This article is available in English too.
I produttori che sono alla ricerca di una soluzione per realizzare componenti
metallici di piccole dimensioni e forme complesse hanno avuto fino ad oggi due sole
opzioni:
- la microfusione
- lo stampaggio ad iniezione di metallo (MIM)
Mentre il casting, che viene utilizzato dalla notte dei tempi,
rimane competitivo solo per pezzi di considerevole dimensione o per cui è
richiesta una scarsa precisione, il MIM (Metal Injection
Molding) esiste da circa 4 decenni ed è una tecnologia matura e
vantaggiosa. È utilizzato infatti per la produzione in vasta scala di piccoli
e complessi componenti con precisioni elevate e tali da non richiedere lavorazioni
successive.
Qual è il rovescio della medaglia?
Purtroppo il MIM ha un costo elevato, soprattutto a causa degli stampi.
Le aziende quindi stanno incentivando sempre più lo sviluppo di un’alternativa
più economica e versatile: la stampa 3D in metallo e nella
fattispecie il 3D Binder Jetting.
Se vi state domandando quale sia la tecnologia da utilizzare, non dovete fare
altro che leggere questo articolo: vi fornirò un’esaustiva introduzione
alle due tecnologie e alla fine le metteremo a confronto evidenziandone i pro e
i contro.
Partiamo dalla prima.
Metal Injection Molding (MIM)
Il Metal Injection Molding (MIM) è un processo metallurgico per la produzione
di materiali di forma complessa, a partire da una materia prima sotto forma di
polvere metallica compattata in pellets.
Nasce negli anni ’20 con il solo utilizzo di polveri ceramiche,
ma è negli anni ’70 che si afferma come una delle tecnologie più
versatili in termini di realizzazione di prodotti ad elevata complessità
geometrica e di materiali utilizzabili (polveri ceramiche, polveri metalliche e
polimeri).
Negli ultimi anni infine, la tecnologia si è ulteriormente perfezionata con
il conseguente abbattimento dei costi di produzione e ciò ha permesso un
ulteriore miglioramento del prodotto ottenuto.
Il processo MIM è normalmente suddiviso in 3 fasi principali:
- Stampaggio
- Deceraggio (debinding)
- Sinterizzazione
Le vedremo ora nel dettaglio e inoltre vi esporrò due fattori, rispettivamente
in fase di deceraggio e in fase di sinterizzazione, da tenere in considerazione
per ottenere i migliori risultati. Non perdeteveli!
Stampaggio
Prima dello stampaggio è necessaria la preparazione della materia prima,
che verrà fusa, stampata, solidificata e addensata. Per questo motivo la
polvere metallica/ceramica viene miscelata con proporzioni ben precise di binder
(legante) organico, ottenendo una soluzione solida omogenea (chiamato
anche feedstock).
Il componente organico è uno dei protagonisti principali dell’intero
processo e deve soddisfare i seguenti requisiti:
- Inglobare un’alta percentuale di polvere metallica/ceramica, 60% di
volume circa.
- Formare una massa omogenea che può essere plastificata e modellata
ad alte temperature.
- Essere rimosso senza causare notevoli distorsioni all’oggetto pur
agendo da componente strutturale rimovibile.
- Essere un composto che non provochi danni alla salute e all’ambiente.
- Non possedere costi elevati.
- Essere riciclato tramite cicli di distillazione.
I rapporti in volume binder/polvere metallica variano a seconda della
tipologia e della quantità utilizzata dei due componenti.
Nel caso specifico, la percentuale in volume della polvere metallica varia tra il
55 e il 65% (legante 45-35%).
Il binder organico termoplastico viene miscelato a secco e successivamente
a caldo (alla temperatura di fusione del polimero) insieme alla polvere metallica.
Questa fase è essenziale al fine di massimizzare l’omogeneità
della stessa miscela. L’aumento di temperatura in fase di miscelazione è
importante per ottenere il livello più basso di viscosità
possibile e facilitare la fase di stampaggio a caldo.
Al termine del procedimento, la miscela viene di nuovo raffreddata e granulata fino
all’ottenimento dei pellets veri e propri.
Il feedstock viene inserito in una tramoggia e successivamente pressurizzato
tramite una vite spinta da un cilindro idraulico e riscaldato tramite delle resistenze
inserite in corrispondenza dell’ugello di iniezione.
La miscela fusa e pressata viene quindi iniettata in uno stampo in acciaio.
Lo stampo deve possedere caratteristiche antiabrasive in quanto il materiale fuso è
altamente abrasivo in fase di deposito.
L’oggetto prodotto e raffreddato viene definito verde e contiene
ancora tutto il legante in fase solida.
La bassa maneggevolezza del verde dipende dal fatto che, in questa fase,
le proprietà meccaniche sono conferite al pezzo solamente dal composto polimerico.
