As discussed in the
previous part
of the article we will pass through benefits and drawbacks of Binder
Jetting (BJ) and Metal Injection Moulding (MIM) technologies.
I think you’ll be surprised by some of the information I’m going
to reveal, read on.
To analyze in detail the pros and cons of binder jetting, it has to be considered
that this technology is inspired by a wider category of additive manufacturing
technologies defined as Material Jetting.
A glance at Material Jetting
Basically, in Material Jetting technologies, all the part material is dispensed
from a print head.
Instead, in the Binder Jetting technology, a binder or other additive
is printed onto a powder bed which forms the bulk of the parts.
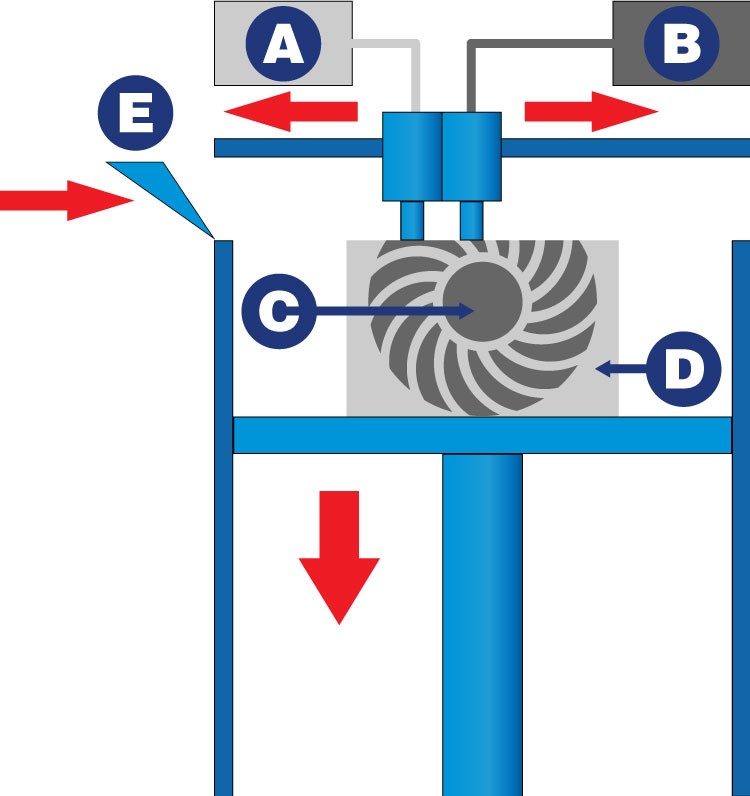
A: support material; B: build material; C: part; D: part support; E: leveling blade
To get a complete picture of the advantages and disadvantages of binder jetting,
we have to first analyze pros and cons of material jetting and see how the benefits
and drawbacks of binder jetting fit into this context.
The primary advantages of material jetting include
- low cost,
- high speed,
- scalability,
- ease of building parts in multiple materials.
Material jetting machines are much lower in cost than other AM machines,
particularly the ones that use lasers.
In general, these machines can be assembled from standard components, while other
machines have many more machine-specific components.
High speed and scalability are related: by using print heads with hundreds or thousands
of nozzles, it is possible to deposit a lot of material quickly and over a considerable
area. Scalability in this context means that printing speed can be increased by
adding another print head to a machine, a relatively easy task, much easier than
adding another laser to Selective Laser Melting or Selective
Laser Sintering machines.
For completeness, I will show you a few disadvantages of Material Jetting, just
to provide a more balanced presentation.
- The choice of materials to date is limited, only waxes
and photopolymers are commercially available.
- Part accuracy, particularly for large parts, is generally
not as good as with some other processes, notably vat photopolymerization and
material extrusion. However, accuracies have been improving across the industry
and are expected to improve among all processes.
Let's now go into detail of the binder jetting manufacturing process.
Did you like this article up to here?
Before you continue, follow us on our Twitter page pressing the button here below!
In this way, we'll be able to keep you updated on most advanced technologies for heat treatments not only with our posts, but also with the best articles that we collect around the web.
Binder Jetting pros and cons
The binder jetting process shares many of the advantages of material jetting
relative to other additive manufacturing processes.
With respect to MJ, binder jetting has some distinct advantages.
- It can be faster since only a small fraction of the total
part volume must be dispensed through the print heads.
However, the need to distribute powder adds an extra step, slowing down binder
processes somewhat.
- The combination of powder materials and additives in binders enables
material compositions that are not possible, or not easily
achieved, using direct methods.
- Slurries with higher solids loadings are possible with
BJ, compared with MJ, enabling better quality ceramic and metal parts to be
produced.
- Binder jetting processes lend themselves readily to printing colors
onto parts.
As a general rule, however, parts fabricated using BJ processes tend to have
poorer accuracies and surface finishes than parts made with MJ. Infiltration steps
are typically needed to fabricate dense parts or to ensure good mechanical properties.
