This article is available in English too.
Nella prima parte dell'articolo abbiamo parlato delle polveri e delle classificazioni adottate per il carburo cementato, nonché dell'importanza di utilizzare un corretto ciclo di deceratura.
In questa seconda parte approfondiremo il processo di sinterizzazione, discutendo la differenza tra sinterizzazione in vuoto e “sinter-HIP” per il carburo cementato e le relative attrezzature impiegate.
Sinterizzazione
I forni in vuoto possono essere progettati per eseguire sia la deceratura termica che la sinterizzazione nello stesso impianto. In questo caso, i forni sono dotati di un sistema di intrappolamento della cera e di un box con ugelli calibrati per una distribuzione omogenea del flusso di gas. La distribuzione del flusso di gas è fondamentale per rimuovere efficacemente i vapori di cera dai pezzi e garantire un'uniformità di temperatura ottimale.
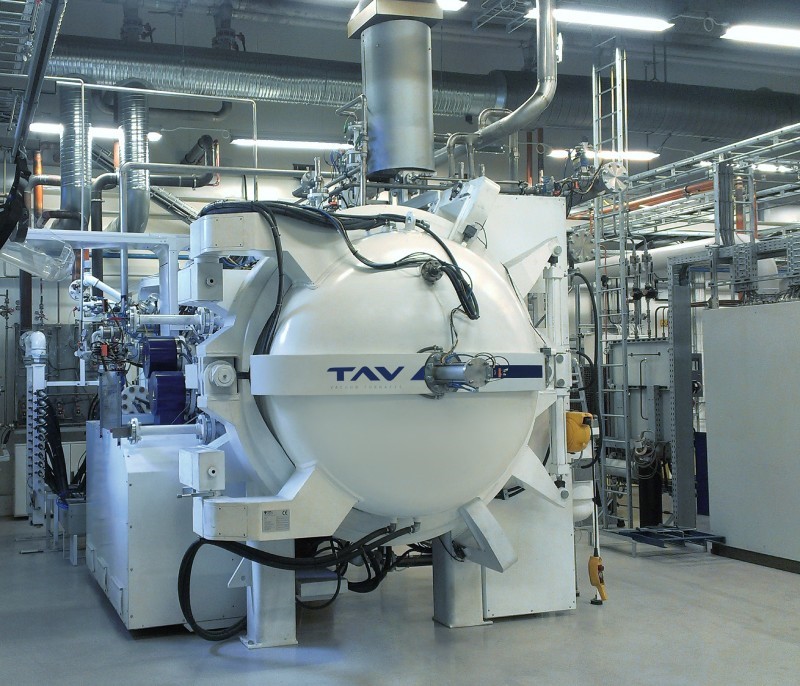
TAV VACUUM FURNACES HM Series - Sinter-HIP, equipaggiato per operare in sovrapressione di idrogeno.
È possibile notare il bruciatore elettrico per l’idrogeno in cima al forno.
Tuttavia, a volte si utilizzano forni da deceratura separati per migliorare la produttività e la pulizia del forno da sinterizzazione. In questo caso, anche se la deceratura viene generalmente completata a temperature inferiori a 500°C, i pezzi vengono riscaldati a temperature più elevate, prossime ai 1000°C, come fase di pre-sinterizzazione, per garantire una resistenza meccanica sufficiente tale da trasferire i pezzi al forno di sinterizzazione.
Dopo la deceratura, i pezzi sono pronti per essere sinterizzati. Prima di entrare nel dettaglio, descrivendo le caratteristiche e le peculiarità dei forni in vuoto per la sinterizzazione del carburo cementato, dobbiamo innanzitutto comprendere i meccanismi che guidano il processo.
La densificazione del carburo cementato si ottiene attraverso la sinterizzazione in fase liquida, cioè la fase legante del metallo si scioglie avvicinandosi alla temperatura di sinterizzazione e i carburi si dissolvono nella fase liquida. Infatti, la sinterizzazione in soluzione solida è molto limitata per il sistema WC-CO e richiederebbe tempi di sinterizzazione enormemente lunghi. Per questo motivo, sono necessari leganti metallici che formino un sistema eutettico a basse temperature (come ripasso, ricordiamo che i sistemi eutettici sono miscele di elementi diversi con un punto di fusione inferiore a quello dei costituenti). Ad esempio, tra WC e Co l'eutettico si verifica intorno ai 1320°C, anche se un'elevata quantità di carbonio libero potrebbe indurre la formazione dell'eutettico Co-C a temperature inferiori. Per questo motivo, il WC-Co viene solitamente sinterizzato nell'intervallo 1350-1500 °C; temperature più elevate sono solitamente preferite per bassi contenuti di cobalto, che formano una frazione inferiore di fase liquida, e viceversa.
Una volta raggiunta la temperatura di sinterizzazione, l’azione capillare sposta il legante liquido verso le porosità, causando un ritiro del pezzo e un aumento della sua densità.