Si consideri che il verde possiede la forma e le proporzioni del prodotto
finale ma con un volume maggiore del 15-20% a causa della presenza del binder.
Leggete ora attentamente le prossime righe, perché la scelta del
legante è di fondamentale importanza affinché si ottimizzi il processo
di stampa e di debinding.
Un legante bassofondente velocizza il processo di deceraggio ma allo stesso tempo
causa una separazione di fase tra il legante e la polvere metallica.
La segregazione può essere causata da due fattori distinti:
- Gradienti di distribuzione: possono bloccare un po’
del materiale estruso nell’iniettore diminuendo la pressione di iniezione
che porta ad un inadeguato riempimento di forma.
- Forze centrifughe differenziali: in questo caso la segregazione
nasce dal processo di iniezione. La fase di iniezione trasmette al binder ed
ai metalli forze centrifughe diverse, separando quindi le particelle più
pesanti da quelle leggere. Questo fenomeno porta necessariamente alla formazione
di un verde disomogeneo.
Diversamente, utilizzando un binder con punto di fusione e peso molecolare superiori,
si ha un beneficio in termini di viscosità a scapito però della velocità
della fase di debinding.
Bisogna considerare anche che l’aumento di viscosità può causare
spurghi di olio (contenuto nel binder per agevolare la fase di preparazione) che
andrebbero a variare la forma del componente in modo permanente, causando cricche
irreversibili in fase di sinterizzazione.
Da ciò che abbiamo detto finora, ne consegue che è importante scegliere
attentamente una formulazione di binder in grado di essere efficiente sia in fase
di stampa che di debinding.
Vediamo ora la fase più delicata e critica dell’intero processo.
Deceraggio (debinding)
Un debinding effettuato correttamente è fondamentale per una buona riuscita
delle fasi successive.
Lo scopo di questa fase è quello di rimuovere la maggior parte del legante
presente in fase solida.
La fase di deceraggio deve avvenire in modo da evitare deformazioni, sgretolamenti,
rigonfiamenti o rotture dell’oggetto stampato.
Esistono due tipologie di deceratura:
- Debinding con solvente
- Debinding termico
Nel caso di deceraggio con solvente, il legante dev’essere
in grado di disciogliersi in un solvente a bassa temperatura. L’acetone e
l’eptano sono tipicamente solventi utilizzati per il debinding di leganti
idrofobici, anche se si preferisce l’utilizzo di acqua come solvente, poiché
i binder idrofili non attaccano chimicamente la struttura del composto.
Il debinding con solvente generalmente asporta solo una parte del legante, infatti,
dopo questa fase, segue il debinding termico.
Il deceraggio termico consiste nel far evaporare il binder per
via termica.
Questa tipologia di deceratura in genere si applica con i forni a vuoto,
innalzando la temperatura lentamente in modo da evitare fenomeni di rigonfiamento
e deformazione del verde.
Al termine della deceraggio, l’oggetto perde peso e volume formando una
struttura solida metallica, chiamata in gergo marrone.
Sinterizzazione
Eccoci giunti alla fase finale del processo, che ha lo scopo di:
- compattare la struttura, addensandola fino al 95% della densità teorica
finale;
- eliminare il binder residuo (10% di binder residuo massimo).
Al termine si ottiene il prodotto con le caratteristiche meccaniche e geometriche
definitive.
Di solito la sinterizzazione viene condotta in forni da vuoto,
aumentando la temperatura fino a 2/3 della temperatura di fusione del composto metallico.
In questo modo si ottiene completa coalescenza dei singoli grani di polvere con
conseguente densificazione del componente finale. In alcuni casi la fase di sinterizzazione
può essere agevolata facendola precedere da una fase di pre-sinterizzazione.
Le leghe tipicamente utilizzate per la realizzazione dei pezzi MIM sono:
- acciai da cementazione;
- acciaio da bonifica;
- acciaio per cuscinetti;
- acciaio inossidabile;
- acciaio per utensili;
- leghe Fe-silicio per applicazioni magnetiche.
Ti è piaciuto fino a qua l'articolo?
Prima di continuare nella lettura, seguici sulla nostra pagina Twitter cliccando il pulsante qui sotto!
In tal modo rimarrai aggiornato sulle tecnologie più avanzate per i trattamenti termici non solo con i nostri articoli, ma anche con le migliori pubblicazioni che raccogliamo in giro per la rete.
Binder Jetting
Vediamo ora la tecnologia più recente, l’alternativa al MIM che
negli ultimi anni è spesso sotto ai riflettori: il binder jetting
ovvero la stampa 3d del metallo. Si noti che il termine stampa
3D nel linguaggio comune viene spesso usato erroneamente come sinonimo di
manifattura additiva, invece la stampa tridimensionale è
solo una delle tecnologie possibili di manifattura additiva.
