This article is available in English too.
Polveri per MIM e AM: a ciascuno il suo
Nell'introduzione di questo articolo abbiamo già discusso come diverse tecnologie di metallurgia delle polveri si affidino a forni in vuoto per fasi critiche del loro processo produttivo, menzionando la produzione additiva Metal Injection Molding (MIM), Binder Jetting (BJT), Powder Bed Fusion (PBF) e Direct Energy Deposition (DED).
Anche se queste tecnologie possono avere alcune applicazioni e aspetti tecnologici comuni, la polvere impiegata in ciascuna di esse ha alcune peculiarità che la differenziano dalle altre.
Scopriamo quali sono le differenze.
Additive Manufacturing
Le polveri per applicazioni di manifattura additiva PBF e DED sono solitamente prodotte tramite atomizzazione a gas o atomizzazione al plasma; il primo processo è senza dubbio il più diffuso, mentre il secondo è generalmente utilizzato per materiali reattivi.
Le polveri atomizzate a gas e al plasma, infatti, permettono di ottenere polveri con una qualità metallurgica molto alta, un basso contenuto di impurità e particelle di polvere quasi perfettamente sferiche.
Avere un controllo serrato sulle proprietà metallurgiche della polvere e sul contenuto di ossigeno e impurità è infatti fondamentale per le applicazioni aerospaziali e mediche, industrie che rappresentano uno dei più grandi mercati per i sistemi AM e che devono fare riferimento a severe normative riguardanti i materiali e le proprietà meccaniche delle parti prodotte.
Inoltre, la sfericità è molto importante per i processi PBF per ottenere un'alta densità relativa e migliorare la flowability della polvere, garantendone una distribuzione uniforme sulla piastra di stampa.
L'atomizzazione al plasma, nonostante i costi di produzione generalmente più elevati e la minore produttività, fornisce polveri della massima purezza, con una forma sferica precisa delle particelle e un contenuto minimo di satelliti. Viene solitamente applicata alla produzione di materiali reattivi, ad esempio metalli refrattari (come molibdeno, niobio, tantalio e tungsteno) e alle leghe di titanio, quando è richiesta la massima purezza (ad esempio per la produzione di Ti-6Al4V Extra Low Interstitial).

Figure 3: Parti AM in titanio prodotte utilizzando la fusione a fascio di elettroni (per gentile concessione dell'Oak Ridge National Laboratory, con licenza CC BY 2.0)
Per quanto riguarda la dimensione delle particelle, la distribuzione è solitamente più fine (nell'intervallo 20-45 µm) per il Laser-PBF rispetto all'Electron beam-PBF (nell'intervallo 45-100 µm) e ancora più grande per il DED (50-150 µm).
Da questo punto di vista, il Binder Jetting rappresenta un'eccezione; la natura stessa del processo BJT, infatti, che si basa su una miscela polvere-legante per creare green parts che vengono infine sinterizzate, fa sì che le polveri per il Binder Jetting siano molto più simili a quelle adottate nel Metal Injection Molding, di cui parleremo nel prossimo paragrafo.
Metal Injection Molding
Le polveri per applicazioni MIM sono solitamente prodotte tramite atomizzazione a gas o ad acqua. Tutte le leghe più comuni impiegate nel Metal Injection Molding possono essere prodotte utilizzando uno dei due metodi sopra citati, ad eccezione delle leghe di titanio che non possono essere prodotte tramite atomizzazione ad acqua, per le stesse ragioni discusse nel paragrafo precedente.
Come già detto, le polveri atomizzate con gas hanno alti livelli di purezza e sfericità.
In confronto, le polveri atomizzate ad acqua hanno di solito un contenuto di ossigeno più elevato e una forma più irregolare, ma con costi di produzione inferiori.
Anche se le particelle di polvere sferiche permettono di ottenere una migliore densità relativa, una polvere di forma irregolare offre alcuni vantaggi per le applicazioni MIM, aiutando i componenti a mantenere la forma originaria durante il debinding e la sinterizzazione.
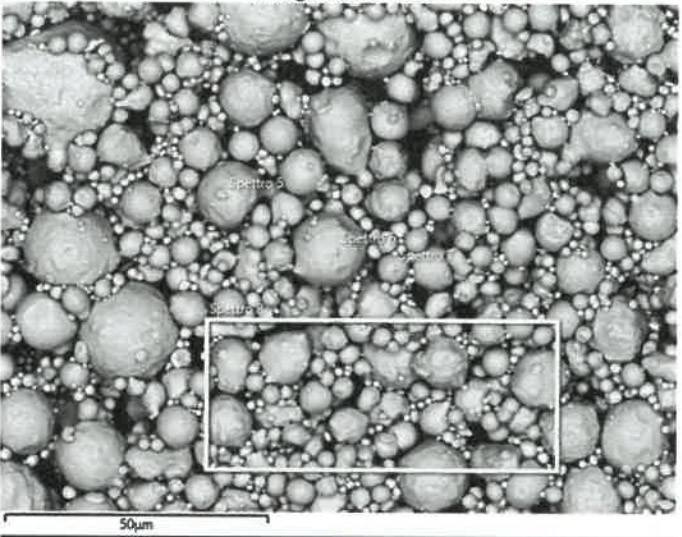
Figure 4: Immagine al SEM di un componente MIM prima della sinterizzazione che mostra la tipica distribuzione granulometrica della polvere impiegata nell'industria MIM.
Infine, le polveri per il MIM hanno di solito particelle di dimensioni comprese tra 5 e 25 µm, che si è dimostrato sperimentalmente essere l’intervallo dimensionale che fornisce il miglior compromesso tra particelle troppo fini, che si sinterizzano meglio ma si caricano male in un sistema contenente legante, e particelle troppo grosse, che viceversa non si sinterizzano ottimamente.
In conclusione, una buona conoscenza delle polveri metalliche permetterà di selezionare il miglior prodotto per l'applicazione specifica e i parametri di processo più adatti.
Inoltre, il risultato dei trattamenti termici per le parti prodotte tramite metallurgia delle polveri è strettamente legato alle proprietà della polvere stessa; una distribuzione subottimale delle dimensioni delle particelle, per esempio, non permetterà alle parti sinterizzate di raggiungere la loro massima densità.
Se sei interessato alla sinterizzazione in vuoto di componenti PM, dai un'occhiata alla nostra "Guida alla sinterizzazione in vuoto" e al nostro articolo su "Sinterizzazione sotto vuoto di acciai inossidabili: come scegliere la giusta atmosfera di sinterizzazione".
Per maggiori informazioni sui trattamenti termici delle parti prodotte tramite manifattura additiva invece, date un'occhiata al nostro articolo su "Perché trattare termicamente il metallo dopo la manifattura additiva?".