Les fabricants à la recherche d’une solution pour la fabrication de petites pièces
métalliques et de formes complexes n’ont eu que deux options jusqu’à présent:
- coulée
- moulage par injection de métal (MIM)
Alors que la coulée, utilisée depuis la nuit des temps, ne reste
compétitive que pour des pièces de grande taille ou pour lesquelles un certain manque
de précision est requis, le MIM (Moulage par Injection
de Métal) existe depuis environ 4 décennies et constitue une technologie
mûre et avantageuse. Ce dernier est en effet utilisé pour la production à grande
échelle et de haute précision de pièces petites et complexes et qui ne requièrent
pas de traitements ultérieurs.
Malheureusement le MIM a un coût élevé, surtout en raison des moules.
Les entreprises encouragent donc de plus en plus le développement d’une alternative
moins chère et plus polyvalente: l’impression métal 3D, et dans
ce cas le jet de liant 3D.
Moulage par injection de métal (MIM)
Le Moulage par Injection de Métal (MIM) est un procédé métallurgique pour la
production de matériaux de formes complexes, à partir d’une matière première sous
forme de poudre métallique compactée en pellets.
Ce procédé est né dans les années 1920 pour l’utilisation exclusive de
poudres céramiques, mais c’est dans les années 1970 qu’il s’est
imposé comme l’une des technologies les plus polyvalentes en termes de fabrication
de produits à haute complexité géométrique composés de matériaux exploitables (poudres
céramiques, poudres métalliques et polymères).
Enfin, au cours des dernières années, cette technologie s’est encore améliorée,
ce qui a permis de réduire les coûts de production et d’améliorer encore le produit
obtenu.
Le procédé MIM se divise normalement en 3 étapes principales:
- Impression
- Déliantage
- Frittage
Examinons-les maintenant plus en détails et je vous montrerai en outre deux facteurs,
respectivement dans les phases de déliantage et de frittage, à prendre en considération
pour obtenir les meilleurs résultats.
Impression
Avant le moulage, il est nécessaire de préparer la matière première qui sera
fondue, moulée, solidifiée et épaissie. Pour cette raison, la poudre métallique/céramique
est mélangée avec des proportions très précises de liant organique, pour
obtenir une solution solide homogène (également appelée feedstock).
Le composant organique est l’un des principaux protagonistes de l’ensemble du
processus, et doit répondre aux exigences suivantes:
- Il doit incorporer un pourcentage élevé de poudre métallique/céramique,
soit environ 60% du volume total.
- Il doit former une masse homogène qui peut être laminée et façonnée à hautes
températures.
- Il doit être enlevé sans causer de distorsions importantes à l’objet, en
agissant comme un élément structurel amovible.
- Il doit s’agir d’un composé qui ne cause aucun dommage à la santé et à l’environnement.
- Il ne doit pas coûter cher.
- Il doit être recyclé par des cycles de distillation.
Les rapports de volume liant / poudre métallique varient en fonction du type
et de la quantité utilisés des deux composants.
Dans ce cas spécifique, le pourcentage du volume de poudre métallique varie entre
55 et 65% (liant 45-35%).
Le liant organique thermoplastique est mélangé à sec puis à chaud (à
la température de fusion du polymère) avec la poudre métallique. Cette phase est
essentielle pour maximiser l’homogénéité du mélange. L’augmentation de la température
pendant le mélange est importante pour obtenir le niveau de viscosité le
plus bas possible et pour faciliter la phase de moulage à chaud.
À la fin du processus, le mélange est à nouveau refroidi et granulé jusqu’à l’obtention
de réels pellets.
Le feedstock est introduit dans une trémie et ensuite mis sous pression
au moyen d’une vis poussée par un vérin hydraulique, et chauffé au moyen des résistances
insérées dans la buse d’injection.
Le mélange fondu et pressé est ensuite injecté dans un moule en acier.
Le moule doit avoir des propriétés anti-abrasives, car le matériau fondu est
fortement abrasif pendant la phase de dépôt.
L’objet produit et refroidi est appelé pièce à vert et contient toujours
tout le liant en phase solide.
La faible maniabilité de la pièce à vert dépend du fait que, dans cette
phase, ce n’est que le composé polymère qui donne à la pièce ses propriétés mécaniques.
Considérons que la pièce à vert a la forme et les proportions du produit
final, mais avec un volume supérieur à 15-20% en raison de la présence du liant.
Un liant à bas point de fusion accélère le processus de déliantage, mais provoque
en même temps une séparation de phases entre le liant et la poudre métallique.
