We are fresh off our stimulating attendance of the
43rd International Conference and Exposition on Advanced Ceramics and Composites,
or ICACC19. Over five exciting days, we took in many exciting talks
and showcases by research and industry leaders. We also did our part in demoing
and testing cutting-edge ceramic products, and we cannot wait to share the scoop
with you.
In the following blog post, we will:
- introduce you to the fascinating world of ceramic science;
- explain exactly what makes advanced ceramics such as
translucent alumina and transparent alumina
a potential game-changer;
- prove that vacuum furnaces and
vacuum sintering are essential
to manufacturing high-quality ceramic product.
We begin our trip into the realm of advanced ceramics with a quick rundown on
its calling-card event, the ICACC.
ICACC19: research and industry meet to drive ceramics innovation
Innovation is the chief source of added value and progress in our societies today,
and it largely depends on monetary and brain capital from universities and industry
leaders. It is all too often, however, that the two branches of innovation do not
get to speak to one another and, thus, miss out on mutually beneficial synergies
and knowledge transfer.
This is where the ICACC19 comes in.
It creates a space for scientists, research and development specialists, engineers,
and industry representatives to come together and take a deep dive into the latest
advances in ceramics research.
The 43rd edition of ICACC focussed on advanced ceramics,
bioceramics, and ceramic coatings, among many
other thrilling developments in the field. In the framework of seventeen symposia,
five focussed sessions, and a special forum for young investigators, ICACC19 was
an exciting event on a topic of continued importance.
But what exactly are advanced ceramics and why should you care?
Continue reading and prepare to have your professional and knowledge horizons expanded!
Did you like this article up to here?
Before you continue, follow us on our Facebook page pressing the button here below!
In this way, we'll be able to keep you updated on most advanced technologies for heat treatments not only with our posts, but also with the best articles that we collect around the web.
Advanced ceramics: strong, versatile, affordable
Much of recent developments in ceramics research focus on translucent
alumina, or see-through ceramic composites. They have a range of favourable
mechanical properties, including:
- exceptional hardness
- resistance to heat and corrosion
- various degrees of transparency
- high added value in a range of applications
Thus, transparent ceramics find applications in almost any environment where
highly resistant and reliable transparent media are required. From
advanced airborne optics to strong yet practically invisible orthodontic
brackets, translucent alumina are part of our daily lives already.
The possibility to form complex and intricate shapes is what makes translucent
alumina so desirable. Achieving equally great shape precision and transparency at
both small and large dimensions used to be quite expensive (think: single
crystal growth).
Thanks to recent developments in ceramic science, the costly fabrication procedures
are a thing of the past, and we can produce a wide range of robust transparent ceramic
items. But how do we achieve translucency in a material that is usually opaque?
It's all about reducing structural defects.
Translucent alumina and the fight against imperfection
When you think of ceramic objects, 'transparent' is usually not a quality that
comes to your mind. This is because conventionally sintered (compression-baked)
ceramics contain constellations of minor structural defects. While these
imperfections do not significantly compromise the ceramic objects' integrity, they
do make them opaque.
Achieving ceramic translucence, therefore, entails a battle against structural
heterogeneities. While a perfect structure is hardly attainable, keeping problematic
spots small and dispersed is key.
- For applications in the visible spectrum, ceramic heterogeneities cannot exceed
50 nm. In the ideal case, they will stay below 10 nm.
- For applications in the infrared spectrum, on the other hand, the tolerance
for heterogeneity is much higher and can extend to 1µm.
It follows, then, that transparent ceramics, much like people, are not perfect,
but the truly good ones have flaws that are small and far between. How much you
put up with depends on what your goals are. Unlike with people, however,
you are in full control of how much imperfection you will allow and how
clearly you will be able to see through the final product.
Transparent alumina are all about the sinter
The translucency of advanced ceramic composites can only be
achieved through a carefully controlled sintering process that keeps in mind two
important material properties:
- The size and concentration of the pores
- The fineness of the grain
Since translucent alumina is an anisotropic material, it possesses
a grain that gives it its characteristic strength. However, to keep its transparent
properties, that grain has to be kept very tiny, and the amount and density of pores
in the material has to stay low as well.
Controlling for both of these structural variables is a formidable task. As we
mentioned earlier, most sintering processes do not manage to keep grain size and
pore concentration at bay, resulting in ceramics that are not so strong and completely
opaque.
So, what is the solution to this million-dollar question?
Hint: we have it right in our company's name!
