Nella prima parte dell'articolo, abbiamo discusso come diversi design influenzino l'efficienza dei forni a vuoto in relazione al loro consumo energetico nella fase di riscaldo.
Sebbene l'energia utilizzata per il riscaldo rappresenti indubbiamente la porzione principale del consumo energetico durante i trattamenti termici sottovuoto, nei forni a vuoto (o nello stabilimento che li ospita) possono essere presenti diversi sistemi ausiliari; basti pensare al sistema di raffreddamento dell’acqua, al sistema per la tempra in gas e, chiaramente, alle pompe per vuoto.
Questi sistemi ausiliari sono essenziali per garantire il corretto funzionamento di un forno a vuoto, ma possono generare complessivamente una fonte di consumo energetico significativa, soprattutto quando è richiesto un funzionamento continuo dell’impianto.
Pompe per vuoto
Le pompe per vuoto sono i componenti che consentono ad un forno sigillato ed a tenuta stagna di raggiungere il livello di vuoto desiderato prima di iniziare il trattamento termico.
Nella configurazione più tipica, i gruppi di pompaggio per il funzionamento a basso e medio vuoto (tra 1*10-3mbar ed alcuni millibar) consistono in una pompa meccanica, che può essere a tenuta d'olio o a secco, accoppiata ad una roots pump per ridurre il tempo di evacuazione.
Quando è richiesto il funzionamento in alto vuoto (a pressioni fino a 1*10-6mbar), sono disponibili diverse soluzioni: anche se le pompe turbomolecolari possono essere preferibili per applicazioni speciali in cui è imperativo avere un ambiente privo di contaminanti, le pompe a diffusione di olio rappresentano solitamente la soluzione più economica e robusta e sono quindi le più comuni.
Abbiamo maggiormente approfondito il principio di funzionamento ed i critieri di selezione delle pompe per vuoto in questo articolo.
Per un forno da tempra a camera orizzontale di medie dimensioni (come il modello TAV H8, 800x800x1200 mm), la potenza del motore per la pompa meccanica e la roots pump può essere, rispettivamente, di circa 5-6 kW e 4 kW. Per i forni a vuoto più grandi (modello TAV H15, 1500x1500x1500) la potenza può raggiungere i 15 kW per la pompa meccanica e gli 11kW per la roots.
Inoltre, la potenza di riscaldamento installata sulle pompe di diffusione di olio, necessaria per far bollire e vaporizzare il fluido di lavoro, è di circa 18kW per il modello H8 di medie dimensioni e di 24kW per il modello H15. Approssimando l'assorbimento effettivo delle pompe durante il funzionamento alla loro potenza di picco, il consumo totale di energia per il gruppo di pompaggio sarà di 28 kW per il modello H8 e di 50 kW per il forno a vuoto H15.
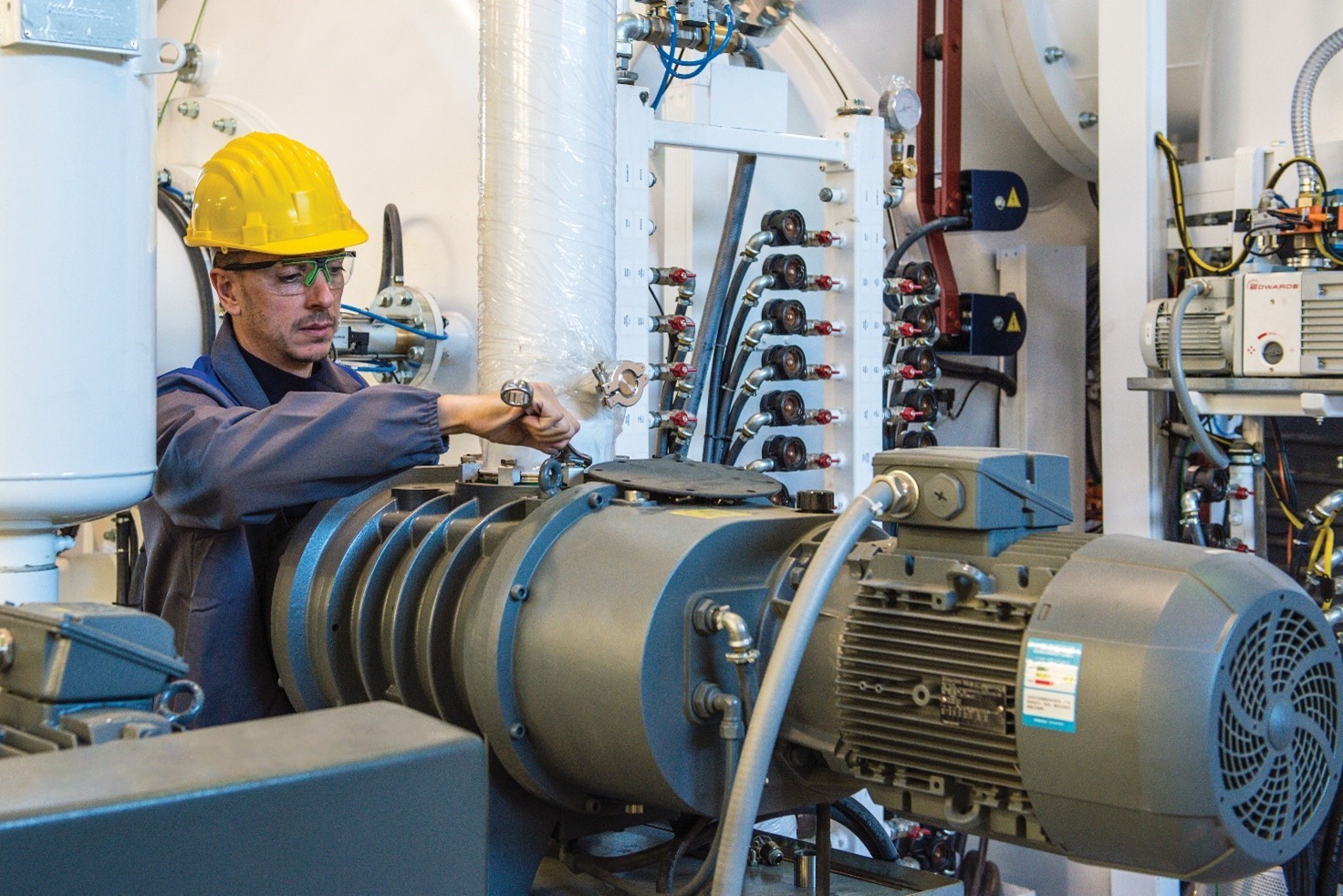
Operazioni di manutenzione su di una roots pump
Naturalmente, non è sempre necessario che le pompe per vuoto funzionino a piena potenza per l'intera durata del trattamento termico; modulando o disattivando completamente l'alimentazione delle pompe durante i periodi di inattività e le fasi del trattamento termico in cui non è richiesta l'evacuazione della camera da vuoto, è possibile ottenere notevoli risparmi in termini di consumo energetico. A tal fine, è necessaria una gestione intelligente e automatizzata delle unità di pompaggio.
Oggi sono disponibili diverse funzioni di risparmio energetico sui forni a vuoto TAV VACUUM FURNACES per ridurre al minimo il consumo energetico derivante dalle pompe per vuoto.
