As we all know, global events have led to a significant increase in energy cost in the past two years all over the world.
In Europe, current natural gas prices (February 2023) have more than doubled compared to the same period of 2020. In Italy, the cost of one MWh of electrical energy is about 3 times what the cost was just 1 year ago. Moreover, the strong price uncertainty makes difficult for companies to forecast the energy-related costs involved for the next few months.
Energy-intensive industries are largely impacted by price inflation; among them foundries, the metalworking industry and, of course, commercial heat treaters and companies performing in-house heat treatment of any sort.
Heating a load to a determined temperature for some time requires a certain amount of energy; whether that energy is generated from fossil fuel (coal, natural gas, petroleum) or renewable resources (solar power, wind power, hydropower), that is an inescapable reality.
Vacuum furnaces are inherently efficient machine; they can be programmed through a PLC (Programmable Logic Control), usually using dedicated software, to follow exactly a desired heating-cooling curve. That means that heating power is provided only when needed, while it is switched off when unnecessary (idle times, cooling etc.). Still, several auxiliary systems can be present on vacuum furnaces (or in the plant housing the furnace); just think of the water-cooling system, the gas cooling system and, clearly, vacuum pumps. Those auxiliary systems generate, altogether, non-negligible energy consumptions.
In this article we are going to analyze the main energy consumption sources related to the operation of vacuum furnaces, while providing general selection criteria and few tips on how to efficiently operates your vacuum furnace. If you are interested in finding out more about these matters keep on reading!
Heating
Most of the energy absorbed by a vacuum furnace is used, obviously, for heating; this energy is, at a glance, the sum of three separate components:
- Energy used to heat up the workload and the fixtures
- Energy used to heat up the furnace hot zone
- Dissipated energy
Let’s discuss each component more in detail.
Energy used to heat up the workload
Most vacuum furnaces are electrically powered, i.e. the energy is transferred to the workload from heating element through radiation (directly, for cold wall vacuum furnaces, or indirectly, for hot wall vacuum furnaces). Generally speaking, the amount of energy required to heat up the workload of a certain temperature increment is fixed and only depends on the mass and specific heat capacity (material) of the parts to be heat treated. On the other hand, radiation heat transfer works very well in vacuum, but is temperature dependent according to Stefan-Boltzmann Law, meaning that heat transfer in vacuum furnaces is far more efficient at high temperatures; for that reason convection heating (filling up the furnace with inert gas just below or above atmospheric pressure) is often used at temperatures below 600°C to speed up the process. Other factor influencing how fast the workload will heat up are its color, surface finishing and, especially, shape; thin and large part with high surface to mass ration will heat up significantly faster compared to thicker parts, thanks to their larger area available for heat transfer.
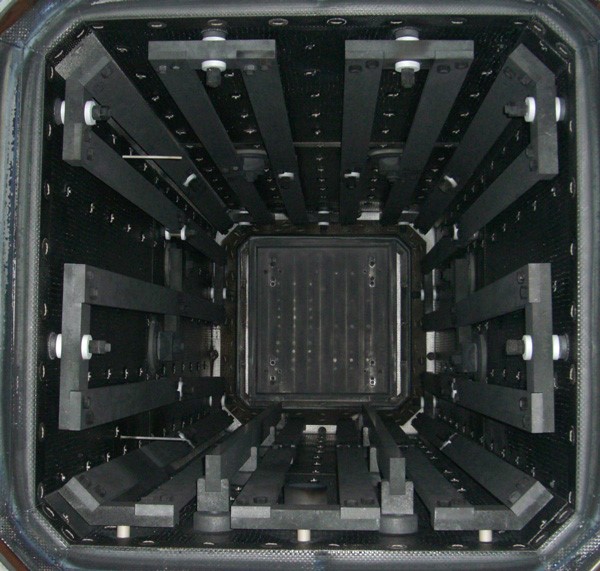
Graphite heating elements of a TAV vacuum furnace
Taking into account dissipations and energy consumption of the auxiliary utilities, which we will discuss more in detail below, shortening the total cycle time trough faster heating rates will always account for lower total energy consumptions.
