This article is available in English too.
La manifattura additiva con metalli e leghe
Con il termine Manifattura Additiva (AM) si intende il processo che permette
di unire dei materiali, utilizzando tecnologie anche molto diverse tra loro e secondo
una modalità strato su strato (Manifattura Additiva), per realizzare oggetti (es.
parti componenti, semilavorati o prodotti finiti) a partire da modelli 3D
digitali, opposto alle metodologie di produzione tradizionali (tornitura,
fresatura, ecc.) che prevedono invece la sottrazione dal pieno (Manifattura Sottrattiva).
Le tecniche di AM prevedono che l’oggetto tridimensionale venga creato a partire
da modelli 3D computerizzati ed utilizzando materiali differenti tra cui quelli
metallici, plastici, ceramici, compositi o biologici.
Nella manifattura additiva di metalli e leghe, questi vengono utilizzati sotto forma di polveri
o fili.
La materia prima viene selettivamente fusa da una fonte di calore focalizzata
e poi consolidata durante il raffreddamento, per formare infine il pezzo progettato.
I processi di AM che più degli altri impiegano materiali metallici, sono quelli
compresi nelle categorie Powder Bed Fusion (PBF) e Direct Energy Deposition
(DED), in particolare: Selective Laser Melting (SLM) Direct Metal Laser
Sintering (DMLS), Electron Beam Melting (EBM), Laser Engineered
Net Shaping (LENS), Direct Metal Deposition (DMD).
Tra i materiali metallici commerciali attualmente disponibili per essere lavorati
tramite processi di AM ci sono: il Ti puro, la lega Ti-6Al-4V, alcuni acciai inossidabili
come il 316L, e il PH 17-4, l’acciaio maraging 18Ni300, la lega AlSi10Mg, le leghe
CoCrMo e la superlega a base Ni-Cr Inconel 625.
All’elenco appena proposto, si possono
aggiungere i materiali riportati nella Tabella 1.
Titanio |
Alluminio |
Acciai da utensili |
Superleghe |
Acciai inossidabili |
Refrattari |
ELI Ti |
6061 |
H13 |
IN718 |
316 |
MoRe |
TiAl |
|
Cermets |
Stellite |
420 |
Ta-W |
CP Ti |
|
|
|
347 |
Allumina |
Tabella 1 – Materiali metallici per AM
I metalli preziosi, come l’oro, l’argento e il platino sono stati trattati indirettamente,
cioè sono stati realizzati, tramite stampa 3D, stampi per la tecnica di fusione
a cera persa, in cui i materiali citati sono stati colati; gli stessi materiali
vengono anche utilizzati direttamente, per esempio, con la tecnica SLM.
Tra i materiali metallici appena elencati, gli acciai inossidabili sono quelli
che trovano applicazione nel maggior numero di settori: aerospaziale,
medico, energetico,
automobilistico, navale, ecc.
Le caratteristiche meccaniche (resistenza a sollecitazioni statiche e dinamiche)
e la densità dei pezzi prodotti tramite manifattura additiva con questi materiali sono da tempo studiate
e sono attualmente molto elevate, cioè simili se non superiori a quelle dei pezzi
prodotti tradizionalmente. Meno nota ed indagata, invece, è la loro resistenza a
corrosione. Tale proprietà è fondamentale in applicazioni specifiche, come per esempio,
quelle del settore nautico.
Studio della resistenza a corrosione di pezzi metallici realizzati tramite AM:
caratteristiche dei materiali studiati ed analisi effettuate
Per investigare il comportamento a corrosione di pezzi in acciaio inossidabile
prodotti tramite manifattura additiva, la sezione di Metallurgia del Dipartimento di Chimica e Chimica
Industriale (DCCI) dell’Università degli Studi di Genova in collaborazione con TAV
VACUUM FURNACES, la ditta Saiem Srl di Cairo Montenotte (Savona) e il CNR-ICMATE
di Padova hanno avviato lo studio di campioni in acciaio 316L realizzati tramite
la tecnica SLM (Selective Laser Melting). Nello specifico, Saiem Srl ha prodotto una serie di campioni, di
dimensioni 1x1x1 cm3 (Figura 1) utilizzando il sistema TRUMPF Tru Print
1000 e polveri pre-legate appositamente progettate e testate per l’utilizzo con
la stampante 3D citata.
