If you know even a little about vacuum heat treatments, for sure you’ve heard about vacuum heat treatment of titanium; in fact, being a particularly oxygen and hydrogen sensitive materials, titanium finds the perfect heat treating environment on vacuum furnaces.
In this article we will talk about a class of titanium alloys they might be less popular compared to commercially pure titanium or titanium Grade 5, but surely as fascinating and promising for demanding applications: beta titanium alloys.
Beta titanium alloys have an unique combination of desirable properties: their high specific strengths, creep resistance, oxidation and corrosion resistance, excellent temperature resistance up to 600°C and hardenability, make them very attractive for aerospace applications. On the other hand, the excellent biocompatibility and low elastic modulus, closer to that of human bone compared to other alloys, make Ti beta alloys an excellent material for biomedical applications.
During the last European Conference on Heat Treatments held in Genova on 29-31 May 2023, we presented a very interesting work developed by Department of Industrial Engineering of the University of Trento, Sisma S.p.a and TAV VACUUM FURNACES, aimed at exploring how vacuum heat treatments affect the mechanical properties of beta titanium parts produced using Laser Powder Bed Fusion.
Beta titanium alloys
Pure titanium undergoes an allotropic transformation upon heating, around 882°C, from an hexagonal close-packed (HCP) crystal structure, known as the α (alpha) phase, to a body-centered cubic (BCC) structure, the β (beta) phase.
Different alloying elements can act as an alpha or beta phase stabilizer, further broadening the range of existence of the alpha phase at higher temperature or enabling the beta phase to exist even at room temperature.
For this reason, titanium alloys can be divided, depending on their chemical composition, into: alpha and near-alpha alloy, alpha-beta alloys (such as the common Ti-6Al-4V or Grade 5), beta and near-beta alloys.
Phase diagrams of Ti alloyed with different alpha or beta stabilizing elements.
Beta and near-beta alloys in particular, contain sufficient quantities of beta stabilizers (such as molybdenum, silicon and vanadium) to make them metastable, allowing them to maintain the beta phase to room temperature when cooled rapidly after heat treatment in the beta region. Being Mo a well know Beta-stabilizer, the equivalent molybdenum content is often adopted as a rule to define beta alloys, where alloys having a Mo equivalent content higher than 10 are generally accepted as beta alloys.
Calculation of the equivalent Mo content for a titanium alloy.

Between the beta titanium alloys, Ti-15Mo-2.7Nb-3Al-0.2Si (or Titanium Beta 21S) was developed to have a good cold formability, oxidation and corrosion resistance thanks to the molybdenum and niobium content, coupled with high strength and creep resistance. For that reason, the alloy is very suitable for “warm” applications.
Laser powder bed fusion of beta titanium alloys
With the aim of producing high complexity titanium components, additive manufacturing (AM) technologies and especially Laser Powder Bed Fusion, are gaining increasing interest thanks to the possibility of decreasing the lead time and cost of production coupled with high design freedom and good tolerances.
Of course, the process used to manufacture Ti 21S parts has a profound effect on the final microstructure.
In particular, as-cast Ti 21S typically present a coarse microstructure of equiaxed beta grains containing dendrites, with a small amount of alpha precipitates formed during cooling.
In L-PBF Ti-21S instead, the extremely fast cooling rates, typical of the L-PBF process, allow to obtain a very fine microstructure of beta grains that are elongated and oriented in the building direction, following the local heat flow direction.
The significantly different microstructure of L-PBF Ti 21S compared to the as-cast material will also influence its response to heat treatment; for that reason, we tested the effects of different heat treatment strategies on Laser Powder Bed Fusion Ti 21S parts.
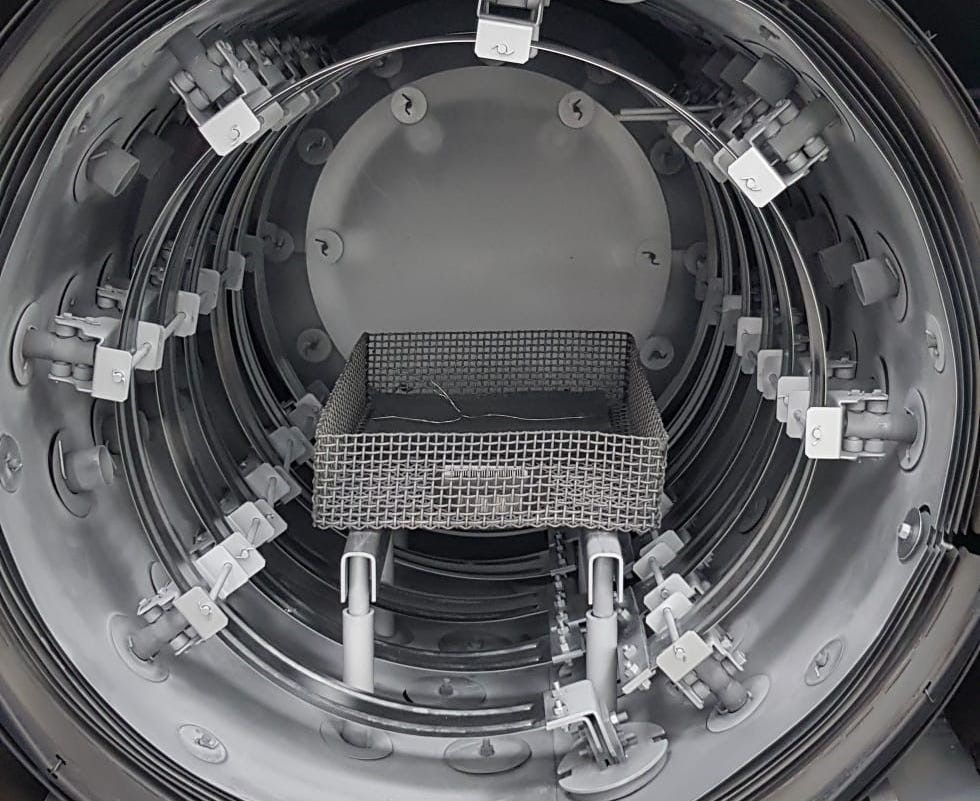
Ti 21S parts inside the furnace hot zone ready for heat treatment
Heat treatment of beta titanium alloys
Heat treatment of beta titanium alloys is performed in order to allow alpha phase precipitation in the beta matrix, strengthening the material. Controlling alpha size and distribution, it is possible to design various microstructures and correspondingly mechanical properties.
