Additive manufacturing and vacuum heat treatments are technologies capable of
making important progress in various sectors, including dentistry applications.
TAV VACUUM FURNACES has developed a research and development collaboration with
Sisma
S.p.A., which produces high precision laser machines and the Department of Industrial Engineering of the University of Trento, prestigious excellences of the Italian industry and academy.
The team dealt with additive manufacturing with particular attention to vacuum
heat treatments as regards the creation of dental prostheses.
The potential of this innovative technology is decidedly surprising, but before
moving on to their exposure we must start from the beginning, which can only be
one: what is additive manufacturing?
Two words on additive manufacturing
Additive manufacturing creates three-dimensional solid objects from a CAD file.
Unlike the subtractive manufacturing which, as the word itself says, removes excess
from a block of material to give life to a finished object, the additive manufacturing
does the exact opposite.
Layer by layer adds the different parts present in the model of a 3D project up
to the complete realization of the object.
3D models can be constructed using a laser source or an electron source and a
powder bed. Unlike the more traditional processes, thanks to 3D metal printing,
the parts produced can be highly customized and enjoy a decidedly optimized functionality.
The additive manufacturing allows to obtain a semi-finished solid three-dimensional
part.
The Laser Metal Fusion (LMF), used in this study, is among the
most advanced additive manufacturing technologies: a computer controls a laser beam
which melts a metallic powder. The result is the creation of an extremely detailed
final product.
Furthermore, one of the most well-known advantages of 3D printing, only the material
necessary for the production of the piece is used, without waste.
Additive manufacturing has been used for some time to create a prototype in a
relatively short time.
Lately the use of this processing technique has extended to various areas of the
industrial sector and ranges from aerospace applications to those
for the automotive.
Its versatility and the use of vacuum heat treatments has also allowed it to touch
another important field: that of medical-dental applications.
In the dentist's chair
Now, to better understand the matter, let's move for a moment to the dentist's
chair ... so to speak.
Fixed half-arch or full-arch dental prostheses must be fixed on the patient's
natural tooth stumps or on titanium implants.
The best known examples of these types of prostheses are the "all on 4”
and the "all on 6”, That is, full arch prostheses that are anchored
to 4 or 6 implants respectively. In both cases the prostheses, before being installed,
must be covered with a ceramic material.
And here comes the crucial point.
Before the ceramicization process and the application on the patient,
the prostheses must be subjected to a heat treatment and, subsequently, they must
be removed from the plate that supports them.
Improvements in the process chain of dental prostheses
Here we are at the heart of the problem.
Let's see how this research and development project managed to optimize
the process of making a dental prosthesis using a vacuum furnace.
The additive manufacturing allows to create shapes, weights and dimensions customized
on different needs and with a precision that has no equal. Strengthened by these
peculiarities, the research team worked to further refine and complete the process
chain of dental prostheses.
Let's see step by step how this process happened.
- The research team started from 3D printing and, first of
all, optimized its parameters. Sisma, using Ti6Al4V powder, produced the samples
in question using the Laser Metal Fusion that I mentioned earlier.
The MySint 100 RM machine was used for additive manufacturing and the samples
were made on a titanium plate.
- The research team then moved on to mechanical characterization of
the components with an analysis of the behavior of the material subjected
to stress, deformation, scratches and static resistance to temperatures, thus
obtaining an evaluation of its hardness and resilience.
- Finally, the researchers focused on the third fundamental step: that of
optimizing the final component thanks to a post-print vacuum heat treatment.
Why heat treating the prosthesis?
The vacuum heat treatment aims to improve the mechanical properties
of the materials.
- The penultimate step is that of dental prosthesis ceramicization
(half arch and full arch).
- At the end of the process chain the prostheses are removed from the titanium
plate: the operation was carried out through the use of one cropper.
