Microextrusion technology is a valid alternative to produce micro components with complex features and tight tolerances.
Microextrusion of plastics represents a solution for some industrial applications such as in the biomedical field, despite its many challenging aspects.
Micromanufacturing technologies
Recently, metal feedstock (a mixture of metallic particles and polymeric binder) has been extruded to produce metallic parts after sintering.
Application in the micro field became nowadays possible, thus opening the possibility for designing a new process chain to produce precise metallic components (workpieces with hollow structures as multilumen microtubes).
Once extruded, such tubes can be deformed and shaped for defining the final part geometry before the sintering takes place. Micromilling can be applied before and/or after
sintering to modify the parts geometry and micropolishing can obtain the final surface characteristics.
A limited experience exists in metallic feedstock extrusion despite this material is used in Metal Injection Molding (MIM), a well-known process both in the industrial practice and in the scientific literature.
Several aspects of the process need to be improved, starting from the feedstock, whose composition has to be optimized to be extruded, to the extruder itself, that experiences severe friction and wear.
Process chain improvements
In the frame of the
European Innovative Training Network MICROMAN - “Process Fingerprint for Zero-defect Net-shape MICROMANufacturing”, the research team of prof. Massimiliano Annoni of Politecnico di Milano (Department of Mechanical Engineering), involving the PhD student Sandeep Kuriakose and the researchers Paolo Parenti and Salvatore Cataldo, has worked to improve the process chain based on microextrusion of feedstock (Figure 1) starting from the characterisation and selection of the suitable materials to extrude, studying the design of extruder components (e.g. the extrusion die) (Figure 2) and suitable off-line and in-line microtubes measuring techniques in order to develop new monitoring and control methods for improving the final part quality.
Interaction of microextrusion with other processes of the process chain as micromilling, sintering and polishing has been also pointed out.
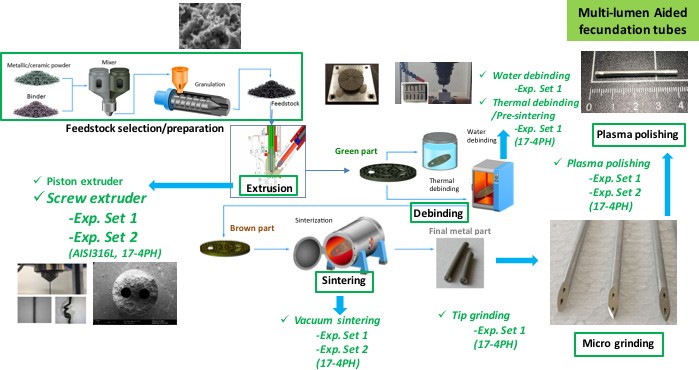
Figure 1: 17-4PH feedstock bi-lumen tubes process chain (adapted from
FineMIM)
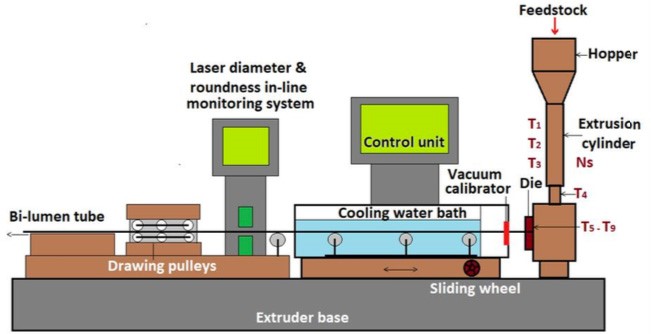
Figure 2: The schematic diagram of the micro extruder showing the process sequence of micro extrusion (Enki srl).
The extrusion of high aspect ratio micro components faces the challenge of maintaining the geometrical accuracy, surface finish and structural properties as the micro extrusion in green state is followed by debinding and sintering operations which result in shrinkage and variations in surface finish and structure.
The stages of the process chain such as solvent/thermal
debinding, to remove the polymeric binder, and presintering, to achieve a mild structural rigidity before the part sintering, are critical stages in achieving the surface and structural properties in case of high aspect ratio micro parts and are not yet studied in case of micro extrusion of feedstock.
The effect of debinding and presintering on surface and structural properties of bi-lumen tubes processed at different extrusion conditions are discussed in a research paper presented at the
World Congress of Micro and Nano Manufacturing (WCMNM 2019) that took place at Raleigh, North Carolina (USA) from 10 to 12 September 2019 (1).
Surface roughness of the tubes was analyzed using 3D microscopy and structural properties are studied using scanning electron microscopy (SEM) and electric discharge spectroscopy (EDS).
The debinding and presintering experiments on extruded micro bi-lumen tubes retained very good surfaces without any cracks or defects.
The study showed that interactions of extrusion temperature and extrusion velocity influence the surface finish of the extruded tubes the most.
The sintered bi-lumen samples of 17-4PH showed a good areal surface finish Sa of 2.21 μm which is near to the green state value confirming the suitability of the applied debinding and presintering parameters.
The type of metallic powder, powder size, type of binder and binder properties are very decisive in making the extrusion process feasible for the micro application.
The influence of feedstock properties on micro extrusion of high aspect ratio micro components are still unknown in case of micro extrusion of feedstock.
The effect of type of feedstock on micro extrusion was studied and presented in another paper from the same research team of Politecnico di Milano (2), where micro bi-lumen tubes were extruded using biocompactible steel feedstocks AISI316L and 17-4PH with two different ageing (Figure 3).