Typically, the heat treatment consists in a solution heat treatment above the beta-transus temperature, to promote recrystallization and recover isotropy, followed by aging.
Metastable beta alloys, unlike alpha-beta alloys, are able to retain the beta phase even upon air colling after solution heat treatment, making this class of materials particularly suitable for heat treatment on vacuum furnaces followed by gas (Argon) quenching.
Gas quenching makes it easier to control the cooling rate and minimizes distortions compared to water quenching, which is usually adopted for the solution heat treatment of Ti-6Al-4V and other alpha-beta alloys. This represents a major advantage for additively manufactured parts which are usually “near-net-shape” and require little to none post-process machining.
Nevertheless, the cooling rate is critical to control alpha grain boundary (αg.b.) precipitation and should be carefully considered.
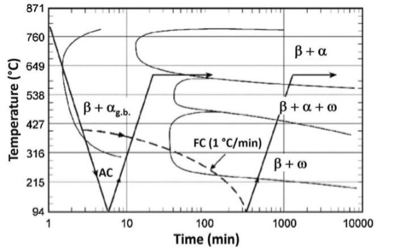
Time - Temperature representation of the solution and aging heat treatments of Ti 21S.
For the aging treatment instead, the selected temperature will modify significantly the material response: low temperature aging can increase the strength of the material at the expenses of ductility. Differently, aging at higher temperature leads to a recovering of the ductility on the expense of strength and improved thermal stability.
In that sense, two commercially diffused heat treatments for Ti21S are direct aging (AA) at around 590°C for 8h for low temperature applications and double aging (DA) at 690°C for 8h and 650°C for 8h for high temperature applications of Ti 21S.
We investigated the effect of the direct aging heat treatment on both the as-built and solution annealed material, as well as the effect of double aging on Ti 21S samples produced using a SISMA MySint 100 machine.
The samples were heat treated in our TAV VACUUM FURNACES R&D Laboratory, where we have different vacuum furnaces dedicated to R&D activities. Being titanium both an oxygen and a carbon sensitive material, for those heat treatments we opted for our TAV TPH 30-30-45 HP model equipped with an all-metal molybdenum hot zone, diffusion pump for high vacuum operation in the 10-5/10-6 mbar range and high pressure gas quenching.
We summarized the heat treatments tested in the following table.
Heat Treatment
|
Solution Annealing
|
Aging 1
|
Aging 2
|
AA
Direct Aging
|
-
|
590°C - 8h
1 bar Argon cooling to RT
|
-
|
STA
Solution Annealing + Aging
|
930°C – 30 min
6 bar Argon quenching to RT
|
590°C - 8h
1 bar Argon cooling to RT
|
-
|
DA
Double Aging
|
-
|
690°C - 8h
Furnace cooling to 650°C
|
650°C - 8h
1 bar Argon cooling to RT
|
Effect of the heat treatment strategy
After being heat treated, the samples were analyzed at University of Trento through microstructural characterization, tensile testing, fractographic analysis after tensile testing and residual stress evaluation on cantilever specimens.
The different heat treatment strategies proved to have a significant impact on the strength and fracture elongation of the samples, other being successful in completely removing the residual stresses due to the L-PBF process.
You can find the complete article “Heat treatment of a Beta-Ti21S alloy produced by additive manufacturing” with the full results in details on the last number of the “La metallurgia Italiana - International Journal of the Italian Association for Metallurgy", n.07/08 july-august 2023.
You can also directly access the article from this link. (https://www.aimnet.it/eng/rivista.php)
TAV VACUUM FURNACES want to thank for their precious collaboration all of the authors:
Lorena Emanuelli - INSTM (Operative center: University of Trento), Trento (TN), Italy
Vassili Tonon - University of Trento, Trento (TN),
Massimo Pellizzari - University of Trento, Trento (TN), Italy
Carlo Lora - SISMA SpA, Piovene Rocchette (VI), Italy