Manufacturers who are looking for a solution to make small metal components and
complex shapes have had only two options to date:
- casting
- metal injection molding (MIM)
While casting, which has been used since the dawn of time, remains
competitive only for pieces of considerable size or for which a lack of precision
is required, MIM (Metal Injection Molding) has
existed for about 4 decades and is a mature and advantageous technology. It is in
fact used for the large scale production of small and complex components with high
precision and that not require subsequent processing.
What's the downside?
Unfortunately MIM has a high cost, mainly due to the molds.
Companies are therefore increasingly encouraging the development of a cheaper and
more versatile alternative: 3D metal printing and in this case
3D Binder Jetting.
If you are wondering what technology to use, all you have to do is to read this
article: I will give you an exhaustive introduction to the two technologies and
at the end we will compare them by highlighting their pros and cons.
Let's start from the first one.
Metal Injection Molding (MIM)
Metal Injection Molding (MIM) is a metallurgical process for the production of
materials with complex shapes, starting from a raw material in the form of
metallic powder compacted in pellets.
It was born in the 1920s for the sole use of ceramic powders,
but it is in the 1970s that it was established as one of the most versatile technologies
in terms of manufacturing products with high geometric complexity and usable materials
(ceramic powders, metal powders and polymers).
Finally, in the last few years, the technology has further improved with the consequent
reduction of production costs and this has allowed a further improvement of the
obtained product.
The MIM process is normally divided into 3 main steps:
- Printing
- Debinding
- Sintering
Let's look now at them in more detail and furthermore I will show you two factors,
respectively in the debinding phase and in the sintering one, to be taken into consideration
to get the best results. Do not miss them!
Printing
Before molding, it is necessary to prepare the raw material which will be melted,
molded, solidified and thickened. For this reason the metal/ceramic powder is mixed
with very precise proportions of organic binder, obtaining a homogeneous
solid solution (also called feedstock).
The organic component is one of the main protagonists of the whole process and
must meet the following requirements:
- It has to incorporate a high percentage of metal/ceramic powder, about 60%
of the whole volume.
- It has to form a homogeneous mass that can be laminated and shaped at high
temperatures.
- It has to be removed without causing significant distortion to the object
while acting as a removable structural component.
- It has to be a compound that does not cause damage to the health and the
environment.
- It has not to be expensive.
- It has to be recycled through distillation cycles.
The binder/metal powder volume ratios vary according to the type and quantity
used of the two components.
In this specific case, the percentage of metal powder volume varies between 55 and
65% (binder 45-35%).
The organic thermoplastic binder is mixed dry and then hot (at the melting
temperature of the polymer) together with the metal powder. This phase is essential
in order to maximize the homogeneity of the same mixture. The increase in temperature
during mixing is important to obtain the lowest possible viscosity level
and to facilitate the hot molding phase.
At the end of the process, the mixture is again cooled and granulated until the
actual pellets are obtained.
The feedstock is inserted into a hopper and subsequently pressurized
by means of a screw pushed by an hydraulic cylinder and heated by means of the resistances
inserted at the injection nozzle.
The molten and pressed mixture is then injected into a steel mold.
The mold must have anti-abrasive characteristics since the melted material is highly
abrasive during the deposit phase.
The produced and cooled object is named Green and still contains all
the solid phase binder.
The low maneuverability of the green depends on the fact that, in this
phase, the mechanical properties are conferred to the piece only by the polymeric
compound. Consider that the green has the shape and proportions of the
final product but with a volume greater than 15-20% due to the presence of the binder.
Read the next lines carefully now, because the choice of binder is of
paramount importance in order to optimize the printing and debinding process.
A low-melting binder speeds up the debinding process but at the same time causes
a phase separation between the binder and the metal powder.
Segregation can be caused by two distinct factors:
- Distribution gradients: they can block some of the extruded
material in the injector, decreasing the injection pressure which leads to an
inadequate form filling.
- Differential centrifugal forces: in this case segregation
arises from the injection process. The injection phase transmits different centrifugal
forces to the binder and metals, thus separating the heavier and lighter particles.
This phenomenon necessarily leads to the formation of an inhomogeneous green.
Otherwise, when using a binder with a higher melting point and molecular weight,
there is a benefit in terms of viscosity at the expense of the speed of the debinding
phase.
It must also be considered that the increase in viscosity can cause oil drains (contained
in the binder to facilitate the preparation phase) that would change the shape of
the component permanently, causing irreversible cracks in the sintering
phase.
From what we have said so far, it follows that it is important to carefully choose
a binder formulation that can be efficient both in printing and debinding.
Let's now look at the most delicate and critical phase of the whole process.
Debinding
A correctly performed debinding is essential for the success of the following
steps.
The purpose of this phase is to remove most of the binder present in the solid phase.
The debinding phase must take place in order to avoid deformation, crumbling, swelling
or breakage of the printed object.
There are two types of debinding:
- Solvent debinding
- Thermal debinding
In the case of solvent debinding, the binder must be able to
dissolve in a low temperature solvent. Acetone and heptane are typically solvents
used for the debinding of hydrophobic binders, although the use of water as a solvent
is preferred, since hydrophilic binders do not chemically attack the structure of
the compound.
Solvent debinding generally removes only a part of the binder, in fact, after
this phase thermal debinding is performed.
Thermal debinding consists in evaporating the binder by thermal
means.
This type of debinding is generally applied with a vacuum furnace,
slowly raising the temperature in order to avoid swelling and deformation of the
green.
At the end of the debinding, the object loses weight and volume, forming a solid
metallic structure, called in jargon Brown.