Come si può desumere dalla stessa immagine (Figura 1), i
pezzi prodotti hanno superfici con morfologia e rugosità differenti tra loro.
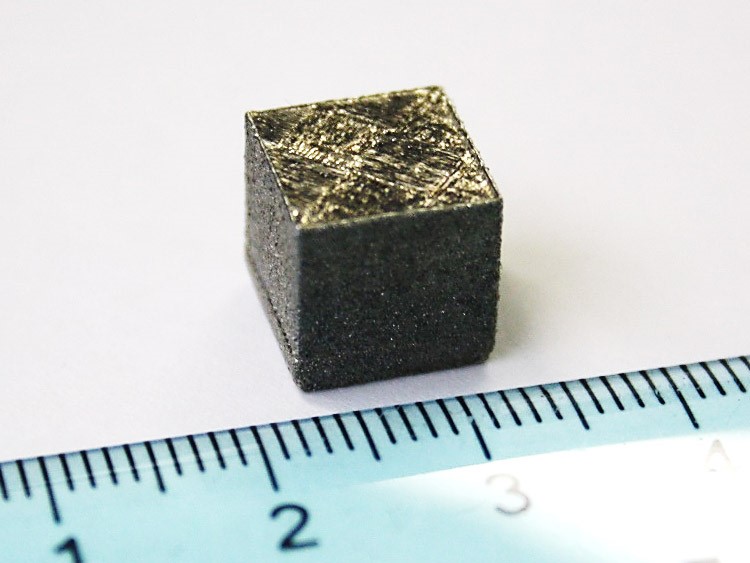
Figura 1 – Cubo 1x1x1 cm3 realizzato tramite
SLM
Le parti finali realizzate hanno la composizione indicata in Tabella 2, corrispondente
a quella dell’acciaio inossidabile austenitico 316L (X2 CrNiMo17-2-2, DIN EN 10088-1).
Fe |
Cr |
Ni |
Mo |
Mn |
Si |
C |
N |
P |
S |
Bul. |
16.5-18.5 |
10.0-13.0 |
2.00-2.50 |
<2.00 |
<1.00 |
<0.030 |
<0.10 |
<0.045 |
<0.015 |
Tabella 2 – Composizione chimica delle parti stampate
(wt.%)
Per lo studio della microstruttura e della resistenza a corrosione, i campioni
sono stati poi sottoposti rispettivamente a caratterizzazione metallografica ed
elettrochimica, la prima tramite Microscopia Elettronica a Scansione (SEM),
Spettroscopia
di Fluorescenza di Raggi X e Microscopia Ottica in Campo Chiaro (LOM-BF), la seconda
per mezzo di Analisi Potenziometriche e Spettroscopia di Impedenza Elettrochimica
(EIS).
Parte dei campioni prodotti da Saiem Srl è stata ulteriormente trattata e cioè,
alcuni cubi sono stati rivestiti con coating a base di TiN (sia presso TAV
VACUUM FURNACES sia presso
il CNR ICMATE di Pd), altri a base di AlTiN (presso il CNR), altri ancora sono stati
sottoposti a ciclo termico.
Il ciclo termico applicato, Figura 2, è stato effettuato
presso TAV VACUUM FURNACES.
