In the first part of the article we discussed about powders and the classifications adopted for cemented carbide, as well as the importance of using a proper dewaxing cycle.
In this second part we will go more in depth about the sintering process, discussing the difference between vacuum sintering and sinter-HIP for cemented carbide and the equipment.
Sintering
Vacuum furnaces can be designed to carry out both thermal dewaxing and sintering on the same piece of equipment. In that case, furnaces are equipped with a wax trapping system and a box with calibrated gas nozzles for an homogeneous gas flow distribution. The gas flow distribution is critical to efficiently remove wax vapors from the parts and ensure an optimal temperature uniformity.
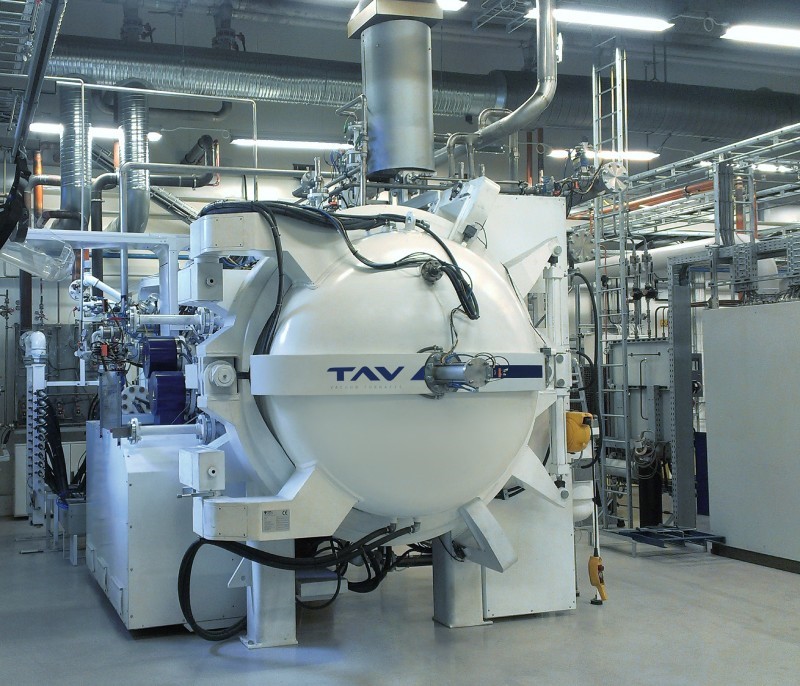
TAV VACUUM FURNACES HM Series - Sinter-HIP furnace equipped for hydrogen overpressure operation.
The electrically fired H2 burner is visible on top of the furnace.
However, separated dewaxing furnaces are sometimes used to improve productivity and cleanliness on the sintering furnace. In the that case, even if dewaxing is generally completed at temperatures below 500°C, parts are heated to higher temperatures approaching 1000°C as a pre-sintering step, to ensure sufficient strength on the parts to be moved to the sintering furnace.
After dewaxing, parts are ready to be sintered. Before going more in details, describing the features and peculiarities of vacuum furnaces for the sintering of cemented carbide, we must first understand the mechanisms driving the process.
Densification of cemented carbide is obtained through liquid phase sintering, i.e. the metal binder phase melts approaching the sintering temperature and the carbides are dissolved into the liquid phase. In fact, solid solution sintering is very limited for the WC-CO system and would require enormously long sintering time. For that reason, metal binders forming eutectic system at low temperatures are required (as a reminder, eutectic systems are mixture of different elements having lower melting point than those of the constituents). For example, between WC and Co eutectic occurs around 1320°C, even if high quantity of free carbon might induce the formation of Co-C eutectic at lower temperature. For that reason, WC-Co is usually sintered in the 1350-1500 °C range; higher temperatures are usually preferred for low cobalt contents, forming a lower fraction of liquid phase, and vice versa.
Once the sintering temperature is reached, capillary actions move the liquid binder towards porosity, causing shrinkage on the part and increase in its density.
Sintering can be carried out both in vacuum or aided by high pressure, combining sintering and hot isostatic pressing.
