Sono passati già parecchi anni da quando le EN ISO 13849-1 e IEC 62061 hanno sostituito la ormai obsoleta EN 954-1 come normative tecniche riguardanti la sicurezza dei sistemi di controllo. Ma queste normative sono state veramente recepite da tutti i settori industriali, tra cui quello dei forni a vuoto?
Allo stesso tempo, i PLC di sicurezza (Controllori a Logica Programmabile) stanno sostituendo con sempre maggiore frequenza i relè di sicurezza tradizionali in molte applicazioni chiave. Ma sono davvero utili? Per quale ragione dovrebbe essere necessario installare un PLC di sicurezza su un forno a vuoto? Questo tema si presta certamente a molte perplessità, per questo vorrei fornirvi 5 validi motivi per cui dovreste installare un PLC di sicurezza sul vostro prossimo forno da vuoto.
1. L’arresto di emergenza non è l'unica funzione di sicurezza
Se si apre il quadro elettrico di un forno a vuoto di qualche anno fa, vi accorgerete che l'arresto di emergenza è probabilmente l’unica funzione che corrisponde agli standard delle normative EN ISO 13849-1 e IEC 62061.
Mentre questo potrebbe essere sufficiente per un macchinario semplice il cui unico rischio potrebbe essere determinato da una parte mobile che deve essere bloccata mediante l’apertura di una protezione o premendo il pulsante di arresto di emergenza, questo non è il caso di un forno a vuoto con raffreddamento in gas pressurizzato, dove la temperatura e la pressione hanno importanti implicazioni sulla sicurezza.
Fino a poco tempo fa, alcune sicurezze cablate venivano aggiunte esternamente al controllore funzionale ed erano consuete, anche se non corrispondevano completamente agli standard di sicurezza. Tuttavia, queste sicurezze cablate non sono in grado di soddisfare gli standard più recenti per diversi motivi, quali la scarsa copertura diagnostica (ad esempio in caso di corto circuito) o ridondanza limitata (poiché il controllore funzionale non può essere considerato nella valutazione della funzione di sicurezza).
Quindi, che cosa offre in più un PLC di sicurezza rispetto ai moduli di sicurezza tradizionali?
2. I PLC di sicurezza possono elaborare i segnali analogici
Temperatura e pressione sono essenzialmente entità analogiche. Mentre i nuovi PLC di sicurezza possono essere dotati di schede di ingresso per leggere ed elaborare una grande varietà di segnali analogici (come quelli provenienti da TC, Pt100 o molti altri trasduttori), i relè di sicurezza possono essenzialmente elaborare solo informazioni digitali (come un pulsante o un finecorsa).
Qual è, quindi, il vantaggio rispetto all'utilizzo di interruttori di pressione e temperatura per fornire segnali digitali ai relè di sicurezza?
3. I segnali analogici offrono miglior copertura diagnostica
Una pratica di base nella sicurezza è quella di utilizzare la ridondanza per aumentare il livello di sicurezza, ad esempio, utilizzando due interruttori di temperatura invece di uno solo. Tuttavia, se non si controllano entrambi gli interruttori, prima o poi il primo interruttore potrebbe incepparsi senza dare segnali, e poi potrebbe farlo anche il secondo vanificando la loro funzione di sicurezza. Ma se il punto di commutazione è impostato ad una temperatura che non dovrebbe mai essere raggiunta in circostanze normali, com’è possibile verificare il funzionamento dei due sensori anche se non stanno funzionando affatto?
Se vi hanno detto che è sufficiente rimuovere periodicamente il termostato e calibrarlo, hanno perfettamente ragione! Tuttavia, sarei curioso di vedere nel registro di manutenzione quando è stata eseguita quest’operazione l'ultima volta sugli interruttori di sovratemperatura installati sui vessel dei loro forni.
Anche se è stato effettivamente oltrepassato il punto di commutazione (durante il normale funzionamento o in una procedura diagnostica), come si può dire che i due interruttori stanno funzionando correttamente? Per i finecorsa, questo viene solitamente controllato utilizzando una finestra temporale, ma questo non può essere applicato in modo sicuro per gli interruttori di pressione o temperatura, dato che questi interruttori non sono suscettibili di commutare esattamente allo stesso tempo, e il ritardo è dovuto alla differenza del punto di commutazione del tasso di variazione della misura, che è generalmente sconosciuto.