In primo luogo, le pompe vengono spente automaticamente quando non sono necessarie, non solo durante il raffreddamento ma anche durante il riscaldo in convezione di gas e le operazioni di carico/scarico tra i diversi lotti. Inoltre, è possibile scegliere una roots pump dotata di inverter; la presenza dell'inverter sulla roots pump aiuta a modulare la potenza e quindi a ridurre il consumo quando non è richiesto il livello di vuoto ultimo, come ad esempio durante il funzionamento in pressione parziale. Per quanto riguarda le pompe di diffusione, è possibile utilizzare un circuito di controllo comprendente un regolatore a tiristori ed una termocoppia per modulare la potenza durante le diverse fasi del ciclo (come stand-by, riscaldo e mantenimento), invece di fornire sempre la potenza nominale (e massima) come standard. In questo modo, si ottiene un risparmio di circa il 17% durante il normale funzionamento con la piena capacità di pompaggio, se si utilizzano oli siliconici come fluido di lavoro.
Infine, TAV utilizza una pompa di mantenimento per mantenere la pompa di diffusione nel range di vuoto richiesto; la presenza della pompa di mantenimento consente di mantenere la diffusione a vuoto senza dover accendere frequentemente la pompa meccanica principale, che nei forni a vuoto di medie e grandi dimensioni genera un consumo energetico sensibilmente più elevato.
Sistema per la tempra in gas
Nei forni a vuoto, la tempra in gas si ottiene mediante una girante di raffreddamento utilizzata per ricircolare gas inerte ad alta pressione in sistemi di guida dedicati attraverso la carica ed infine attraverso uno scambiatore di calore raffreddato ad acqua.
La potenza installata per il motore che aziona la girante di raffreddamento dipende da molti fattori: dimensioni e pressione massima consentita del forno, velocità targert e densità del gas selezionato.
Come riferimento, la potenza tipica del motore installato sula girante varia da 50kW a 250kW per i forni da tempra di dimensioni maggiori, anche se per applicazioni specifiche possono essere utilizzate potenze superiori.
Inutile dire che non tutti i trattamenti termici richiedono di raffreddare utilizzando la massima potenza della girante per l'intero processo. Pensando alla tempra degli acciai, ad esempio, per la fase di raffreddamento a bassa temperatura al di sotto della temperatura di trasformazione della martensite, la dissipazione di calore proveniente dal motore della girante può essere significativa rispetto al calore estratto dallo scambiatore di calore raffreddato ad acqua; in questa fase, utilizzare la massima potenza del motore non è né economico né efficace. Lo stesso ragionamento può essere applicato al trattamento di solubilizzazione delle superleghe e, in generale, a tutti i processi in cui le trasformazioni metallurgiche avvengono a temperature superiori rispetto alla temperatura ambiente. Per questo motivo, è possibile utilizzare un inverter per controllare il motore che aziona la girante di raffreddamento; ciò consente di modulare la sua potenza e di ridurne il consumo energetico. In questa configurazione, è possibile ridurre la velocità della girante di raffreddamento fino al 30% della massimale, riducendo così la potenza assorbita di 37 volte (la potenza assorbita è infatti proporzionale al cubo della velocità di rotazione).