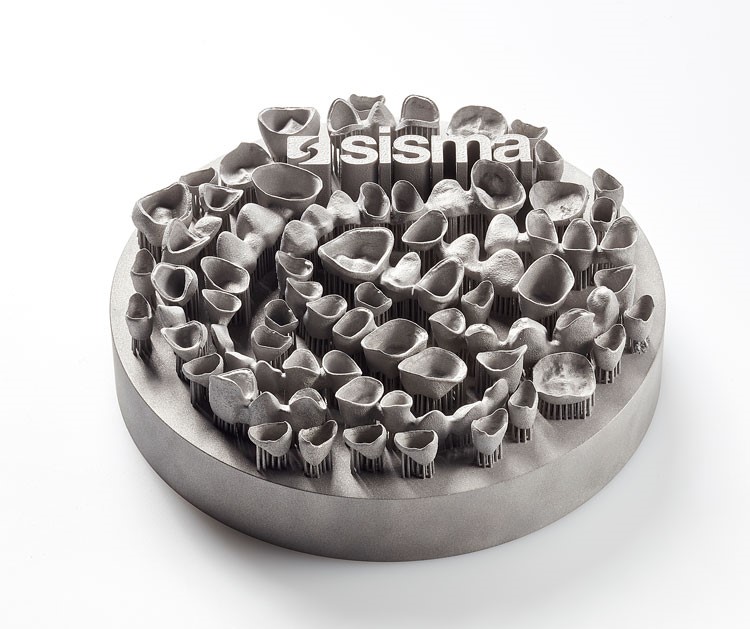
Printed parts before removing them from the plate
Why do vacuum furnaces play a primary role in additive manufacturing?
If you have the patience to follow me a little more in reading I will tell you about
three main advantages that vacuum heat treatments offer to the dental medical
sector.
Did you like this article up to here?
Before you continue, follow us on our Facebook page pressing the button here below!
In this way, we'll be able to keep you updated on most advanced technologies for heat treatments not only with our posts, but also with the best articles that we collect around the web.
Vacuum heat treatments and dental applications: all the benefits
Vacuum heat treatment has a fundamental role in the additive manufacturing of
dental applications.
Now let's keep our promise, I'll show you the three main advantages that
can be obtained with this process.
1. Stress relief treatment
During the printing phase subcooling phenomena occur related
to the passage of the laser on the metal powder. This creates mechanical tensions
that the stress relief treatment is able to remove.
2. Optimization of mechanical properties
The team heat treated the newly printed samples in vacuum, noting that the synergy
between the temperature and the high level of vacuum inside the thermal chamber
allowed to obtain considerable results on titanium dental prostheses.
More specifically, low temperature heat treatments are among the main defendants
of the release of most of the residual stress accumulated during the 3D printing
process.
Heat treatments at higher temperatures relieve residual stresses and
modify the metallurgical microstructure of the material, optimizing the
final component also from the point of view of mechanical properties.
3. Unaltered geometries
The geometric properties remain unchanged: it is essential that the sample after
treatment has superior mechanical properties compared to the starting ones. Equally
basic is that, at the same time, the geometric properties remain unchanged.
Preservation of the initial dimensions is obviously one essential feature
so that the prosthesis is perfectly compatible with the implant and with
the patient's mouth.
In the following figures it is possible to appreciate the fitting difference
between a newly printed prosthesis (as built) and a prosthesis that has
undergone a vacuum heat treatment.
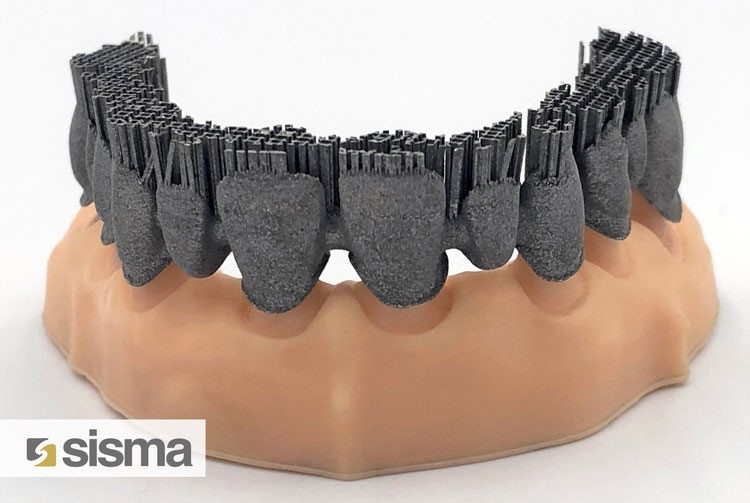
“As built” dental arch produced by Sisma with
LMF technology
Dental arch after stress relieving vacuum heat treatment
One last consideration
The R&D team would not have achieved these important results if it had not
given due importance to theatmosphere effect in which the heat
treatment is carried out. This must indeed happen to a high level of vacuum
guaranteed throughout the thermal cycle. In the absence of this requirement,
the oxygen present in the thermal chamber at high temperatures would cause the oxidation
of the titanium thus compromising the quality and compliance with the medical specifications
of the sample.
Do you need more info?
Write to our engineers and discover all the vacuum furnace applications for the medical-dental sector.