La sinterizzazione può essere effettuata sia in vuoto che con l'ausilio di alta pressione, combinando sinterizzazione e pressatura isostatica a caldo.
Nel primo caso, si utilizzano tipicamente forni sottovuoto isolati in grafite, con temperature massime comprese nell'intervallo 1500-1600°C. Questi forni sono in grado di raggiungere livelli di vuoto fino a 0,001 mbar, anche se spesso vengono adottate pressioni parziali di gas (solitamente argon) intorno a 1-10mbar, per evitare la vaporizzazione degli elementi volatili e della fase liquida alle alte temperature. La perfetta ermeticità del forno in vuoto e la purezza dell'argon sono parametri critici per ottenere un'atmosfera sufficientemente "secca" (cioè con una pressione parziale di ossigeno sufficientemente bassa) per garantire che gli ossidi presenti sulle polveri, come CoO, WO e Cr2O3, vengano ridotti prima di raggiungere la temperatura di sinterizzazione. Infatti, una riduzione insufficiente degli ossidi a basse temperature produrrebbe porosità dovute all’evolvere di gas intrappolato nel materiale.
La pressatura isostatica a caldo (“hot isostatic pressing” o “HIP”) è particolarmente vantaggiosa per eliminare le porosità residue e massimizzare le proprietà del carburo cementato, come la resistenza a rottura trasversale. Il processo HIP può essere applicato al carburo cementato sia come operazione successiva alla sinterizzazione (in breve “post-HIP”) o contemporaneamente alla fase di sinterizzazione; in questo caso, il processo è chiamato “sinter-HIP”.
Il “post-HIP” viene solitamente eseguito con argon ad alta pressione, circa 1000 bar, a temperature inferiori alla temperatura di sinterizzazione, da 1000°C a 1100°C circa.
Il “sinter-HIP”, invece, viene effettuato mediante iniezione di argon fino a 100 bar alla temperatura di sinterizzazione, circa 1450°C. Grazie alla presenza di una fase liquida alla temperatura di sinterizzazione, sono necessarie pressioni inferiori per eliminare completamente le porosità residue rispetto al “post-HIP”. Il “sinter-HIP” è spesso preferito, non solo per praticità e per l'economicità di combinare due processi in uno, ma anche per evitare l'eccessiva crescita dei grani, talvolta associata all’ “hot isostatic pressing” post-sinterizzazione.
Un tipico ciclo di “sinter-HIP” per il carburo cementato è rappresentato nella figura di seguito; in questo caso particolare, il ciclo comprende anche una fase iniziale di deceratura in atmosfera di idrogeno.
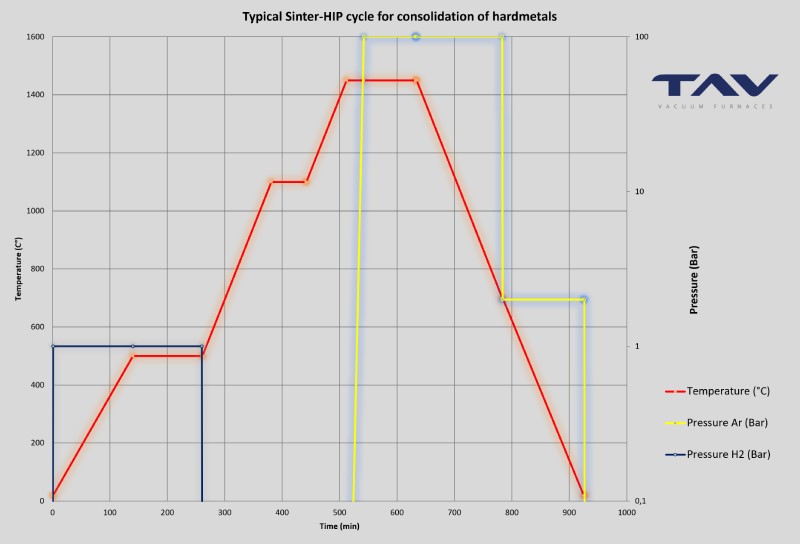
Esempio di ciclo “sinter-HIP” per il carburo cementato
Il “sinter-HIP” è particolarmente vantaggioso per i gradi contenenti una percentuale bassa di cobalto, soprattutto per i grani più fini; questa combinazione, infatti, inibisce fortemente la completa densificazione dei pezzi senza l'applicazione di pressione isostatica. In questi casi, la differenza nella resistenza a rottura trasversale può arrivare ad essere anche del 50% superiore per i pezzi sinterizzati con “sinter-HIP” rispetto a quelli sinterizzati sotto vuoto.
Rispetto ai forni in vuoto tradizionali, i forni per “sinter-HIP” richiedono caratteristiche di progettazione specifiche.
