La manifattura additiva (AM) è una famiglia di tecnologie bottom-up che possono rispondere alle necessità, supportando la fabbricazione rapida di componenti con forme complesse.
I vantaggi più noti della manifattura additiva sono la flessibilità nella progettazione delle parti, la possibilità di realizzare parti leggere, proprietà meccaniche superiori a quelle dei materiali fusi convenzionalmente e l'integrazione di diverse funzionalità.
Tra le tecnologie industriali AM, la fusione laser selettiva (Selective Laser Melting, SLM) è la più diffusa, grazie alla stabilità del processo e al suo ottimo rapporto tra costi e qualità delle parti.
Tuttavia, i prodotti ottenuti con la fusione laser selettiva richiedono la post-elaborazione, come
- trattamenti termici per la distensione,
- finiture per migliorare la qualità della superficie e controllare le tolleranze dimensionali,
- rivestimenti per dotare le superfici di ulteriori proprietà.
Il processo in tre fasi
Lo studio dell'intero percorso di produzione, inclusi il processo SLM, i trattamenti termici e la deposizione di sottili pellicole funzionali, permette di ottenere strumenti stampati pronti all'uso, potenzialmente con forme complesse e alto grado di personalizzazione.
In questo articolo vedremo come sia possibile eseguire il processo di deposizione di film sottili per rivestire substrati in titanio, realizzati tramite fusione laser selettiva.
Continua a leggere per ottenere una risposta completa alle seguenti domande.
È possibile rivestire i substrati in lega di titanio per ottenere un miglioramento delle caratteristiche meccaniche della superficie?
Qual è il ruolo dei trattamenti termici sottovuoto sui pezzi ottenuti tramite manifattura additiva?
I percorsi di scansione del laser possono influire sulla risultante adesione dei rivestimenti?
E altro ancora…
Fase 1: fusione laser selettiva
Il SLM è un processo a letto di polvere, in cui un raggio laser grazie alla scansione può fondere una porzione limitata di polvere sullo strato corrente. Il processo viene replicato per diversi strati (layer), dando quindi origine a parti 3D semifinite, prodotte attraverso una strategia di produzione strato per strato.
Grazie alle dimensioni limitate della vasca del liquido, vengono indotte velocità di raffreddamento molto elevate e ciò consente di ottenere microstrutture fini.
Per quanto riguarda la disponibilità di materiali che possono essere elaborati mediante fusione laser selettiva, La lega di titanio64 (Ti6Al4V) ha una buona lavorabilità ed è un materiale molto diffuso in diversi settori, come quello biomedico e quello aerospaziale.
Produrremo campioni cilindrici da polvere commerciale di Ti6Al4V per mezzo di una stampante 3D a fusione laser selettiva (mod. AM400 di Renishaw, installata presso la sede di Lecco del CNR ICMATE).
I parametri di processo adottati sono elencati nella tabella seguente.
Strategia di scansione |
Potenza |
Tempo di esposizione |
Spessore dello strato |
Distanza punto/tratteggio |
Temperatura della piattaforma |
Atmosfera |
Meander |
200W |
50µS |
30µm |
75µm |
30°C |
Argon |
Contour |
100W |
60µS |
30µm |
75µm |
30°C |
Argon |
La caratterizzazione topologica tridimensionale mediante uno stylus profiler (Bruker, Dektat XT), è stata effettuata su diverse superfici del substrato, al fine di valutare le caratteristiche geometriche dei campioni preparati con SLM e identificare lo schema di scansione ottimale adatto per la successiva deposizione HiPIMS.
Abbiamo testato 2 diversi design di scansione per realizzare campioni, meander (zig-zag) e contour (spirale).
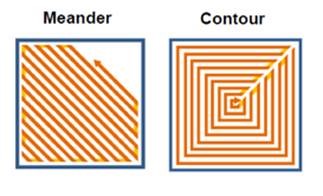
Più avanti in questo articolo vedremo come ciò abbia portato a risultati interessanti.