In the first case, graphite insulated vacuum furnaces are typically employed, having maximum temperature in the range 1500-1600°C. Those furnaces able to reach vacuum levels as deep as 0.001 mbar, even though partial pressures of gas (usually argon) are often adopted, around 1-10mbar, to prevent vaporization of volatiles elements and the liquid phase at high temperatures. The tightness of the vacuum furnace and the argon purity are critical parameters to obtain a sufficiently “dry” atmosphere (i.e. with sufficiently low oxygen partial pressure) to ensure that the oxides present on the powders, such as CoO, WO and Cr2O3, are reduced before reaching the sintering temperature. In fact, insufficient oxide reduction at low temperatures will produce entrapped gas porosities.
Hot isostatic pressing (HIP) is particularly beneficial to eliminate residual porosities and maximize the properties of cemented carbide, such as transverse rapture strength. HIP can both be applied to cemented carbide as a post-process operation (post-HIP in short) or simultaneously to the sintering step; in this case, the process is called sinter-HIP.
Post-HIP is usually performed with argon at high pressures of approximately 1000 bar at temperatures below the sintering temperature, around 1000°C to 1100°C.
Sinter-HIP, instead, is carried out through injection of argon up to 100bar at the sintering temperature, around 1450°C. Thanks to presence of a liquid phase at the sintering temperature, lower pressures are required to completely eliminate residual porosities compared to post-HIP.
Sinter-HIP is often preferred, not only for the practicality and economicity of combining two processes in one, but also to avoid excessive grain growth, which is sometimes associated with post-sintering HIP.
A typical sinter-HIP cycle for cemented carbide is represented in next figure; in that particular case, the cycle also includes an initial dewaxing step in hydrogen atmosphere.
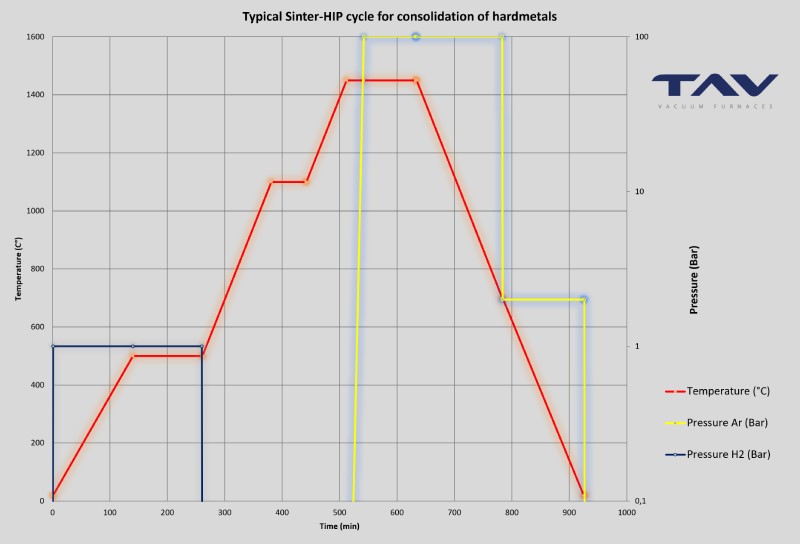
Typical sinter-HIP cycle for cemented carbide
Sinter-HIP is particularly beneficial for grades with lower cobalt content, especially for finer grains; that combination in fact, strongly inhibits the complete densification of the parts without application of isostatic pressure. In these cases, the difference in transverse rapture strength can be as high as 50% more in favor of sinter-HIPed parts compared to vacuum sintered parts.
Compared to traditional vacuum furnaces, sinter-HIP furnaces require specific design features.
