From 5th to 8th September, TAV VACUUM FURNACES participated at the 27th IFHTSE Congress & European Conference on Heat Treatment 2022, held in Salzburg, Austria.
The International Federation for Heat Treatment and Surface Engineering is an institution linking organizations around the world active in the fields of heat treatment and surface engineering, including national metallurgical and heat treatment association, such as the AIM (Associazione Italiana di Metallurgia), for which TAV VACUUM FURNACES is a supporting member.
IFHTSE regularly organize international conferences and congresses to promote sharing of knowledge between associations, universities, research institutes and companies.
The IFHTSE – ECHT 2022 covered many different topics related to heat treatment of steels and non-ferrous alloys, thermochemical treatments, coating technologies and finally, furnace technology.
As one of the major vacuum furnaces manufacturer, TAV VACUUM FURNACES gave a speech during the first day of the congress about the heat treatment of titanium alloys, more specifically, on the “Vacuum heat treatment of Ti6Al4V alloy produced via SLM additive manufacturing”.
The speech was based on a work developed by Department of Industrial Engineering of the University of Trento, SISMA S.p.a. and TAV VACUUM FURNACES and aimed at exploring how vacuum heat treatments could impact the mechanical properties of titanium grade 5 parts produced using Selective Laser Melting 3D printing.
SLM printing for the healthcare industry
We already talked about the Selective Laser Melting technology extensively in previous articles. Just to recap, SLM is a 3D printing technology which make us of an high energy laser beam to melt a metallic powder. The controller of an SLM machine guides the laser beam following the slices of a 3D CAD file, melting the powder layer after layer until the part is completed. The very nature of the process enables to produce high complex geometries with cavities, undercuts and lattice structures without the limitations typically related to conventional manufacturing.
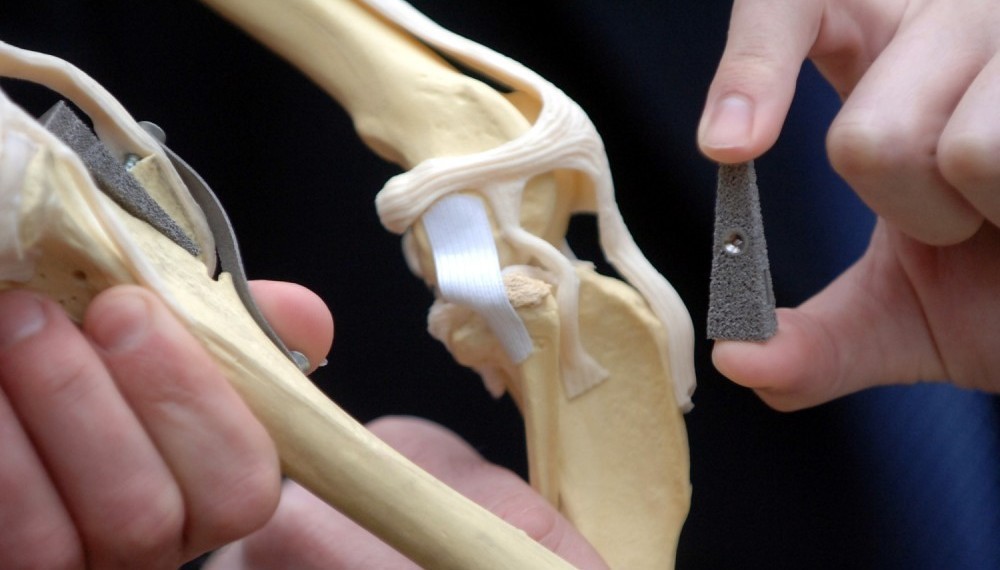
Fig.1: Surgical implant produced through Powder Bed Fusion Additive Manufacturing
("3dp fusion implant example" by andreaskofner is licensed under CC BY-SA 2.0)
The topic of adjusting the mechanical properties of SLM printed parts through heat treatment to meet specific requirements is particularly relevant today considering that the technology is becoming increasingly popular for the production of dental prothesis, surgical implants and other components for the healthcare industry. Selective Laser Melting is not only able to work with the main go-to materials utilized in the biomedical sector (biomedical grade stainless steel, cobalt-chromium alloys and titanium alloys) but also allows to create one of a kind medical devices fitted to the patient needs. Moreover, though SLM is possible to create very fine and complex lattice structures that replicate the bone tissue ensuring a high level of compatibility between the implant and the human body.
