This article is available in English too.
Come tutti sappiamo, gli eventi globali hanno portato a un aumento significativo del costo dell'energia negli ultimi due anni in tutto il mondo.
In Europa, i prezzi attuali del gas naturale (febbraio 2023) sono più che raddoppiati rispetto allo stesso periodo del 2020. In Italia, il costo di un MWh di energia elettrica è circa 3 volte superiore a quello di un anno fa. Inoltre, la forte incertezza dei prezzi rende difficile per le aziende prevedere i costi legati ai consumi di energia per i prossimi mesi.
I settori energivori sono ampiamente colpiti dall'inflazione dei prezzi; tra questi, le fonderie, l'industria metallurgica e, naturalmente, i trattamentisti commerciali e le aziende che eseguono internamente trattamenti termici di qualsiasi tipo.
Riscaldare una carica a una determinata temperatura per un certo periodo di tempo richiede una certa quantità di energia; che sia generata da combustibili fossili (carbone, gas naturale, petrolio) o da risorse rinnovabili (energia solare, eolica, idroelettrica), questa è una realtà ineluttabile.
I forni in vuoto sono macchine intrinsecamente efficienti; possono essere programmati tramite un PLC (Programmable Logic Control), di solito utilizzando un software dedicato, per seguire esattamente una curva di riscaldo e raffreddamento desiderata. Ciò significa che l'energia di riscaldo viene fornita solo quando è necessaria, mentre viene spenta quando non è richiesta (tempi morti, raffreddamento, ecc.). Nei forni in vuoto (o nell'impianto che ospita il forno) possono comunque essere presenti diversi sistemi ausiliari; basti pensare al sistema di raffreddamento ad acqua, al sistema di raffreddamento a gas e, chiaramente, alle pompe per vuoto. Questi sistemi ausiliari generano, complessivamente, consumi energetici non trascurabili.
In questo articolo analizzeremo le principali fonti di consumo energetico legate al funzionamento dei forni in vuoto, fornendo al contempo criteri generali di selezione e alcuni consigli su come far funzionare in modo efficiente il vostro forno in vuoto.
Se siete interessati a saperne di più su questi argomenti, continuate a leggere!
Riscaldo
La maggior parte dell'energia assorbita da un forno in vuoto viene utilizzata, ovviamente, per il riscaldo; questa energia è, in sintesi, la somma di tre componenti distinte:
- Energia utilizzata per riscaldare la carica e i cestelli di supporto.
- Energia utilizzata per riscaldare la camera termica del forno
- Energia dissipata
Ma analizziamo ogni componente in maggiore dettaglio.
Energia utilizzata per riscaldare la carica
La maggior parte dei forni in vuoto è alimentata elettricamente, cioè l'energia viene trasferita alla carica dalle resistenze tramite irraggiamento (direttamente, per i forni in vuoto a parete fredda, o indirettamente, per i forni in vuoto a parete calda). In generale, la quantità di energia necessaria per riscaldare la carica di un certo incremento di temperatura è fissa e dipende solo dalla massa e dalla capacità termica specifica (materiale) delle parti da trattare termicamente. D'altra parte, il trasferimento di calore per irraggiamento funziona molto bene in vuoto, ma è dipendente dalla temperatura secondo la legge di Stefan-Boltzmann, il che significa che il trasferimento di calore nei forni in vuoto è molto più efficiente alle alte temperature; per questo motivo il riscaldo per convezione (riempimento del forno con gas inerte appena al di sotto o al di sopra della pressione atmosferica) è spesso utilizzato a temperature inferiori a 600°C per accelerare il processo. Altri fattori che influenzano la velocità di riscaldo della carica sono il colore, la finitura superficiale e, soprattutto, la forma; pezzi sottili e grandi con un elevato rapporto superficie/massa si riscaldano molto più velocemente rispetto a quelli più spessi, grazie alla maggiore area disponibile per il trasferimento di calore.
