing with abrasive papers.
As regards the samples characterized by different surface morphology and subjected
to further treatments, the maximum resistance values were found for the sample coated
with TiN at TAV VACUUM FURNACES.
The best corrosion behavior is attributable to the nature of the applied layer and
to the best covering of the surface.
Conclusions
The analysis carried out has highlighted critical issues for the sample obtained
by SLM in relation to the type of the exposed surface.
The application of coating and the heat treatment
allowed to obtain good results from the point of view of the corrosion resistance.
This study project was a collaboration of
University of Genoa: P. Piccardo,
V. Bongiorno, R. Spotorno, G. Ghiara
SAIEM Srl: F. Fraternale, A. Ghiglia
TAV VACUUM FURNACES SPA: A. Fiorese
ICMATE-CNR: S. Battiston,
F. Montagner
Did you like the article?
Subscribe to our Telegram channel and stay up to date on most advanced technologies for heat treatments.
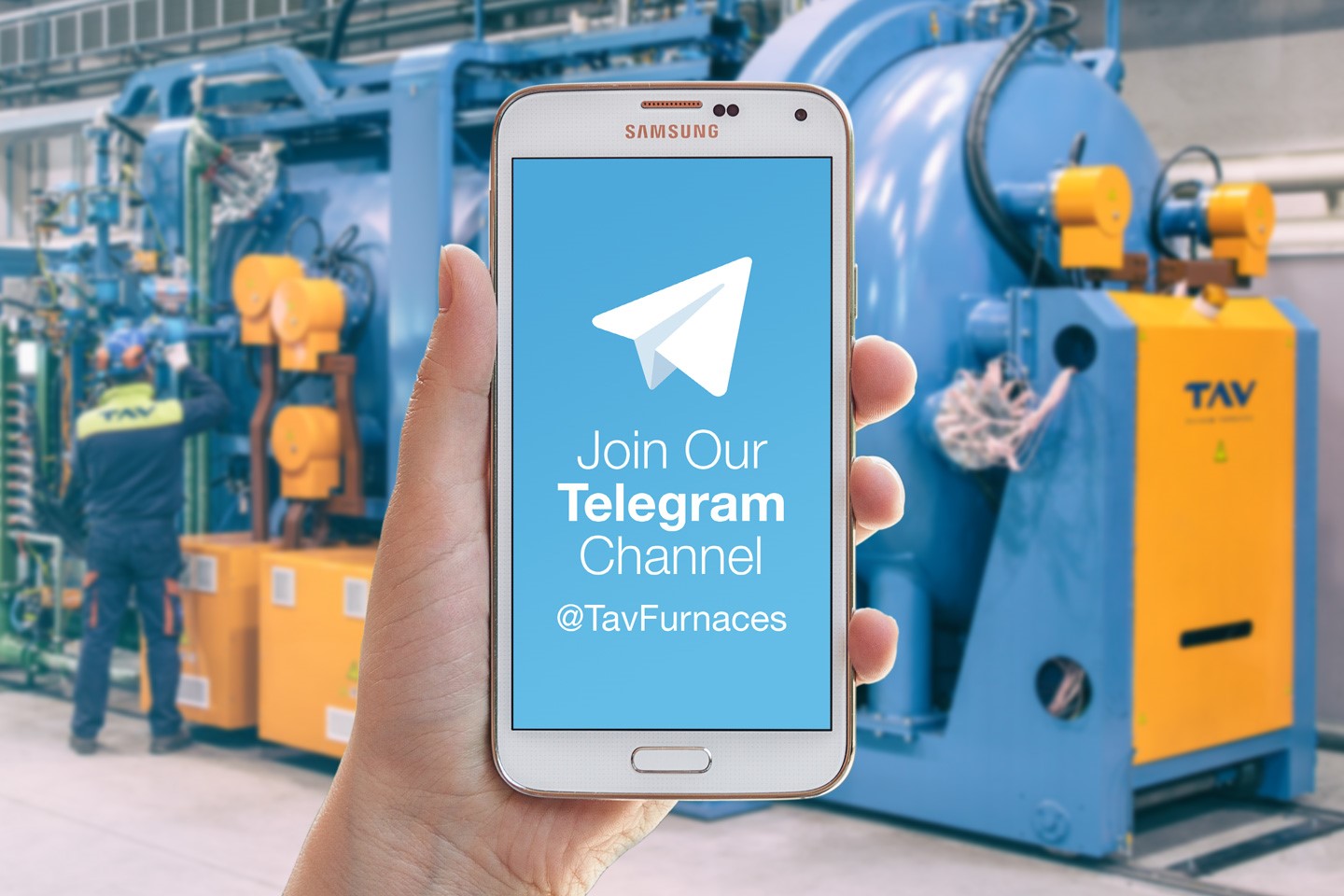
Don't you have Telegram?
If you do not have Telegram yet, use one of the following buttons to install it:
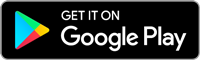
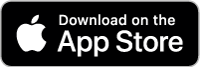