Questo è il punto dove la possibilità di elaborare in modo sicuro i valori analogici entra in gioco: se si dispone di due misure di temperatura, è possibile metterle a confronto, anche quando non si è in prossimità del punto di commutazione. Se si rompe un sensore, lo si capisce immediatamente non appena le due letture differiscono più di una certa tolleranza.
Se il punto di commutazione è oltrepassato durante il normale funzionamento, anche la combinazione di un segnale analogico con un segnale digitale può essere una possibilità interessante, dato che manifesterebbe una diversità e aiuterebbe a prevenire i guasti più comuni.
Ma un PLC di sicurezza fornisce altri vantaggi oltre a questo? Certamente! Andiamo ora ad analizzare altre 2 ragioni per cui un PLC di sicurezza potrebbe essere una valida scelta per minimizzare i rischi sul tuo forno.
Ti è piaciuto fino a qua l'articolo?
Prima di continuare nella lettura, seguici sulla nostra pagina Twitter cliccando il pulsante qui sotto!
In tal modo rimarrai aggiornato sulle tecnologie più avanzate per i trattamenti termici non solo con i nostri articoli, ma anche con le migliori pubblicazioni che raccogliamo in giro per la rete.
4. I PLC di sicurezza portano a bordo logiche più complesse
Ci sono applicazioni in cui le funzioni di sicurezza non sono semplicemente basate sullo stato di uno o più sensori, ma anche su una specifica sequenza di operazioni. Per esempio, in un forno che utilizza l’idrogeno come atmosfera di processo, è necessario sapere con certezza che uno spurgo di gas inerte è stato completato in modo sicuro prima di immettere o sfiatare altro idrogeno.
Questa è stata l’applicazione in cui i PLC di sicurezza si sono diffusi più rapidamente, tanto da essere già installati sui forni a idrogeno di quasi tutti i principali produttori. Ma questo non è tutto...
5. I PLC di sicurezza riducono i rischi di manomissione
Immagino che sia capitato anche a voi la classica situazione con il forno bloccato a causa di un sensore guasto o che aveva bisogno di calibrazione, proprio quando il vostro cliente aveva bisogno di una consegna urgente e per risolvere questo problema i vostri tecnici hanno bypassato i sistemi di sicurezza. Questo comportamento è potenzialmente molto pericoloso perché se il tecnico poi non si ricorda di riattivare correttamente il sistema di sicurezza potrebbero sorgere gravi problematiche.
Come produttori, abbiamo la responsabilità non solo di utilizzare componenti affidabili e sicuri, ma anche prevenire la possibilità di manomissioni al sistema di sicurezza. Il PLC di sicurezza ci può aiutare in tutto questo?
Certamente! Prima di tutto, in un PLC, tutta la logica di sicurezza è incorporata all'interno del controllore stesso. Mentre una logica di sicurezza cablata può essere alterata da chiunque abbia un cacciavite, per modificare la logica in un PLC di sicurezza è necessario non solo un software specifico, ma anche una password impostata dal costruttore per ogni singolo forno.
Il livello di sicurezza può essere ulteriormente incrementato combinando controllore di sicurezza con sensori intelligenti, che applicano una differita al segnale proveniente dal PLC o che generano l’azionamento stesso. In questo modo, un sensore di sicurezza intelligente non può essere bypassato con un corto circuito, a differenza dei sensori tradizionali che si basano semplicemente su contatti puliti.
Si potrebbe comunque obiettare che sia possibile forzare un contattore con un cacciavite, e sfortunatamente è vero. Non importa quanto sofisticato possa essere, c'è ancora qualcosa che un PLC di sicurezza non può fare!
Allora, avete già installato un PLC di sicurezza sul vostro forno a vuoto?
Ti è piaciuto l'articolo?
Iscriviti al nostro canale Telegram, in tal modo potrai restare aggiornato sulle tecnologie più avanzate per i trattamenti termici.