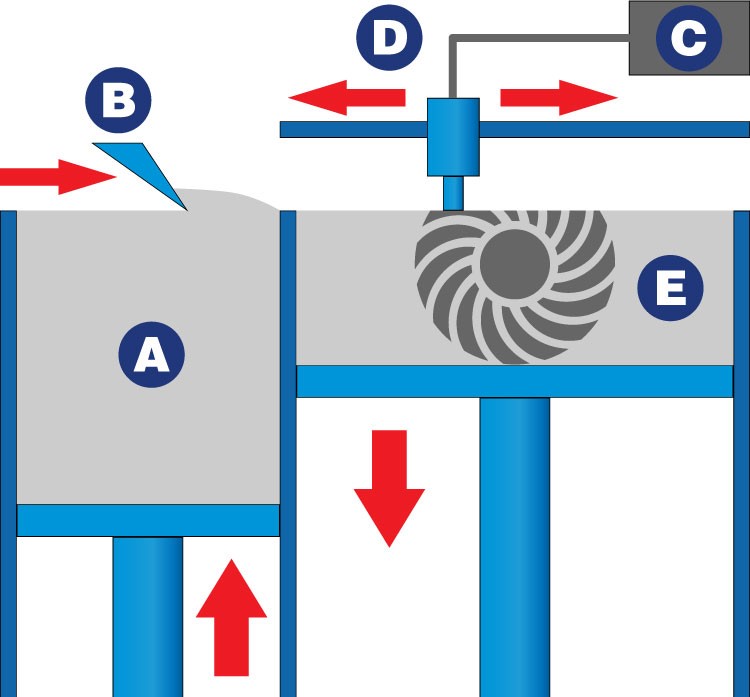
A: metal powder stock; B: squeegee; C: binder; D: print head; E: powder bed
As with any set of manufacturing processes, the choice of the process and material
depends largely on the requirements of the part or device.
It is a matter of compromising on the best match between process capabilities and
design requirements.
Is binder jetting going to replace metal injection molding?
Read the next chapter to have the right answer.
Metal Injection Moulding pros and cons
Now it’s the turn of Metal Injection Moulding: what makes your part suitable
for creation via MIM?
To determine this, here's a look at some of the advantages of this process:
- Design Complexity: if you're satisfied with the design
freedom you get from plastic injection molding but want to
craft metal parts, then MIM could be right for you. That's because the two processes
are quite similar in terms of design complexity - the main differences being
that one produces plastic parts and the other metal ones. With MIM, cross holes,
angle holes, splines, undercuts, side holes and grooves are all possible. Additionally,
with MIM you can create whole parts that would often have to be created separately
and assembled in post-production.
- Small Size: MIM uses very fine powders to create fully
dense metal parts, hence the process is best for small parts, typically those
that weigh between 0.1 and 250 grams.
- Production Volume: MIM can be a very cost-effective
process, but only if the right number of parts are needed. Typically, the cost
benefits are most noticeable and most worth it when part runs are between 10,000
and 20,000. The potential cost savings from using MIM might not be evident at
all producing fewer than 10,000 items.
- Properties: as we've already noted, if the process
is carried out correctly MIM can create fully dense or near fully dense metal
parts when the process is complete. It's particularly beneficial for parts that
are too small or too detailed to machine out of bar stock. For comparison's
sake, it's estimated that the part density is 98% via MIM, compared to 100%
via conventional machining processes.
- Economical: unlike machining, MIM doesn't cut away
existing metal - it uses only the amount of materials that is necessary to create
the product. Nothing is wasted.
Conclusions
After presenting in detail the pros and cons of the Binder Jetting vs. Metal
Injection Molding technologies, we can conclude that BJ is not destined to replace
the MIM in a short time.
Today binder jetting is a more convenient technology when it comes to small productions
at the prototype level of components with complex geometry. In this case the MIM
should face a design and production of always different molds that would result
in an unjustified increase in the final price of the single component.
On the other hand, metal injection molding is a much cheaper technology when
it comes to greater productions of a component even with complex geometry and reduced
dimensions. In this case the cost of the single mold can be amortized during the
repeated production of the same component and it turns out to be a more productive
technology.
To get rid of any doubt, take a look at the final comparison table:
|
Metal Injection Molding |
Binder Jetting |
Cost |
Cheaper when producing many parts. |
Cheaper when producing few parts. |
Accuracy |
Today the best choice in term of design complexity, especially for
small parts. |
The technology is getting better every day and it’s expected to
highly improve. |
Speed |
Lower speed if we consider the entire process chain (design and
production of moulds). |
Higher speed if we consider the entire process chain. |
Density |
It's particularly beneficial for parts that are too small or too
detailed to machine out of bar stock. |
Infiltration steps are typically needed to fabricate dense parts
or to ensure good mechanical properties. |
Productivity |
The cost benefits are most noticeable and most worth it when part
runs are between 10,000 and 20,000. |
More convenient when it comes to small productions at the prototype
level. |
Do you want to see more photos?
We have many more.
Visit our Pinterest page pressing the button here below and then follow us to keep in touch!