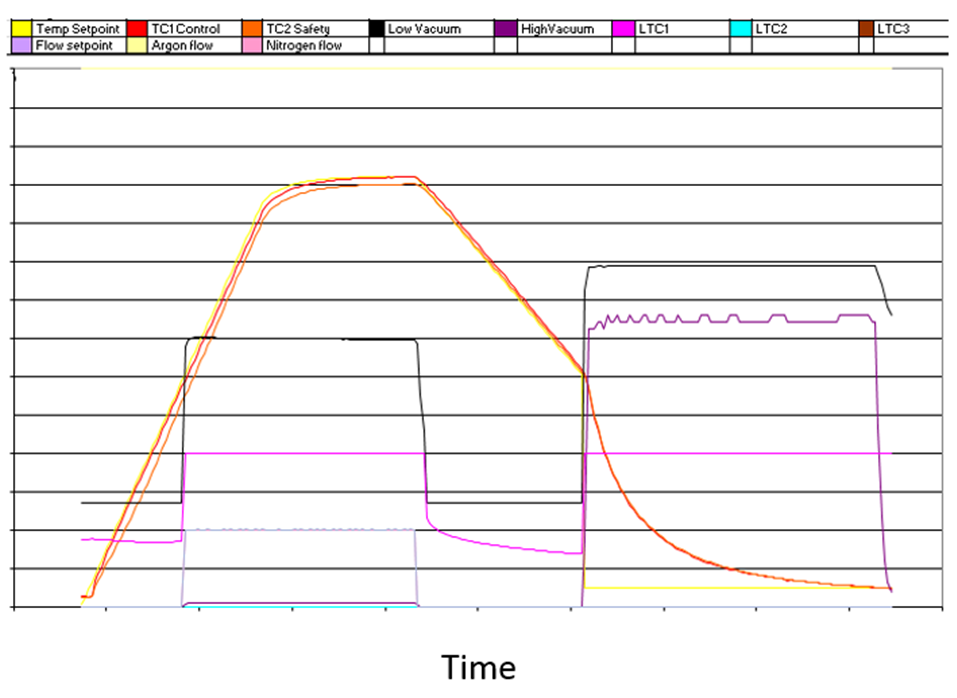
Figura 3. Ciclo termico applicato
Anche di questi campioni, cioè quelli rivestiti con coating di diversa composizione
o sottoposti a trattamento termico, sono stati valutati sia gli aspetti microstrutturali
sia il comportamento a corrosione. In particolare, si è voluto verificare se i trattamenti
applicati risultassero in un miglioramento o peggioramento della resistenza a corrosione
dei campioni studiati.
Ti è piaciuto fino a qua l'articolo?
Prima di continuare nella lettura, seguici sulla nostra pagina Facebook cliccando il pulsante qui sotto!
In tal modo rimarrai aggiornato sulle tecnologie più avanzate per i trattamenti termici non solo con i nostri articoli, ma anche con le migliori pubblicazioni che raccogliamo in giro per la rete.
Risultati di laboratorio
Caratteristiche metallografiche dei campioni
L’analisi microstrutturale ha riguardato le sezioni longitudinale e trasversale
dei campioni tal quali e quella longitudinale dei campioni sottoposti a trattamento
termico.
Lo studio delle micrografie SEM e LOM-BF ha permesso di riscontrare un’elevata
densità dei pezzi prodotti. Pochi sono i pori visibili e caratterizzati da forme
sferiche con un diametro compreso tra 1 e 10 mm (attribuibili a gas rimasti intrappolati
nel materiale durante la produzione del pezzo), o da forme irregolari (questi pori
sono dovuti al processo di stampa stesso e possono avere dimensioni da macroscopiche
a sub-micrometriche).
La microstruttura dei campioni, investigata dopo attacco con acqua regia (HNO3:HCl:H2O
3:10:10 in volume), ha messo in evidenza la presenza di grani allungati ed orientati
lungo la direzione di costruzione del pezzo corrispondente alla direzione di svolgimento
del calore (Figura 4), le singole melting pool, con dimensioni
di circa 100 mm lungo l’asse orizzontale, geminati ed una struttura cellulare in
cui gli spazi intracellulari sono inferiori ad 1 mm (Figura 5).
La microstruttura
appena descritta, soprattutto la struttura cellulare osservata, è tipica dei pezzi
metallici prodotti tramite tecniche di manifattura additiva, caratterizzate da processi di solidificazione
con velocità di raffreddamento elevate ed elevato grado di sottoraffreddamento.
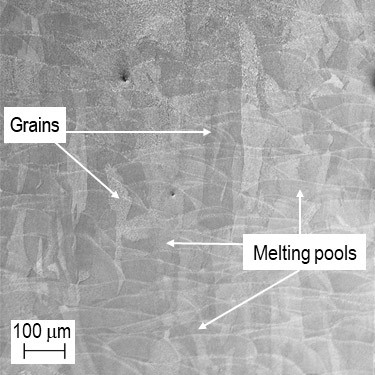
Figura 4 – SEM-SE: Microstruttura del campione
lungo la sezione longitudinale dopo attacco con acqua regia (ingrandimento
200x).