Cette ségrégation peut être causée par deux facteurs distincts:
- Gradients de distribution: ils peuvent bloquer une partie
du matériau extrudé dans l’injecteur, en diminuant la pression d’injection,
ce qui entraîne un remplissage inadéquat du moule.
- Forces centrifuges différentielles: dans ce cas, la ségrégation
résulte du processus d’injection. La phase d’injection transmet différentes
forces centrifuges au liant et aux métaux, en séparant ainsi les particules
plus lourdes et plus légères. Ce phénomène entraîne nécessairement la formation
d’une pièce à vert inhomogène.
Autrement, l’utilisation d’un liant ayant un point de fusion et un poids moléculaire
plus élevés présente un avantage en termes de viscosité, au détriment de la vitesse
de la phase de déliantage.
Il faut également tenir compte du fait que l’augmentation de la viscosité peut provoquer
des fuites d’huile (contenue dans le liant pour faciliter la phase de préparation),
qui modifieraient la forme du composant de façon permanente, en provoquant des fissures
irréversibles lors de la phase de frittage.
Il est important de choisir soigneusement une formulation de liant qui puisse
être efficace à la fois pour l’impression et pour le déliantage.
Déliantage
Il est essentiel pour le succès des étapes suivantes que le déliantage soit correctement
effectué.
Le but de cette phase est d’éliminer la plus grande partie du liant présent dans
la phase solide.
La phase de déliantage doit avoir lieu afin d’éviter la déformation, l’émiettement,
le gonflement ou la cassure de l’objet imprimé.
Il existe deux types de déliantage:
- Déliantage par solvant
- Déliantage thermique
Dans le cas du déliantage par solvant, le liant doit pouvoir
se dissoudre dans un solvant à basse température. L’acétone et l’heptane sont des
solvants généralement utilisés pour le déliantage de liants hydrophobes, bien que
l’utilisation de l’eau comme solvant soit préférable, car les liants hydrophiles
n’attaquent pas chimiquement la structure du composé.
Le déliantage par solvant n’enlève généralement qu’une partie du liant; en fait,
après cette phase on effectue le déliantage thermique.
Le déliantage thermique consiste à évaporer le liant au moyen
de la chaleur.
Ce type de déliantage s’effectue généralement dans un four sous vide,
en augmentant lentement la température afin d’éviter le gonflement et la déformation
de la pièce à vert.
À la fin du déliantage, l’objet perd du poids et du volume, en formant une structure
métallique solide, appelée en jargon pièce brune.
Frittage
Nous en sommes à l’étape finale du processus, qui vise à:
- compacter la structure, en l’épaississant jusqu’à 95% de la densité théorique
finale;
- éliminer le liant résiduel (10% maximum de liant résiduel).
À la fin, on obtient le produit avec les caractéristiques mécaniques et géométriques
définitives.
Habituellement, le frittage est effectué dans un four sous vide,
en augmentant la température jusqu’à 2/3 de la température de fusion du composé
métallique. On obtient ainsi une coalescence complète des différents grains de poudre
et une densification conséquente du composant final. Dans certains cas, on peut
faciliter la phase de frittage en la faisant précéder d’une phase de pré-frittage.
Les alliages typiquement utilisés pour la fabrication des pièces MIM sont:
- aciers de cémentation;
- acier trempé;
- acier pour roulements;
- acier inoxydable;
- acier à outils;
- alliages de fe-silicium pour applications magnétiques.
Avez-vous aimé lire l’article jusqu'ici?
Avant de continuer à lire, suivez-nous sur notre page
Facebook en cliquant
sur le bouton ci-dessous!
De cette façon, vous resterez informé des technologies les plus avancées pour les
traitements thermiques
non seulement avec nos articles, mais aussi avec les meilleures publications que nous collectons en ligne.
Binder Jetting (Jet de Liant)
En bref, un liant liquide est déposé sélectivement sur une couche de poudre métallique
et, couche après couche, l’objet final est formé.