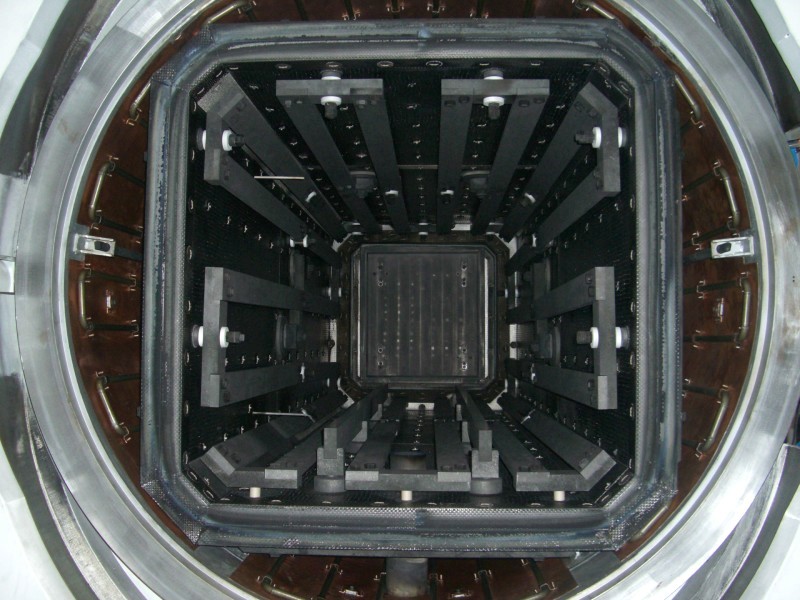
Camera termica di un forno per sinter-HIP TAV VACUUM FURNACES HM Series
Oltre alle sollecitazioni meccaniche dovute alla pressione differenziale tra l'interno e la pressione ambiente all'esterno del forno, il funzionamento a temperature relativamente elevate con un'alta pressione di gas porterebbe a una significativa dissipazione di calore verso l'ambiente esterno. Questo non solo è antieconomico dal punto di vista dell'efficienza, ma potrebbe anche compromettere l'integrità strutturale della campana in acciaio raffreddata ad acqua del forno, surriscaldandola eccessivamente. Per questo motivo, i forni TAV VACUUM FURNACES della serie HM sono dotati della tecnologia ICT (Internal Cooling Technology), appositamente progettata per controllare la temperatura della campana durante tutte le fasi del ciclo.
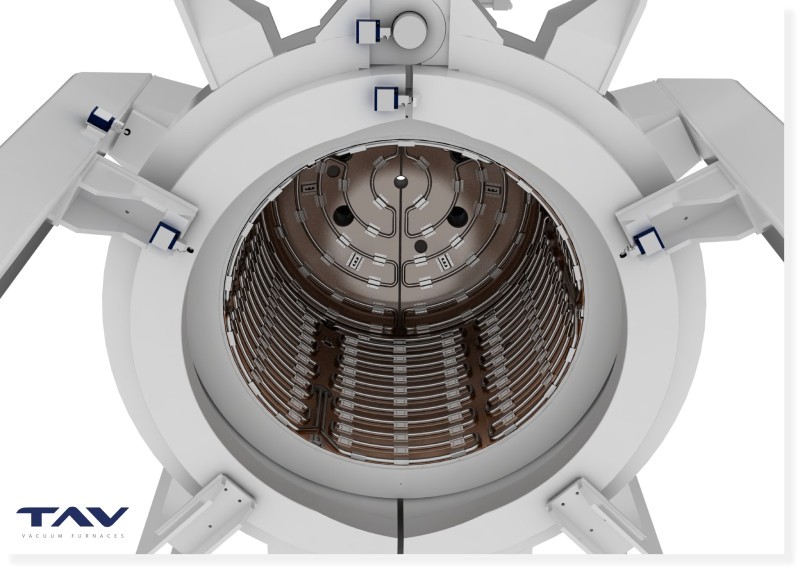
TAV VACUUM FURNACES ICT (Internal Cooling Technology)
In conclusione
Come abbiamo appreso nell'articolo, per le varie categorie e gradi di carburo cementato disponibili sul mercato per diverse applicazioni, possono essere applicati processi produttivi diversi. Il consolidamento è una fase critica del processo produttivo e determinerà in ultima analisi le prestazioni dell'utensile in metallo duro; tutte le fasi, dalla deceratura alla sinterizzazione, devono essere attentamente selezionate in base alle caratteristiche del materiale.
I forni in vuoto sono macchine versatili e possono essere configurati per operare in condizioni diverse durante le varie fasi del processo. Esistono tuttavia specifiche progettuali che devono essere tenute in considerazione durante l'ingegnerizzazione del forno, in base alle esigenze; per questo motivo, affidarsi a esperti è l'unico modo per essere sicuri di ottenere sempre il massimo dai propri componenti in carburo cementato.