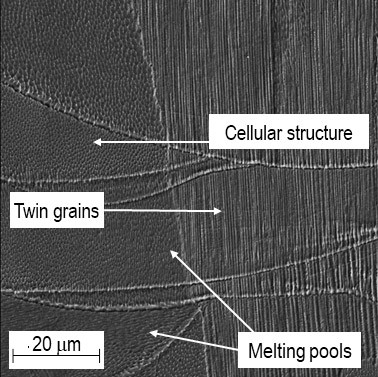
Figura 5 – SEM-SE: Microstruttura del campione
lungo la sezione longitudinale dopo attacco con acqua regia (ingrandimento
8500x).
Nel caso dei campioni sottoposti a trattamento termico la microstruttura è differente
da quella riscontrata osservando i campioni as printed, dal momento che
essa risulta caratterizzata da grani di grandi dimensioni ed in cui dettagli come
le melting pool, i geminati e la struttura cellulare, non sono più apprezzabili.
Caratteristiche elettrochimiche dei campioni
Le misure elettrochimiche hanno riguardato le superfici laterale ed inferiore
del campione prodotto tramite SLM al fine di verificarne il comportamento a corrosione
in relazione ad un campione di riferimento di 316L commercialmente utilizzato.
Prove di polarizzazione elettrochimica
Queste misure hanno evidenziato un comportamento passivo variabile, tipico di
un materiale caratterizzato da un film di ossidazione superficiale che limita enormemente
le cinetiche di corrosione agendo sulla semi-reazione anodica.
Paragonando il campione
ottenuto tramite SLM con un campione di 316L in commercio si possono notare intervalli
di passività minori per tutte le facce esposte, cioè quella inferiore e quella laterale,
con più alte densità di corrente di corrosione per la faccia laterale.
Le maggiori criticità, riscontrate sulla superficie laterale, si possono correlare
alla sua morfologia e al numero e distribuzione delle porosità che determinano fenomeni
addizionali di interfaccia, da approfondire ulteriormente.
Il lavoro è proseguito con la valutazione del comportamento a corrosione della
faccia laterale tal quale e della stessa faccia sottoposta a diversi trattamenti
superficiali e a trattamento termico.
Le misure hanno evidenziato che i trattamenti superficiali sono risultati in
una maggiore protezione del campione. In particolare, tra i trattamenti applicati,
quello che ha fornito una protezione migliore è stato quello a base di TiN depositato
presso TAV VACUUM FURNACES.
Spettroscopia di impedenza elettrochimica (EIS)
A rappresentanza del campione massivo è stata considerata la superficie inferiore
del campione stampato tramite SLM, confrontata con un campione di riferimento di
AISI 316L. L’EIS misurata per la superficie inferiore è risultata paragonabile a
quella ottenuta dal campione di riferimento, con un leggero sbilanciamento verso
un miglior comportamento a corrosione da parte del campione stampato.
La similarità
tra risultati ottenuti è imputabile alla confrontabile finitura superficiale, ottenuta
in entrambi i casi mediante lucidatura con carte abrasive.
Per quanto riguarda i campioni caratterizzati da diversa morfologia superficiale
e sottoposti ad ulteriori trattamenti, i massimi valori di resistenza sono stati
riscontrati per il campione rivestito con TiN presso TAV VACUUM FURNACES.
Il miglior comportamento
a corrosione è attribuibile alla natura dello strato applicato e al miglior ricoprimento
della superficie.
Conclusioni
Le analisi effettuate hanno evidenziato criticità per il campione ottenuto tramite
SLM in relazione al tipo di superficie esposta.
L’applicazione di coating e del
trattamento termico ha permesso di ottenere buoni risultati dal punto di vista della
resistenza a corrosione.
Hanno collaborato alla realizzazione del progetto di studio
Università degli Studi di Genova:
P. Piccardo, V. Bongiorno, R. Spotorno, G. Ghiara
SAIEM S.r.l.: F. Fraternale, A. Ghiglia
TAV VACUUM FURNACES SPA: A. Fiorese
ICMATE-CNR: S. Battiston,
F. Montagner
Ti è piaciuto l'articolo?
Iscriviti alla nostra newsletter gratuita, in tal modo potrai restare aggiornato sulle tecnologie più avanzate per i trattamenti termici.