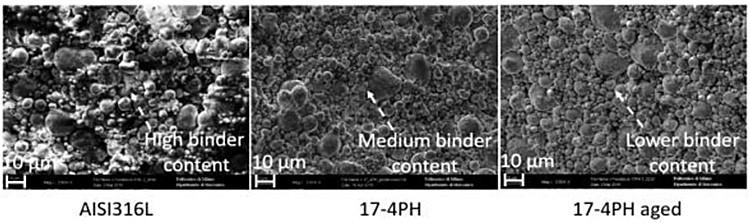
Figure 3: SEM image of feedstock, AISI316L D110E, 17-4PH G120E and 17-4PH G120E aged.
Did you like this article up to here?
Before you continue, follow us on our Facebook page pressing the button here below!
In this way, we'll be able to keep you updated on most advanced technologies for heat treatments not only with our posts, but also with the best articles that we collect around the web.
The geometrical features of the extruded bi-lumen tubes, surface roughness and structural properties were analyzed using 3D focus variation microscopy, differential scanning calorimetry (DSC) and scanning electron microscopy (SEM). The analysis showed that feedstock type affects the feasibility of extrusion in great extent. An average Sa roughness deviation from 1.73 μm to 4.57 μm was observed for feedstocks 17-4PH and AISI316L. The study also confirms that binder properties and ageing of the feedstocks also have to be taken into account for maintaining the surface finish and structural properties in case of metallic feedstock extrusion of high aspect ratio bi-lumen tubes.
Sintering treatments have been carried out in a TAV H3 all metal vacuum furnace installed at TAV VACUUM FURNACES R&D laboratory (the company attended the WCMNM 2019 conference).
Sintered tubes pictures can be seen in Figure 4 and Figure 5.
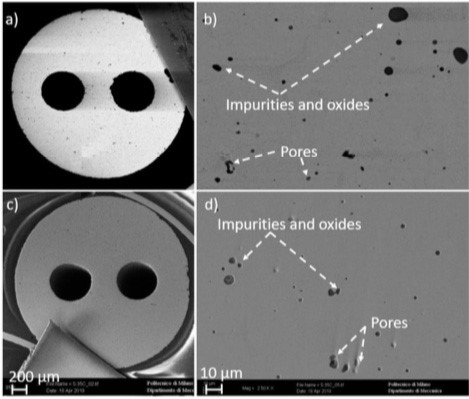
Figure 4: SEM Image of cross-section of bi-lumen tube at sintered state of a & b) 17-4PH and c & d) 17-4PH aged.
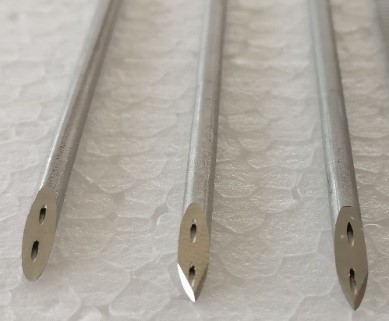
Fig. 5: Final bi-lumen tubes.
Conclusions
Hollow metallic parts as the bi-lumen tubes obtained in this research raise great interest in various industrial sectors as biomedical (needles, orthopedic implants and instruments, screws), chip removal tools, heat exchangers, etc. and open new applications and products.
The European Innovative Training Network MICROMAN
The continuous trend towards miniaturization and multifunctionality embedded in products and processes calls for an ever-increasing innovation, research and development within the European manufacturing sector.
A necessary condition for the European productive sector to be at the global forefront of technology, ensuring job creation and sustainable growth, is to have access to innovative, entrepreneurial, highly skilled research engineers in the fields of micro manufacturing, micro product/process development and quality control.
The MICROMAN ITN provides world excellent research training to 13 Early Stage Researchers (ESRs) in the field of micro manufacturing proposing:
- Innovative process fingerprint framework for zero-defect net-shape micro manufacturing;
- Cutting edge interdisciplinary training in different micro manufacturing technologies;
- Validation of technologies in industry for the production of micro component for the biomedical, healthcare, machine tool, pharmaceutical, quality control sectors.
MICROMAN provides an all-round, comprehensive yet specialized, training in micro manufacturing.
Specific training on project engineering research management and entrepreneurship completes the training and gives the ESR the required skills to effectively contribute to the competitiveness of the European micro manufacturing industry, to ensure job creation and well-being of the European society.

The project MICROMAN (Process Fingerprint for Zero-defect Net-shape MICROMANufacturing) has received funding from the Marie Sklodowska-Curie Actions (MSCA) under the European Union's Horizon 2020 research and innovation programme (grant agreement n° 674801).
References
- Sandeep Kuriakose, Salvatore Cataldo, Paolo Parenti, Massimiliano Annoni, Debinding and pre-sintering of high aspect ratio micro bi-lumen tubes produced by extrusion of 17-4PH feedstock, World Congress of Micro and Nano Manufacturing (WCMNM 2019), Raleigh, North Carolina (USA), 10-12 September 2019.
- Sandeep Kuriakose, Massimiliano Annoni Effect of feedstock properties on extrusion of high aspect ratio micro bi-lumen tubes, World Congress of Micro and Nano Manufacturing (WCMNM 2019), Raleigh, North Carolina (USA), 10-12 September 2019.
Did you find this article useful?
Please help us to spread it over the web using Twitter.
You have only to press the button here below!