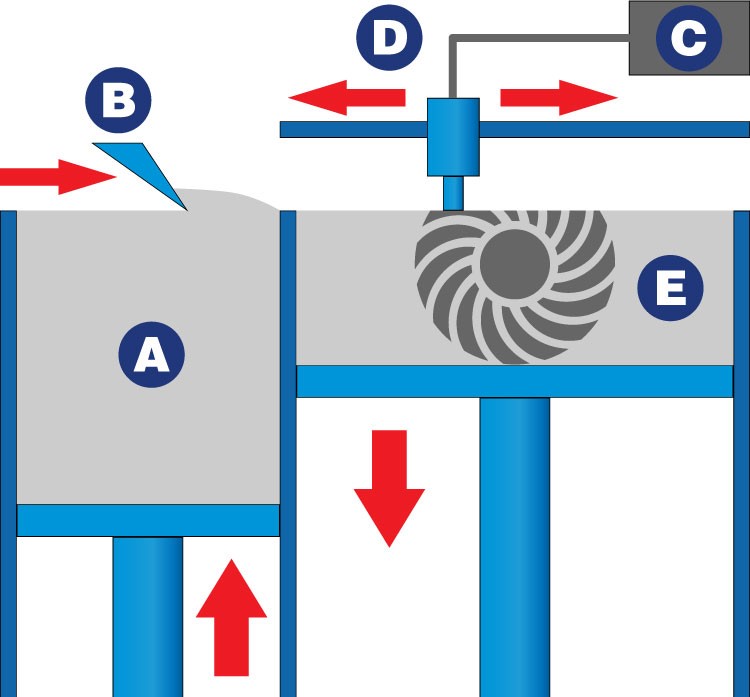
A: metal powder stock; B: squeegee; C: binder; D: print head; E: powder bed
En entrant un peu plus dans les détails, le composant à réaliser est conçu à
l’aide d’un logiciel de CAO (Conception Assistée par Ordinateur)
et le fichier résultant est envoyé à une imprimante 3D qui va produire l’objet en
le divisant en couches.
Le processus d’impression s’effectue comme décrit ci-dessous:
- Une raclette (une sorte de lame métallique) dépose une couche de poudre
sur la base qui sera utilisée pour la construction de la pièce.
- Une tête d’impression dépose sélectivement de la colle sur la poudre métallique.
La taille moyenne de chaque goutte est d’environ 80 μm de diamètre, pour obtenir
une bonne résolution.
- Une fois que le processus de dépôt de l’adhésif sur la première couche est
terminé, la base descend pour passer à la couche suivante.
- Le processus est répété à partir de l’étape (1) jusqu’à ce que toutes les
couches soient imprimées.
À la fin, l’excédent de poudre est nettoyé de l’objet, et la poudre métallique
peut être recyclée.
Une fois la phase d’impression terminée, l’objet manufacturé est dans l’état
de pièce à vert avec des propriétés mécaniques insuffisantes et une grande
porosité. Pour cette raison, des traitements ultérieurs sont nécessaires; ils sont
généralement deux:
- infiltration, et/ou
- déliantage et frittage.
Dans le cas de l’infiltration, il est nécessaire d’insérer dans les cavités réticulaires
des composés tels que: cire fondue, colle cyanoacrylate, résine époxy, etc.
Dans le cas du déliantage suivi de frittage, ces composés sont appliqués
sous vide afin d’obtenir l’élimination du liant et la coalescence subséquente
des grains de la poudre métallique.
Dans les deux cas, le but de ces traitements est de densifier la pièce moulée
pour augmenter ses propriétés mécaniques.
Suite à ces traitements, le volume de l’échantillon est fortement réduit, en
raison des forts pourcentages de liant de prétraitement, mais surtout il est réduit
d’une manière imprévisible.
Le type de liant est fortement corrélé à la poudre utilisée: par exemple, l’utilisation
d’un liant à base de furane est idéale pour les impressions en lit de silice, qui
ne requièrent pas de traitement thermique après impression. Les liants phénoliques,
d’autre part, sont excellents comme liants pour les noyaux en sable. Enfin, pour
les poudres métalliques, on utilise principalement des liants à base d’eau qui épaississent
les couches.
Les matériaux utilisés pour le jet de liant sont:
- Sable siliceux: dérivé de cristaux de quartz, il ne requiert
pas de traitements thermiques;
- Acier inoxydable: qui peut aussi être infiltré avec du
bronze. Le produit a d’excellentes propriétés mécaniques et peut être recuit;
- Alliages de cobalt-chrome-aluminium: avec d’excellentes
propriétés mécaniques à haute température.
Conclusions
Nous avons analysé les caractéristiques du MIM et du jet de liant,
en décrivant les processus de production et en mettant en évidence les aspects
positifs et négatifs de chacun d'eux.
Une technologie est-elle destinée à remplacer l'autre?
Ou les deux coexisterons entre certain domaines et avec des objectifs
spécifiques?
Ce sera le sujet que nous aborderons dans la
deuxième partie de l'article ...
ne le manquez pas!
Avez-vous aimé lire l’article jusqu'ici?
Abonnez-vous à notre newsletter gratuite, de cette façon vous pouvez rester au courant
sur les technologies les plus avancées pour les traitements thermiques.