Sintering
Here we are at the final stage of the process, which aims to:
- compacting the structure, thickening up to 95% of the final theoretical
density;
- eliminate the residual binder (10% maximum residual binder).
At the end, you obtain the product with the definitive mechanical and geometrical
characteristics.
Usually sintering is conducted in vacuum furnace, increasing
the temperature up to 2/3 of the melting temperature of the metal compound. In this
way a complete coalescence of the individual powder grains is obtained with consequent
densification of the final component. In some cases the sintering phase can be facilitated
by making it precede by a phase of pre-sintering.
The alloys typically used for making MIM pieces are:
- cementation steels;
- tempered steel;
- bearing steel;
- stainless steel
- tool steel;
- Fe-silicon alloys for magnetic applications.
Did you like this article up to here?
Before you continue, follow us on our Facebook page pressing the button here below!
In this way, we'll be able to keep you updated on most advanced technologies for heat treatments not only with our posts, but also with the best articles that we collect around the web.
Binder Jetting
Let's now look at the latest technology, the alternative to MIM that in recent
years is often under the spotlight: binder jetting or 3d metal
printing. Note that the term 3D printing in the common language
it is often mistakenly used as a synonym for additive manufacturing,
instead three-dimensional printing it is only one of the possible additive
manufacturing technologies.
How does binder jetting work?
In short, a liquid binder is selectively deposited on a layer of metal powder and,
layer by layer, the final object is formed.
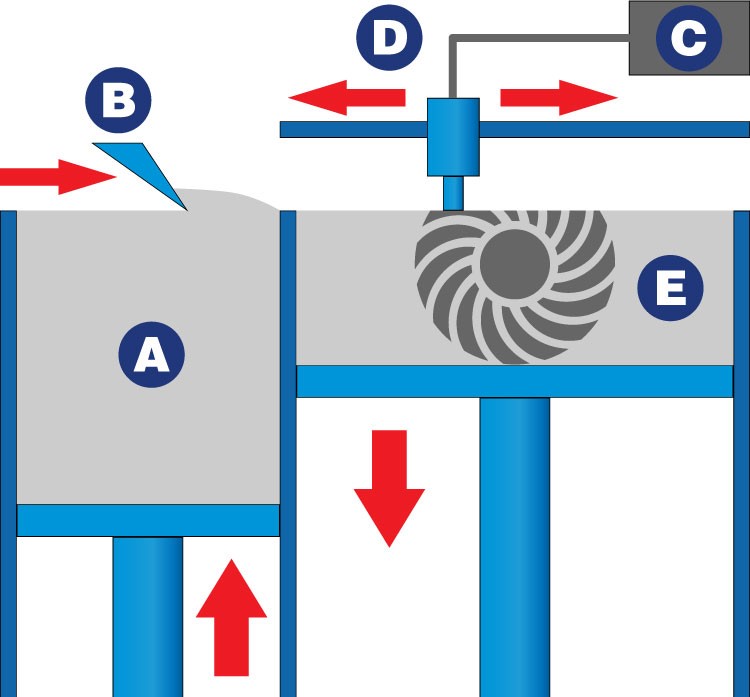
A: metal powder stock; B: squeegee; C: binder; D: print head; E: powder bed
Entering a little more in detail, the component to be realized is designed using
a CAD software (Computer-Aided Design) and the resulting file is
sent to a 3D printer that will produce the object by dividing it into layers.
The printing process takes place as described below:
- A squeegee (a kind of metal blade) spreads a layer of powder on the base
that will be used for the construction of the piece.
- A print head selectively deposits the glue material on the metal powder.
The average size of each drop is about 80 μm in diameter, so you can get
a good resolution.
- Once the process of deposition of the adhesive on the first layer is complete,
the base goes down to proceed with the next layer.
- The process is repeated from step (1) until all layers are printed.
At the end, the powder excess is cleaned from the object and the metal powder
can be recycled.
Once the printing phase is over, the manufactured object is in a state of
green with poor mechanical properties and high porosity. For this reason, post-processing
treatments are necessary, which are typically two:
- infiltration and/or
- debinding and sintering.
In the case of infiltration it is necessary to insert in the reticular cavities
compounds like: molten wax, cyanoacrylate adhesive, epoxy resin, etc.
In the case of debinding followed by sintering, they are applied in a vacuum
in order to obtain the binder removal and a subsequent coalescence of the grains
of the metallic powder.
In both cases the purpose of these treatments is to densify the molded component
to increase its mechanical properties.
As a result of these treatments, the volume of the sample is reduced a lot, due
to the high percentages of the pretreatment binder, but above all in an unpredictable
way.
The type of binder is strongly correlated to the used powder: for example the
use of a furan binder is ideal for silica bed prints that do not require post-print
thermal treatment. Phenolic binders, on the other hand, are excellent as binders
for sand cores. Finally, for metal powders, mainly water-based binders that thicken
the layers are used.
The materials used for binder jetting are:
- Silica sand: deriving from quartz crystals, does not require
heat treatments;
- Stainless steel: which can also be infiltrated with bronze.
The product has excellent mechanical properties and can be annealed;
- Cobalt-chrome-aluminum alloys: with excellent mechanical
properties at high temperature
Conclusions
We have analyzed the characteristics of MIM and binder jetting, describing
the production processes and highlighting the pros and cons of each one.
Is one technology designed to replace the other?
Or will both co-exist, each in specific areas and for specific purposes?
This will be the topic that we will discuss in the second part of the article... do not miss it!
Did you find this article useful?
If you think your friends will like it too, share it on Facebook.
You have only to press the button here below!