Come funziona il binder jetting?
In poche parole, un agente legante liquido viene depositato selettivamente su uno
strato di polvere metallica, dopodiché, strato su strato si forma l’oggetto
finale.
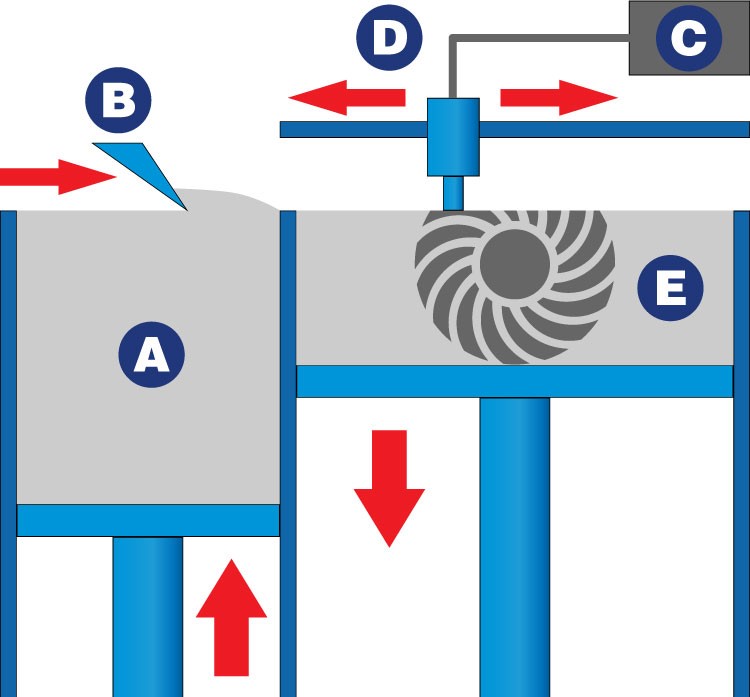
A: serbatoio polvere di metallo; B: racla; C: legante; D: testina di stampa; E: letto di polvere
Entrando un po’ più nel dettaglio, il componente da realizzare viene
progettato utilizzando un CAD (Computer-Aided Design) e il file
risultante viene inviato ad una stampante 3D che produrrà l’oggetto
suddividendolo in layer (strati).
Il processo di stampa avviene come descritto di seguito:
- Una racla (una sorta di lama metallica) stende uno strato di polvere sulla
base che verrà utilizzata per la costruzione del pezzo.
- Una testina di stampa deposita in maniera selettiva sulla polvere metallica
il materiale collante. La dimensione media di ogni goccia è di circa
80 μm di diametro, quindi è possibile ottenere una buona risoluzione.
- Una volta completato il processo di deposizione del collante sul primo strato,
la base scende per poter procedere con il layer successivo.
- Si riparte dal punto (1) fino al completamento di tutti i layer
di stampa.
Al termine l’oggetto viene ripulito dalla polvere in eccesso che
può essere riciclata.
Conclusa la fase di stampa, l’oggetto prodotto è in uno stato
di verde con scarse proprietà meccaniche e alta porosità.
Per questo motivo sono necessari dei trattamenti post processo, che sono tipicamente
due:
- infiltrazione e/o
- debinding e sinterizzazione.
Nel caso dell’infiltrazione si tratta di inserire nelle cavità
reticolari composti del tipo: cera fusa, colla cianoacrilica, resina epodossica
ecc.
Nel caso del debinding seguito dalla sinterizzazione, si applicano in vuoto
in modo da ottenere la rimozione del binder ed una successiva coalescenza dei
grani di polvere metallica.
In entrambi i casi lo scopo di questi trattamenti è quello di densificare
il componente stampato in modo da aumentarne le proprietà meccaniche.
In seguito a questi trattamenti, il volume del campione si riduce parecchio,
a causa delle elevate percentuali di binder pretrattamento, ma soprattutto in
maniera poco prevedibile.
Il tipo di legante è fortemente correlato alla polvere utilizzata:
ad esempio l’utilizzo di un legante furanico è ideale per stampe
a letto di silice che non richiedono un trattamento termico post stampa. I leganti
fenolici invece sono ottimi come leganti per forme ad anime di sabbia. Per le
polveri metalliche infine vengono utilizzati principalmente leganti a base acquosa
in grado di addensare gli strati.
I materiali utilizzati nel binder jetting sono:
- Sabbia di silice: derivante da cristalli al quarzo, non
necessita di trattamenti termici;
- Acciaio inossidabile: il quale può essere anche
infiltrato con bronzo. Il prodotto possiede ottime proprietà meccaniche
e può essere ricotto;
- Leghe di cobalto-cromo-allumino: con eccellenti proprietà
di resistenza meccaniche ad alta temperatura
Conclusioni
Abbiamo analizzato le caratteristiche del MIM e del binder jetting,
descrivendo i processi di produzione e mettendo in evidenza i lati positivi e negativi
di ognuno di essi.