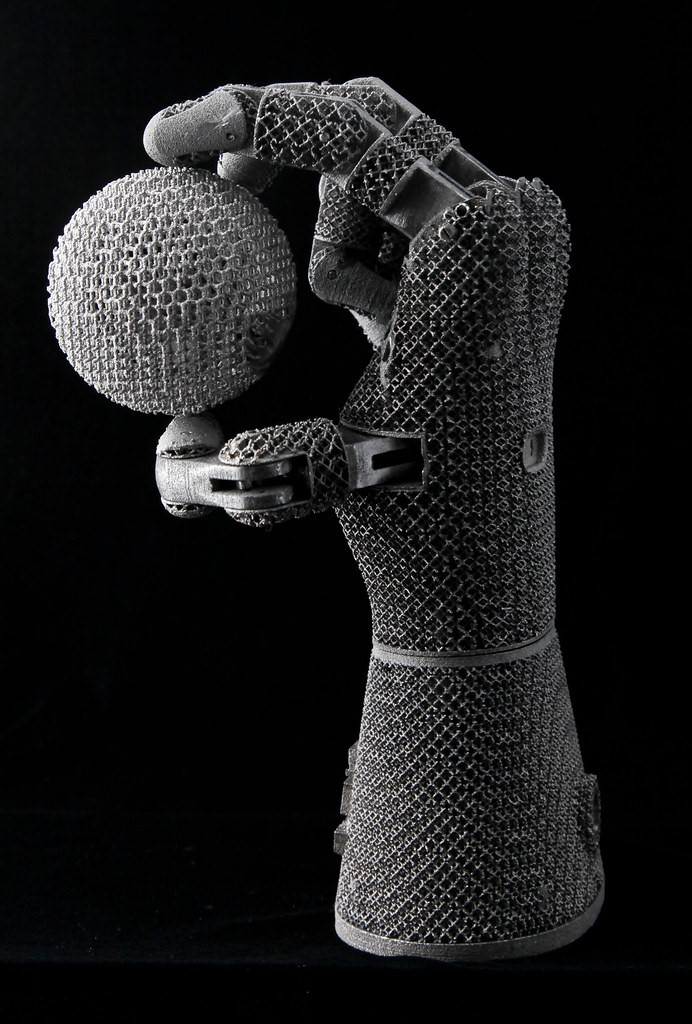
Fig.2: Titanium AM trabecular structures produced using Electron Beam Melting
("Additive manufacturing" by oakridgelabnews is licensed under CC BY 2.0”)
Vacuum Heat treatment of SLM produced implants
The surgical implants industry is regulated by strict standards; the American ASTM F136-13 (“Standard Specification for Wrought Titanium-6Aluminum-4Vanadium Extra Low Interstitial Alloy for Surgical Implant Applications”) is often taken as a reference in that sense.
The standard set specifications both in terms of chemical requirements and mechanical properties, more specifically, the following table presents the requirements for parts with thickness or diameter comprise between 4.75mm and 44.45mm.
Tensile Strength min (MPa) |
Yield Strength (0.2 % offset) min, psi (MPa)
|
Elongation A in 2 in. (50 mm), min, %
|
860 |
795 |
10 |
It’s important to note that these requirements are not specified in respect of the testing direction of the parts; that means that the isotropy of the mechanical properties, for Ti-6Al-4V surgical implants, is a necessary condition.
Moreover, the continuous heating and rapid cooling cycles that the material undergoes during the Selective Laser Melting process cause internal stresses to arise and the formation of fine, hard and brittle martensitic structure. For that reason, even though the strength of Ti6Al4V components produced by SLM is often superior to that of the same material produced by conventional manufacturing, the material shows a lack of ductility in the as-built condition and a significant disparity in the mechanical properties, with an higher tensile and yield strength along the build direction.
A post-process heat treatment, which is typically carried out in vacuum furnaces due to the high reactivity of the Ti-6Al-4V alloy, is then necessary to improve the tensile elongation and eliminate the inherent anisotropy.
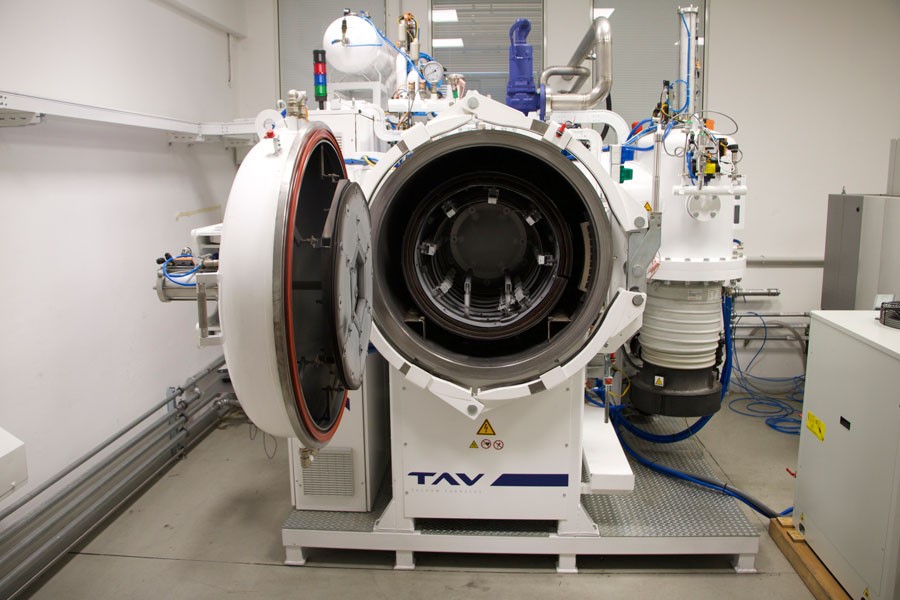
Fig.3: TAV TPH 30-30-45 inside TAV VACUUM FURNACES R&D Laboratory
In view of this, the aim of our work was to investigate the influence of four different vacuum heat treatments on the microstructure and mechanical properties of samples produced by means of SLM technology in Ti6Al4V, in order to design a specific heat treatment capable of meeting the requirements of titanium alloys for biomedical applications.