Ti è piaciuto fino a qua l'articolo?
Prima di continuare nella lettura, seguici sulla nostra pagina Facebook cliccando il pulsante qui sotto!
In tal modo rimarrai aggiornato sulle tecnologie più avanzate per i trattamenti termici non solo con i nostri articoli, ma anche con le migliori pubblicazioni che raccogliamo in giro per la rete.
Fase 2: trattamenti termici in vuoto del substrato
I substrati ottenuti il selective laser melting sono stati trattati termicamente con un forno in vuoto all metal TAV H3 a 950°C per 1 ora al fine di valutare come la struttura del materiale risultante e i cambiamenti della microstruttura potessero influenzare la crescita della sottile pellicola e, di conseguenza, le loro proprietà meccaniche.
I trattamenti termici sono stati effettuati in alto vuoto (circa 10-5-10-6 mbar).
Fase 3: processo di deposizione di film sottili
La Physical Vapor Deposition High-Power Impulse Magnetron Sputtering (PVD HiPIMS) rappresenta un'evoluzione della tecnica convenzionale di magnetron sputtering e consente di depositare rivestimenti di alta qualità, densi e aderenti su substrati con forme complesse.
Inoltre, per le loro eccellenti proprietà di resistenza all'usura e alla corrosione, la dure pellicole di AlTiN sono ampiamente utilizzate in molte applicazioni ad esempio utensili da taglio, settore dei motori aeronautici, bio-impianti, ecc.
In questo trattato, è stato studiato l'effetto dei rivestimenti duri di AlTiN dei ui campioni piatti AMed Ti6Al4V sulle proprietà microstrutturali e meccaniche. La microstruttura e la risposta meccanica dei film depositati sono stati caratterizzati mediante Microscopia a Scansione Elettronica (Scanning Electron Microscopy, SEM), diffrazione dei raggi X (-Rays Diffraction, XRD) e test di nanoindentazione.
Uno sguardo più da vicino al processo di coating
Le condizioni del processo di deposizione PVD HiPIMS sono state adattate per ottimizzare l'abbinamento tra il substrato metallico e il rivestimento ceramico.
Le pellicole protettive sottili sono state depositati mediante HiPIMS PVD reattivo su vetrini rivestiti di Si (100) (Si-Mat), dischi Ti6Al4V lucidati (ottenuti da una billetta in lega di titanio commerciale con una forma finale cilindrica con un diametro di 25 mm e uno spessore di 4 mm) e substrati lucidati ottenuti con fusi laser selettiva a zig-zag (prima e dopo il trattamento termico sotto vuoto).
- Il processo di lucidatura effettuato per alcuni dei campioni di lega di titanio è stato eseguito con una sospensione di silice colloidale (OP-U, 0,04 µm, Struers) con la lucidatrice Tegramin 20 (Struers).
I substrati sono stati quindi sonicati in etanolo e isopropanolo ed essiccati con N2 (99.998%).
- Il processo di sputtering è stato eseguito a partire da una pressione di base di 5,0×10-7 mbar, impiegando un target AlTi (50:50 al%, puro al 99,9%, con diametro di 50,8 mm, acquistato da MaTek), con una pressione di esercizio totale di 5,0 x 10-3 mbar, in atmosfera costituita da una miscela di Ar (99.9997%) con diverse pressioni parziali di N2 (pn2, 99,998%), come 14%, 20%, 25% e 30%.
- Il processo di deposizione è stato guidato da un alimentatore Ionautics Hipster 6 mantenendo una densità di potenza costante (15 W cm-2), frequenza (1500 Hz), tempo di impulso (50 µs), polarizzazione del substrato fornita da Ionautics Hipster 1 (-50 V potenza, frequenza 1500 Hz, tempo impulso 100 µs, sincronizzato), temperatura (350°C) e la distanza target-substrato (60 mm).