Una tecnologia è destinata a sostituire l’altra?
Oppure coesisteranno entrambe, ognuna in ambiti e con finalità specifiche?
Questo sarà l’argomento che affronteremo nella seconda parte dell’articolo… non perdetevelo!
Ti è piaciuto l'articolo?
Iscriviti al nostro canale Telegram, in tal modo potrai restare aggiornato sulle tecnologie più avanzate per i trattamenti termici.
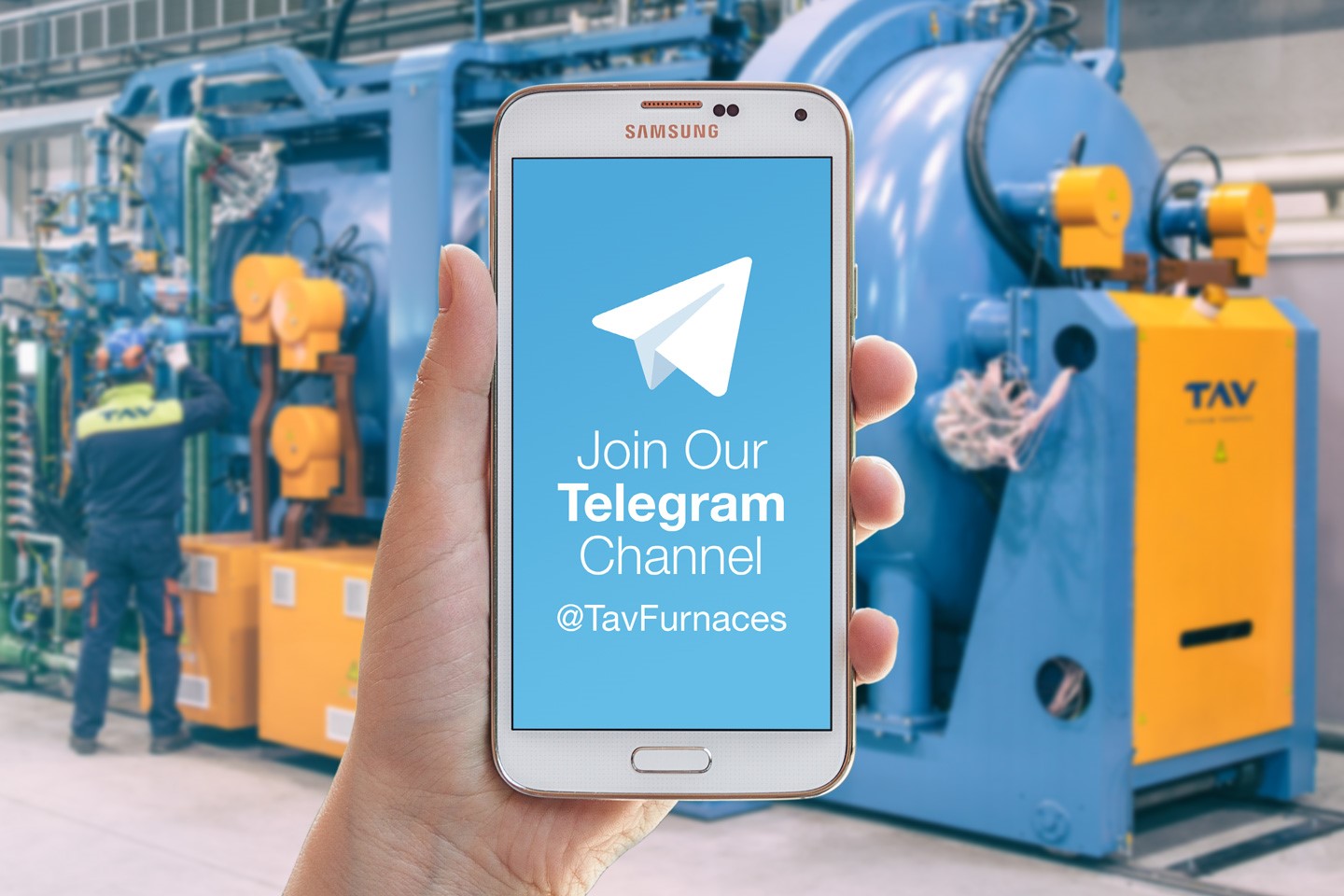
Non hai Telegram?
Se ancora non hai Telegram, usa uno dei seguenti pulsanti per installarlo:
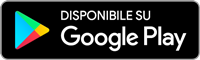
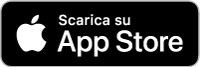