Experimentation
Tensile test samples were produced by SISMA through their Laser Metal Fusion (LMF) technology using a MYSINT100 printer in Argon atmosphere. The samples were produced with the longitudinal axis parallel to the printing direction.
All the heat treatments were performed in the TAV VACUUM FURNACES R&D Laboratory using our TAV TPH 30-30-45 HP.
This high vacuum furnace is equipped with an all-metal molybdenum hot zone and has the option of using pressurized argon gas to cool down the parts.
Moreover, the furnace is equipped with a dew point meter to check the gas purity. For these reasons, the TAV TPH 30-30-45 HP is well suited to heat treat materials that are both carbon and oxigen sensitive such as titanium.
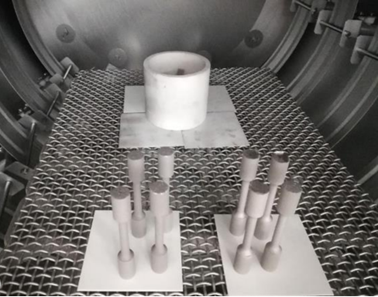
Fig.4: Samples in the furnace hot zone of TAV TPH 30-30-45 before heat treatment
The tensile test specimens were placed vertically inside the furnace and heated in high vacuum (absolute pressure <5x10-4bar) to the selected heat treatment temperature (650, 845, 950 and 1050°C respectively). After holding at temperature for 2 hours, the samples were cooled with free cooling or pressurized Argon according to the strategies chosen.
Results
The microstructure obtained on the samples heat treated at lower temperature (650°C) is very similar to the one typical of SLMed samples in the as-built condition, showing the presence of a martensitic α structure with elongated grains oriented in the build direction.
For higher temperature heat treatments is it possible to observe the presence of an equilibrium α+β microstructure, with a percentage of the α phase increasing with the temperature.
Increasing the temperature up to 950°C also makes the microstructure obtained after heat treatment coarser. The grain coarsening effect is further accentuated in treatments with slow cooling ('furnace cooling') compared to treatment with fast cooling ('air cooling').
Tensile tests show a progressive restoration of ductility in the specimens, at the expense of tensile strength.
Specimens heat treated at 845°C and 950°C meet the standard in terms of both percentage elongation at break and yield strength. For samples treated at 1050 specimens, however, the yield strength and ultimate tensile strength are below the minimum prescribed by the standard.
Conclusions
Some important conclusions can be drawn from this study.
First of all, the tensile test values demonstrated that, to completely satisfy the ASTM F136-13 requirements, Ti-6Al-4V samples produced via SLM must be heat treated. In fact, the ductility of the samples in the “as-built” condition is below the standard’s requirement.
Furthermore, heat treatment parameters must be carefully selected to guarantee the desired mechanical properties; indeed, only some of the heat treatments studied resulted in compliant mechanical properties both in terms of elongation at break and yield strength.
For any inquiries regarding the vacuum heat treatment of titanium parts don’t hesitate to contact us.
Also, if you’re interested in the topic of heat treatments for additive manufactured parts check out our article to learn why heat treat additive manufactured metal parts.
Finally, to learn more about the metal powders for additive manufacturing applications, have a look at our article on powder metallurgy and the production of metal powders.
Giulio Rossato, Ali Reza Jam and Massimo Pellizzari, University of Trento, Via Sommarive 9, Trento, Italy. CONTACT: massimo.pellizzari@unitn.it
Carlo Lora, SISMA, Via dell’Industria 1, Piovene Rocchette, Vicenza, Italy. CONTACT: clora@sisma.it
Giorgio Valsecchi, TAV VACUUM FURNACES SpA, Via dell’ Industria 11, Caravaggio, BG, Italy. CONTACT: rd@tav-vacuumfurnaces.com