Even if this statement is true physically speaking, this not always translates to lower expenses; in fact, to achieve faster heating rates the furnaces will require higher power absorptions, possibly exceeding the maximum power allowed by the electrical supply contract, incurring into peak power penalties.
It’s not possible to determine a priori which strategy will be the more economically favorable in all cases; a good rule of thumb could be to adopt the faster heating rate that allows to not exceed the contracted power, but each case should be carefully evaluated based on the supply contract, the specific process and the furnace specification.
As briefly aforementioned, vacuum furnaces are able to provide exactly the right amount of energy necessary to heat the load according to the heat treatment parameters selected; that is done thanks to a closed loop control system based on a PID controller. No heating power is consumed during pumping down, loading and unloading of the furnace, cooling and idle times.
Vacuum furnaces from TAV VACUUM FURNACES, other than being fully programmable, can be remotely monitored, allowing to schedule the heat treatment in the most efficient way to minimize energy expenditure, for example taking advantages of more favorable energy fees during certain hours of the day or by better spreading energy requirements of the factory equipment, again, to avoid peak power penalties.
It’s important to stress that, though energy consumption of vacuum furnaces will increase with the mass of the load to be heat treated according to the principles discusses above, this relationship is not linear.
In fact, with small batches the portion of energy required to heat the furnace hot zone and fixtures, which we will discuss in the following paragraph, is predominant, while it becomes proportionally less and less significant increasing the batch size, since the former component remains constant with larger batch sizes while the latter one increases. Therefore, the specific energy used to heat one kilogram of load (kWh/kg) will decrease exponentially increasing the batch size.
Although some limitations exist in terms of furnace and fixtures maximum load, other than part spacing to avoid damages and ensure uniform radiation, it is clear that exploiting the whole furnace capacity and increasing the furnace saturation will reduce the energy cost per unit associated with heat treatment.
Finally, we will just provide one remark regarding part fixturing: even though fixtures made of lighter, better performing material might be more expensive compared to others, heavier fixtures will also require more energy to heat up.
In some cases, the mass of the fixtures could be equal or superior to that of the parts to be heat treated, generating a non-negligible power consumption; this should always be kept into consideration during the selection process.
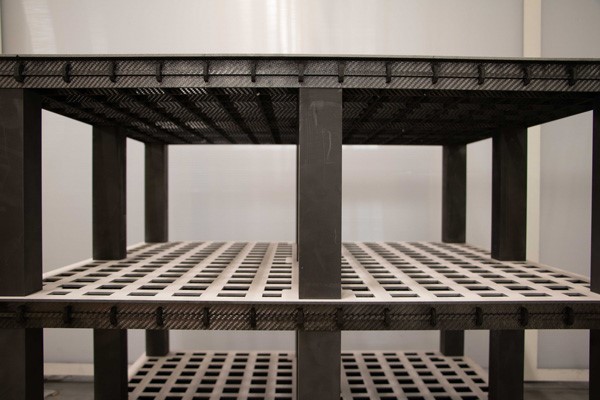
CFC fixture with ceramic coating
Energy used to heat up the furnace hot zone
All the considerations made in the previous chapter on energy requirements for heating the workload also stand for the energy required to heat the furnace hot zone, with the clear distinction that mass and physical properties of the insulation, resistors, load support and all the component of the furnace hot zone will stay constant for every heat treatment cycle performed on the same furnace.
On that subject, the total mass of the hot zone is a crucial parameter affecting the energy required for heating. A well thought out design should be able to maximize the useful volume to mass ratio; squared section are usually favored in that sense compared to round section hot zones. Moreover, closable hatches that are generally used on squared section hot zones to control the cooling gas flow further reduce dissipations compared to nozzles adopted on round section hot zones. For that reason, squared section are preferable whenever process constraints or part geometry do not strictly require a round section hot zone.
Dissipated energy
Even for the best designed vacuum furnace, dissipation accounts for a relevant portion of the absorbed energy; more specifically, this energy is dissipated in the form of heat transferred from the furnaces hot zone to the external (i.e., the furnace water-cooled jacket).