Vacuum furnaces: the best way to streamline translucent alumina production
Above, we explained why a regular sinter yields opaque and brittler ceramic
components. They are certainly good enough for everyday household use,
for example, but most industrial applications require a much more sophisticated
approach.
Enter the all-powerful vacuum furnaces!
Vacuum sintering is the key to controlling the three main parameters
that influence the quality of transparent ceramics:
- Sintering temperature;
- Maintenance time at high temperatures;
- Heat-treating atmosphere.
Vacuum sintering has a particularly strong positive effect on the heat-treatment
atmosphere. It reduces oxygen levels drastically and eliminates much of pore formation
and other impurities within the material.
But how much vacuum is enough to yield these positive effects?
More vacuum, more translucence
An experiment revealed that low vacuum (around 10^-3 mbar) has a notable positive
effect on stemming pore formation; it is enough to push air and other absorbents
out. However, translucent alumina sintered in low vacuum consistently fall short
of the desired optical quality standards.
High vacuum sintering at 10^-6 mbar, on the other hand, gets the job
done. It keeps pores out and grain sizes sufficiently small. It beats atmospheric
sintering by a long shot, especially when it comes to keeping impurities out.
Keeping Impurities at bay promotes a finer grain
Atmospheric sintering is known for the higher grade of impurities that make it
into the final product. Si, Ca, K, and Mg are just some elements that can be incorporated
from the walls of the furnace into the alumina during the various preparatory stages
or during sintering. They, along with water vapor from the atmosphere, have a deleterious
effect on grain size.
Vacuum sintering minimizes these foreign substances thanks to
the continuous pumping-out process that occurs in vacuum furnaces. By removing loose
atoms and keeping oxygen pressure low, vacuum sintering establishes firm control
over grain growth.
At 1350°C and 10^-6 mbar pressure, vacuum-sintered alumina
can reach optimal purity, minimal pore density, and minimal grain size - all the
qualities that make it strong and translucent for a variety of industrial applications.
The following graph shows how vacuum sintering implies higher transmittances over a wider spectral window with respect to atmosphere treated components.
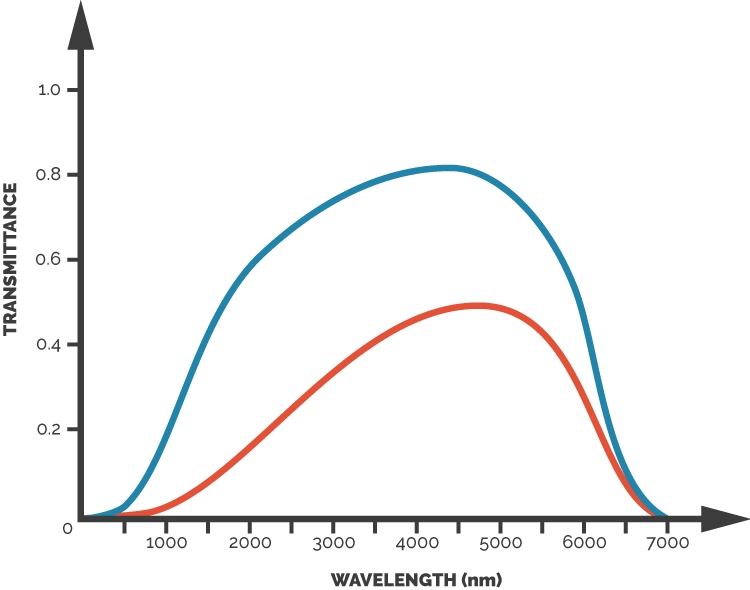
Red curve: alumina transmittance spectrum after
atmosphere sintering.
Blue curve: alumina transmittance spectrum after high vacuum sintering.
Conclusion
In our little crash course on advanced ceramics, we poured the
inspiration we got from the great
ICACC19 conference and expo into a rundown on what makes translucent alumina
such a great material. We described the process of creating this clear and robust
substance and the pivotal role vacuum furnaces play in it.
Thanks to this know-how, translucent alumina emerge as an affordable
and reliable alternative to the expensive and cumbersome production of intricate
parts, both large and small.
Have you already thought about integrating transparent ceramics into your products?
They are definitely worth your while!
Have you missed ICACC19?
Take a look at our presentation slides here below (after the free ebook chapter).
Download the FREE eBook
Download the FREE guide to vacuum sintering and get deep insight into the heat treatment process to improve your products.
Learn how powdered metal, metal injection molding (MIM), 3D printing and other similar technologies can benefit greatly from the superior quality and flexibility of vacuum sintering.