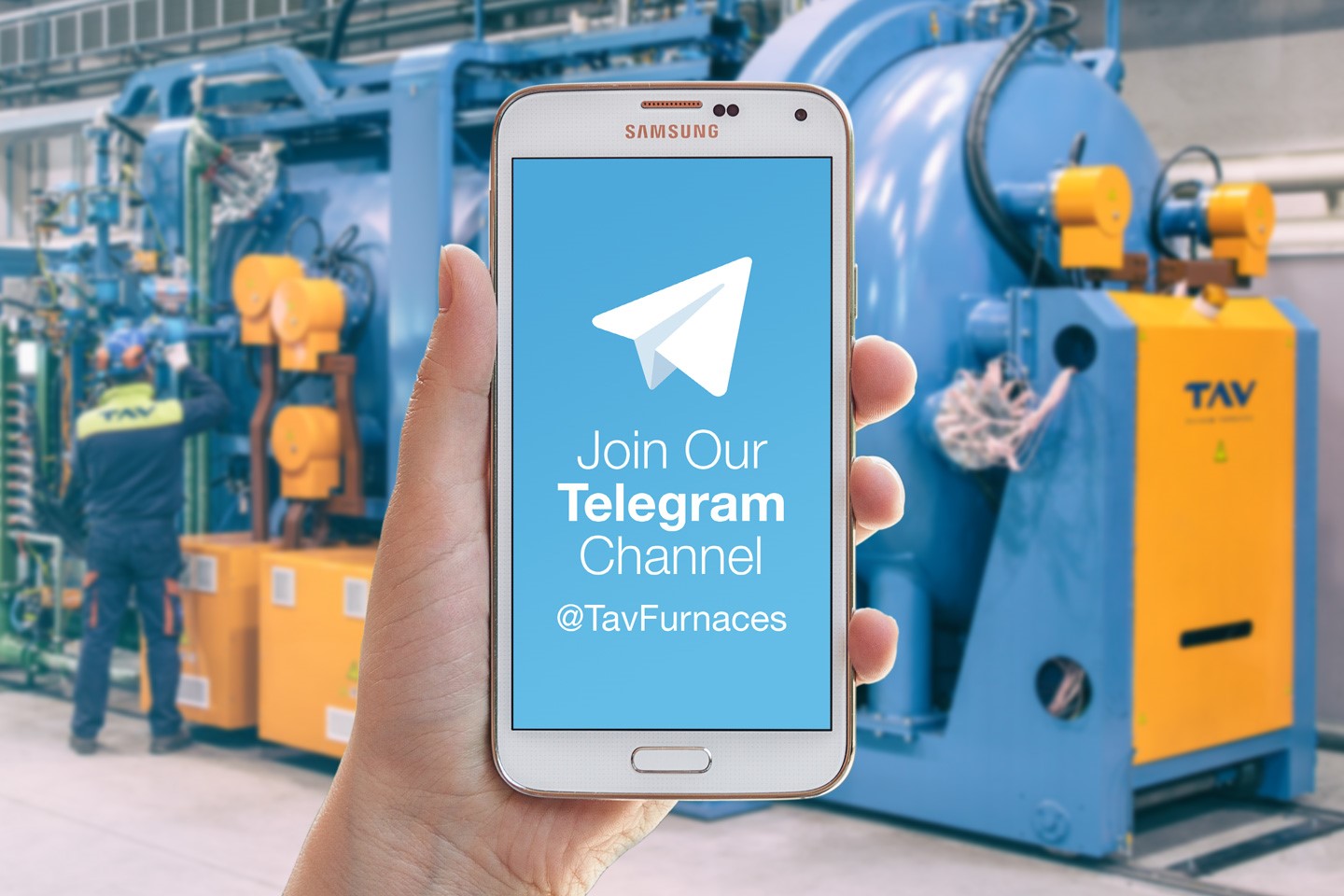
Non hai Telegram?
Se ancora non hai Telegram, usa uno dei seguenti pulsanti per installarlo:
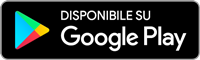
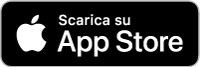