Many aspects of the furnace design will influence its energy losses, such as: size, shape (round section or square section), quantity and distribution of nozzles/hatches for gas quenching and hot zone material.
Different type of hot zone design and insulation are available. Nowadays, for vacuum furnaces, mainly two type of hot zone designs are employed:
- All-metal hot zone
- Graphite hot zone
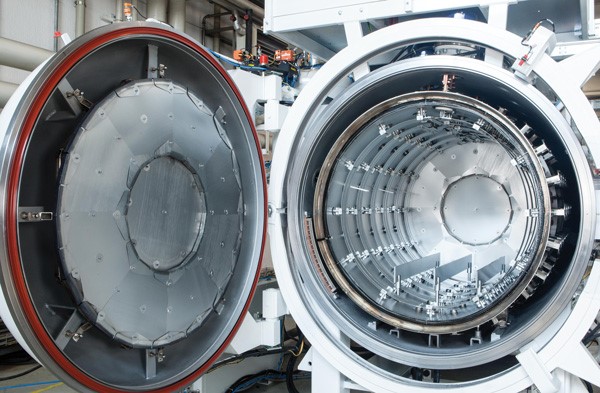
All-metal round section TAV vacuum furnace
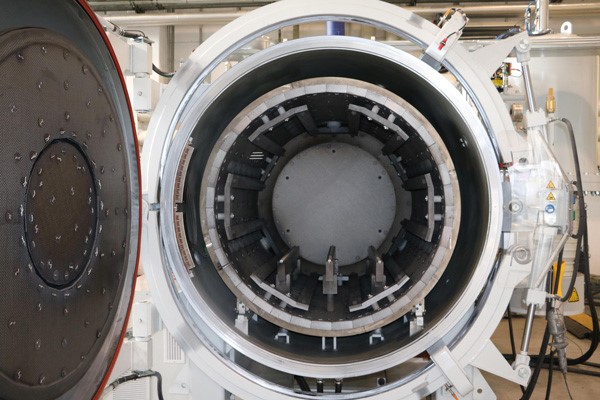
Graphite round section TAV vacuum furnace
The first one consists in a series of metal panels, spaced few millimeters, acting as reflective shields, with the inner ones made of refractories metal (usually molybdenum or tungsten, depending on the maximum operating temperature) and the outer ones made of stainless steel.
In the second case, the hot zone is insulated using a graphite wafer. In high quality vacuum furnaces, the graphite wafer in protected by a Carbon Fiber Composite (CFC) layer for improved mechanical resistance.
There are advantages and disadvantages to each type of hot zone design, with the all-metal hot zone providing a cleaner environment with very low outgassing rate, ideal for carbon sensitive or oxygen sensitive materials, other than faster heating rates, while the graphite design is usually cheaper, more robust and does not have problems of opacification over time.
If you want to learn more about pros and cons of all-metal and graphite hot zones, check out our article VACUUM FURNACE HOT ZONE: GRAPHITE VS ALL-METAL DESIGN.
In terms of dissipated energy, the advantage undoubtedly goes to graphite hot zones. In fact, energy losses in vacuum furnaces are mainly dependent on the temperature difference between inner and outer side of the hot zone; dissipations increase exponentially with increase in temperature. This effect is even more pronounced for all-metal hot zones compared to graphite insulated hot zone, as shown by the trends in the following graph.
We neglected precise values in the graph since, as discussed earlier, many factors other than hot zone materials are contributing to the actual dissipation values of a vacuum furnace. To give some references, specific dissipated power (kW/m2) at 1100°C for an all-metal vacuum furnace could be anywhere between 10% to 30% higher compared to an equally sized graphite furnace.
Whether a graphite insulated hot zone or an all-metal design is best suited to your process, optimal furnace design and quality of the materials adopted (including the production process of the hot zone elements) are crucial aspects in determining the energy consumption requirements of the furnaces, that will definitely payback any additional investment needed in the first place.
Do not miss out the part II of this article in which we will discuss about the energy consumption of auxiliary utilities and how TAV’s furnaces allow to efficiently manage those subsystems!