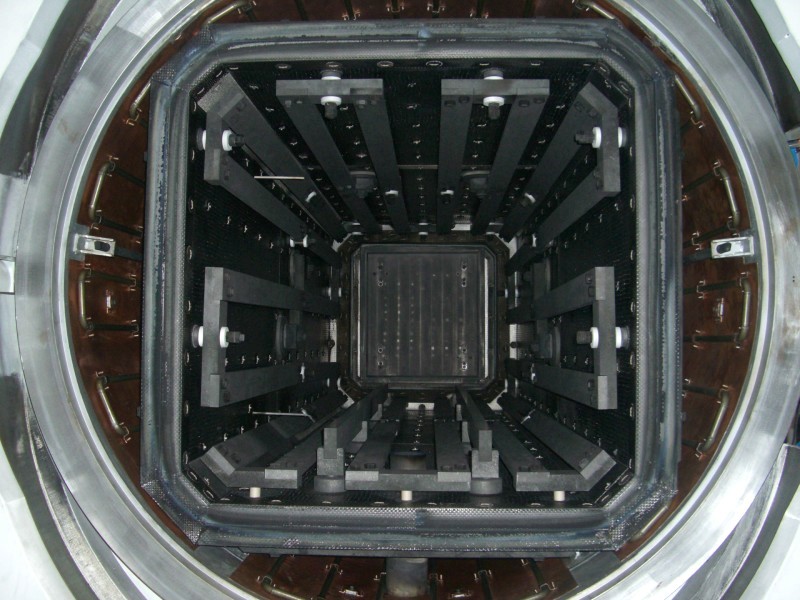
Hot zone of a TAV VACUUM FURNACES HM Series - Sinter-HIP Furnace
Other than mechanical stresses due to the differential pressure between inside and ambient pressure outside the furnace, operating at relatively high temperatures with high pressure of gas would lead to significant dissipations of heat to the external environment. This is not only anti-economic from an efficiency point of view, but could also compromise the structural integrity of the water-cooled steel vessel of the furnace by overheating it. For that reason, TAV VACUUM FURNACES HM Series sinter-HIP furnaces are equipped with our specially designed ICT (Internal Cooling Technology) to control the vessel temperature during the cycle.
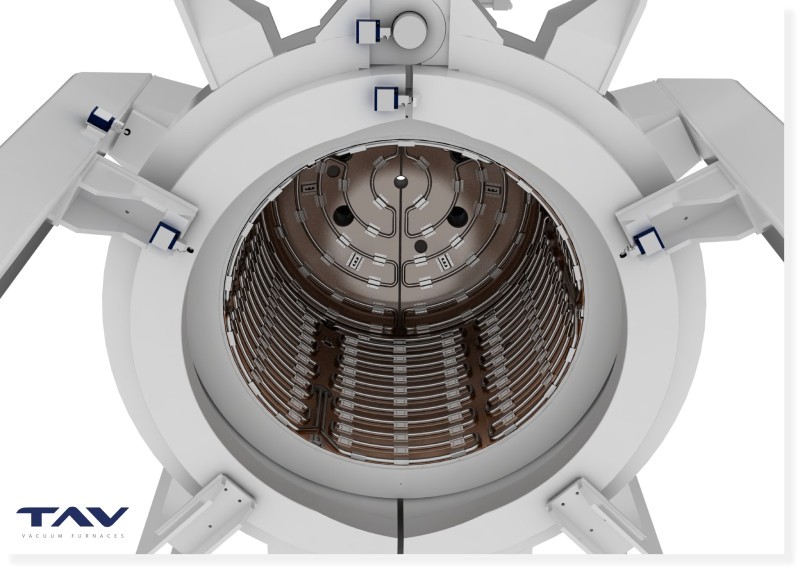
TAV VACUUM FURNACES ICT (Internal Cooling Technology)
In conclusion
As we learned in the article, for various categories and grades of cemented carbide available on the market for several applications, different production processes might be applied. Consolidation is a critical step in the production process and will ultimately determine the performance of the hard metal tool; all the stages, from dewaxing to sintering, must be carefully selected according to the material characteristics.
Vacuum furnaces are versatile machines and can be configured to operate in different conditions during different stages of the process. There are, however, design features that should be kept into consideration during the engineering of the furnace, based on the requirements; for that reason, relying on experts is the only way to be sure you could always get the most out of your cemented carbide parts.