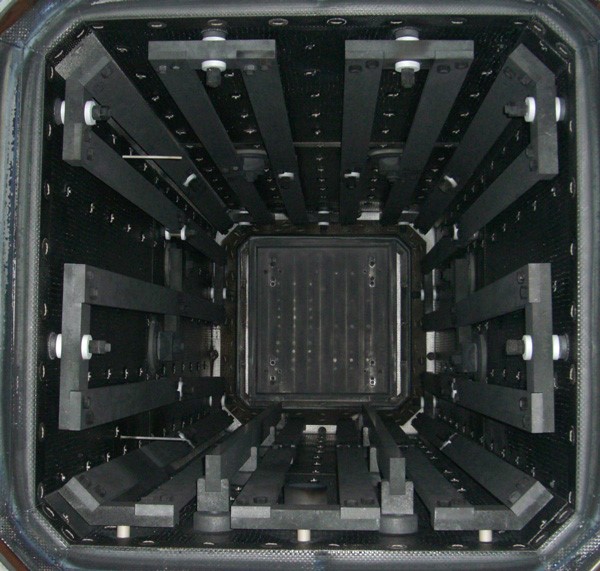
Elementi riscaldanti in grafite di un forno in vuoto TAV
Tenendo conto delle dissipazioni e dei consumi energetici delle utenze ausiliarie, di cui parleremo più dettagliatamente in seguito, la riduzione del tempo di ciclo totale attraverso velocità di riscaldo più elevate si tradurrà sempre in un minor consumo energetico totale.
Anche se questa affermazione è vera dal punto di vista fisico, ciò non sempre si traduce in minori spese; infatti, per ottenere velocità di riscaldo più elevate i forni richiederanno assorbimenti di potenza più elevati, eventualmente superando la potenza massima consentita dal contratto di fornitura elettrica, incorrendo in penali per la potenza di picco.
Non è possibile stabilire a priori quale strategia sia più favorevole dal punto di vista economico in generale; una buona norma potrebbe essere quella di adottare la velocità di riscaldo più elevata che consente di non superare la potenza contrattuale, ma ogni caso deve essere valutato attentamente in base al contratto di fornitura, al processo specifico e alle specifiche del forno.
Come brevemente accennato, i forni in vuoto sono in grado di fornire esattamente la giusta quantità di energia necessaria per riscaldare il carico in base ai parametri di trattamento termico selezionati; ciò avviene grazie a un sistema di controllo ad anello chiuso basato su un controllore PID. Non viene consumata energia di riscaldo durante il pompaggio, il carico e lo scarico del forno, il raffreddamento e i tempi di inattività.
I forni in vuoto di TAV VACUUM FURNACES, oltre a essere completamente programmabili, possono essere monitorati a distanza, consentendo di programmare il trattamento nel modo più efficiente per ridurre al minimo il dispendio energetico, ad esempio sfruttando tariffe energetiche più favorevoli in determinate ore del giorno o distribuendo meglio il fabbisogno energetico delle apparecchiature dello stabilimento, sempre per evitare picchi di potenza.
È importante sottolineare che, sebbene il consumo energetico dei forni in vuoto aumenti con la massa del carico da trattare secondo i principi sopra esposti, questa relazione non è lineare.
Infatti, con lotti piccoli la parte di energia richiesta per riscaldare la camera termica del forno ed i cestelli, di cui parleremo nel paragrafo successivo, è predominante, mentre diventa proporzionalmente sempre meno significativa aumentando la carica, poiché la prima componente rimane costante con lotti più grandi mentre la seconda aumenta. Pertanto, l'energia specifica utilizzata per riscaldare un chilogrammo di carica (kWh/kg) diminuirà esponenzialmente aumentando la massa totale della carica trattata.
Sebbene esistano alcune limitazioni in termini di carico massimo del forno e dei dispositivi, oltre ad una distanza minima tra i pezzi per evitare danni e garantire un irraggiamento uniforme, è chiaro che sfruttando l'intera capacità del forno e aumentandone la saturazione si ridurrà il costo energetico per unità associato al trattamento termico.