Raccolta dati
Raccogliamo ora i risultati sperimentali sulle caratterizzazioni microstrutturali e meccaniche.
La struttura, la composizione e le caratteristiche meccaniche dei film sottili sono state studiate mediante X-ray Diffraction (XRD), Energy Dispersive Spectroscopy (EDS) associata alla Field Emission Scanning Electron Microscopy (FE-SEM) e nanoindentazione. Infine, la FE-SEM è stata impiegata anche per valutare l'evoluzione della microstruttura di entrambi i substrati e i film sottili.
Se sei interessato agli strumenti che abbiamo utilizzato per l'acquisizione dei dati sperimentali, leggi qui sotto, altrimenti passa direttamente al capitolo successivo.
- Profili di diffrazione dei raggi X. dei campioni sono stati ottenuti utilizzando un diffrattometro a raggi X PW 3710 Philips con geometria Bragg-Brentano e una sorgente CuKα (40 kV, 30 mA). L'identificazione della fase sui profili XRD è stata effettuata utilizzando il software Match!, sfruttando il database di strutture cristalline inorganiche.
- Le caratterizzazioni compositive morfologiche e quantitative sono stati eseguite al microscopio elettronico a scansione di emissione di campo Sigma Zeiss dotato del sistema di spettroscopia a raggi X a dispersione di energia (EDS) di Oxford X-Max. Le analisi dei punti EDS sono state condotte su film AlTiN depositati a una tensione di accelerazione di 20 kV, con un tempo di acquisizione di 50 secondi, utilizzando il software INCA 4.14 (Oxford Instruments).
Per queste analisi, i film sono stati depositati su vetrini rivestiti di nanocristalli di Si con uno spessore superiore a 2 µm per avere un substrato perfettamente planare e conduttivo, al fine di minimizzare gli errori dovuti alla morfologia della superficie e all'influenza della natura del substrato, e quindi rendere affidabile la valutazione di quantificazione.
Il software è stato calibrato per la quantificazione, facendo riferimento agli standard di Co optimization, con BN lucido, così come gli standard per N, Al e Ti. Le formule empiriche sono state calcolate mantenendo il numero di atomi di N fissato a 1,0 e i rispettivi errori sono stati calcolati come deviazioni standard delle misurazioni.
- I valori di durezza e del modulo elastico sono stati misurati mediante nanoindentazione strumentata, con sistema Nanotest (micromateriali, Wrexham, Regno Unito) dotato di punta Berkovich.
I test sono stati eseguiti in modalità di controllo della profondità e la profondità massima è stata selezionata in modo tale che la profondità di penetrazione finale di ciascun rientro fosse inferiore al 10% dello spessore medio del film, al fine di ridurre al minimo l'influenza del substrato sulle misurazioni.
I dati sono stati ottenuti mediante analisi statistica di 25 rientranze per ciascuna superficie del campione, disposte su griglie quadrate. La nano-durezza e il modulo elastico sono stati stimati applicando il metodo Oliver e Pharr alle risultanti curve di carico-spostamento.
Conclusioni
Ora siamo pronti per analizzare i dati dei processi di manifattura additiva e di coating.
Non perdere il prossimo articolo, risponderemo a molte domande irrisolte, dandoti un ampia panoramica delle possibilità offerte da queste nuove tecnologie.
National Research Council; Institute of Condensed Matter Chemistry and Technologies for Energy (Padova): S. Battiston, F. Montagner, V. Zin
National Research Council; Institute of Condensed Matter Chemistry and Technologies for Energy (Lecco): C.A. Biffi, J. Fiocchi, A. Tuissi
TAV VACUUM FURNACES SpA: A. Fiorese, A. Gionda
Ti è piaciuto l'articolo?
Iscriviti alla nostra newsletter gratuita, in tal modo potrai restare aggiornato sulle tecnologie più avanzate per i trattamenti termici.