Infine, ci limitiamo a fare un'osservazione sui cestelli ed i supporti carica utilizzati per il posizionamento dei pezzi durante il trattamento: anche se strutture realizzate con materiali più leggeri e performanti possono risultare più costose, i cestelli più pesanti richiedono anche più energia per il riscaldo.
In alcuni casi, la massa di supporti e cestelli potrebbe essere pari o superiore a quella dei pezzi da trattare termicamente, generando un consumo energetico non trascurabile; questo aspetto andrebbe sempre tenuto in considerazione durante il processo di selezione degli stessi.
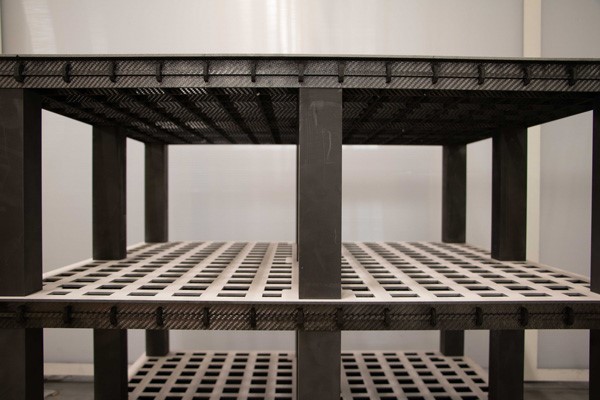
Cestello di carica in CFC con coating ceramico
Energia utilizzata per riscaldare la camera termica del forno
Tutte le considerazioni fatte nel capitolo precedente sui requisiti energetici per il riscaldo della carica valgono anche per l'energia richiesta per riscaldare la camera termica del forno, con la chiara distinzione che la massa e le proprietà fisiche dell'isolamento, delle resistenze, dei supporti carica e di tutti i componenti della camera termica del forno rimarranno costanti per ogni ciclo di trattamento termico eseguito sullo stesso.
A questo proposito, la massa totale della camera termica è un parametro cruciale che influisce sull'energia richiesta per il riscaldo. Un progetto ben studiato dovrebbe essere in grado di massimizzare il rapporto tra volume utile e massa; in questo senso, le camere termiche a sezione quadrata sono solitamente favorite rispetto a quelle a sezione circolare. Inoltre, gli schermi richiudibili, generalmente utilizzati nelle camere termiche a sezione quadrata per controllare il flusso di gas di raffreddamento, riducono ulteriormente le dissipazioni rispetto agli ugelli adottati nelle zone calde a sezione circolare. Per questo motivo, le camere a sezione quadrata sono preferibili quando i vincoli di processo o la geometria dei pezzi da trattare non richiedano rigorosamente una camera termica a sezione circolare.
Energia dissipata
Anche nel caso del forno in vuoto meglio progettato, la dissipazione rappresenta una parte rilevante dell'energia assorbita; più precisamente, questa energia viene dissipata sotto forma di calore trasferito dalla camera termica del forno all'esterno (ovvero alla camicia raffreddata ad acqua del forno).
Molti aspetti della progettazione del forno influiscono sulle perdite di energia, come le dimensioni, la forma (sezione rotonda o quadrata), la quantità e la distribuzione degli ugelli e portelle per il gas di raffreddamento oltre al materiale della camera termica.
Sono disponibili diversi tipi di design per la camera termica e differenti tipologie di isolamento. Oggi, per i forni in vuoto, se ne utilizzano principalmente di due tipi:
- Camera termica metallica
- Camera termica in grafite
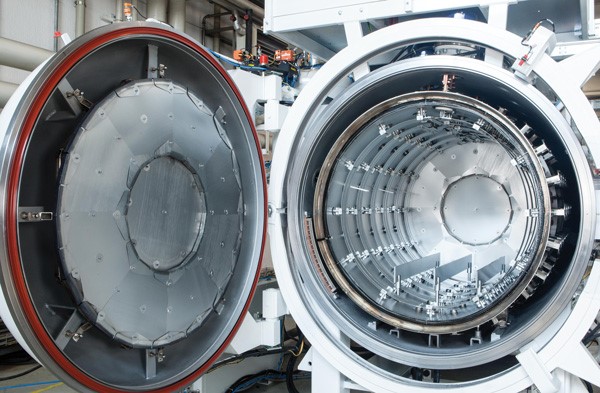
Forno in vuoto TAV a sezione circolare con camera termica metallica
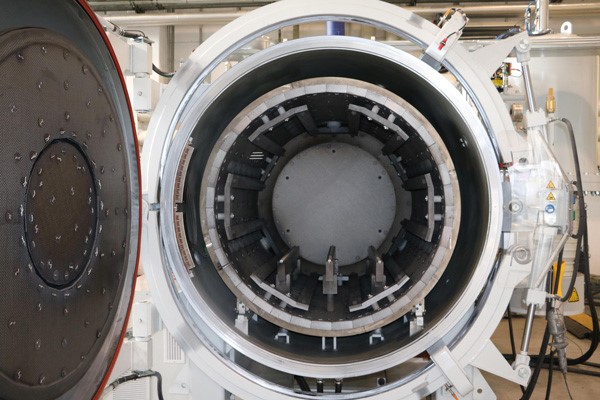
Forno in vuoto TAV a sezione circolare con camera termica in grafite
Il primo consiste in una serie di pannelli metallici, distanziati di pochi millimetri, che fungono da schermi riflettenti, con quelli interni in metallo refrattario (solitamente molibdeno o tungsteno, a seconda della temperatura massima di esercizio) e quelli esterni in acciaio inossidabile.
Nel secondo caso, la camera termica è isolata con un wafer di grafite. Nei forni in vuoto di alta qualità, il wafer di grafite è protetto da uno strato di fibra di carbonio (CFC) per migliorare la resistenza meccanica.
Ciascun tipo di camera termica presenta vantaggi e svantaggi: la camera termica interamente metallica offre un ambiente più pulito con un tasso di degassaggio molto basso, ideale per i materiali sensibili al carbonio o all'ossigeno, e consentono di ottenere velocità di riscaldo più elevate, mentre il design in grafite è solitamente più economico, più robusto e non presenta problemi di opacizzazione nel tempo.
Se volete saperne di più sui pro e i contro delle camere termiche metalliche e in grafite, vi invitiamo a leggere il nostro articolo CAMERE TERMICHE PER FORNI IN VUOTO: MEGLIO GRAFITE O METALLO?
In termini di energia dissipata, il vantaggio va senza dubbio alle camere in grafite. Infatti, le perdite di energia nei forni in vuoto dipendono principalmente dalla differenza di temperatura tra il lato interno e quello esterno della camera termica; le dissipazioni aumentano esponenzialmente con l'aumentare della temperatura.
Questo effetto è ancora più pronunciato per le camere termiche metalliche rispetto a quelle isolate in grafite, come mostrano gli andamenti del grafico seguente.
Abbiamo trascurato i valori precisi nel grafico poiché, come discusso in precedenza, ci sono diversi fattori, oltre al materiale della camera termica, che contribuiscono ai valori effettivi di dissipazione di un forno in vuoto. Per dare alcuni riferimenti, la potenza specifica dissipata (kW/m2) a 1100°C per un forno in vuoto metallico potrebbe essere superiore dal 10% al 30% rispetto a un forno in grafite di pari dimensioni.
Che sia camera termica isolata in grafite o camera metallica quella più adatta al vostro processo, una progettazione ottimale del forno e la qualità dei materiali utilizzati (compreso il processo di produzione dei vari elementi che compongono la camera termica) sono aspetti cruciali nel determinare i requisiti di consumo energetico dei forni, che ripagheranno sicuramente ogni investimento aggiuntivo necessario.
Non perdete la seconda parte di questo articolo, in cui parleremo del consumo energetico delle utenze ausiliarie e di come i forni TAV permettono di gestire in modo efficiente questi sottosistemi!