Nei forni a vuoto TAV VACUUM FURNACES è possibile ridurre automaticamente la velocità della girante quando la temperatura del forno o della carica raggiunge un valore prestabilito, attraverso le funzioni di "controllo forno" e "controllo carica". Inoltre, è disponibile una funzione di "raffreddamento controllato", che autoregola la velocità del motore per seguire un gradiente di raffreddamento definito.
Sistema di raffreddamento dell’acqua
Il design più comune per i forni a vuoto è senza dubbio quello a parete fredda, in cui la campana del forno contiene una doppia parete che funge da camicia raffreddata ad acqua. Il sistema dell’acqua a servizio di un forno a vuoto a parete fredda deve essere in grado di far circolare l'acqua, utilizzando una o più pompe, attraverso uno scambiatore di calore e di nuovo al forno, mantenendo l'acqua fresca, a una temperatura adeguata.
Le pompe dell'acqua rappresentano, ovviamente, una fonte di consumo energetico; per questo motivo, nei forni a vuoto TAV VACUUM FURNACES è disponibile una funzione di risparmio energetico che consente di spegnere automaticamente le pompe dell'acqua quando il forno e la pompa di diffusione sono sufficientemente freddi.
Per i sistemi di ricircolo a circuito chiuso, lo scambio di calore necessario per raffreddare l'acqua può essere fornito da un dry cooler o da un chiller utilizzante un circuito refrigerato. Idealmente, l'acqua di raffreddamento dovrebbe essere mantenuta al di sotto dei 25°C; anche se la temperatura dell'acqua che entra nella campana del forno può raggiungere valori leggermente superiori senza comprometterla, è essenziale che l'acqua che serve la pompa di diffusione rispetti questo requisito durante tutto funzionamento del forno. Per questo motivo, un sistema di raffreddamento ad acqua che combini l'uso di un dry cooler e di un chiller può essere la soluzione più efficiente. Un dry cooler ha il vantaggio di dissipare calore richiedendo una spesa energetica molto bassa. Per raffreddare il sistema, l'acqua calda scorre attraverso i tubi del dry cooler scambiando calore con l'aria ambiente. Nella stagione più calda le ventole del dry cooler vengono attivate, forzando l'aria attraverso i tubi e favorendo lo scambio termico. Le ventole possono essere attivate in successione a varie soglie di temperatura, arrivando ad attivarle tutte solo quando necessario, nelle condizioni di utilizzo più gravose.
Con questa configurazione, se la temperatura ambiente lo richiede, è possibile utilizzare solo un piccolo chiller esclusivamente per la pompa di diffusione per ottenere una temperatura dell'acqua adeguata. Nei climi più caldi, invece, si può installare un chiller di dimensioni maggiori che serva l'intero sistema di raffreddamento dell'acqua e che venga acceso nei mesi più caldi.
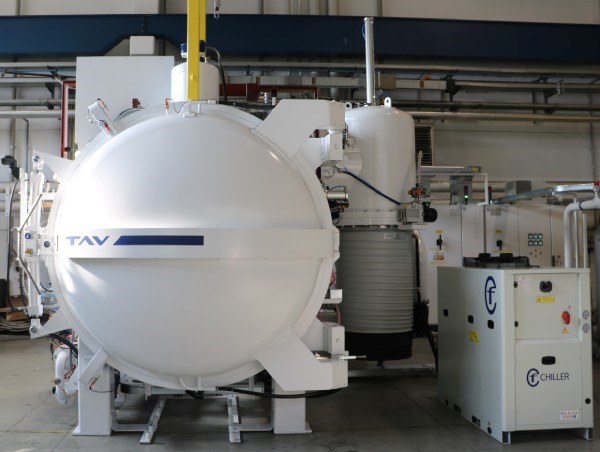
Pompa di diffusione con chiller dedicato
Se volete saperne di più su come operare e mantenere correttamente il vostro sistema di raffreddamento dell’acqua, consultate il nostro articolo.
Inoltre, nei forni TAV VACUUM FURNACES, il consumo energetico specifico per ogni ciclo di trattamento viene registrato e vengono tracciati in tempo reale gli assorbimenti elettrici e la velocità della girante di raffreddamento in una pagina dedicata "Energies", nel pannello di controllo. Ciò consente di tenere traccia dell'impatto dei parametri di processo sul consumo energetico e di intervenire ogni volta che vengono rilevati scostamenti dai valori storici.
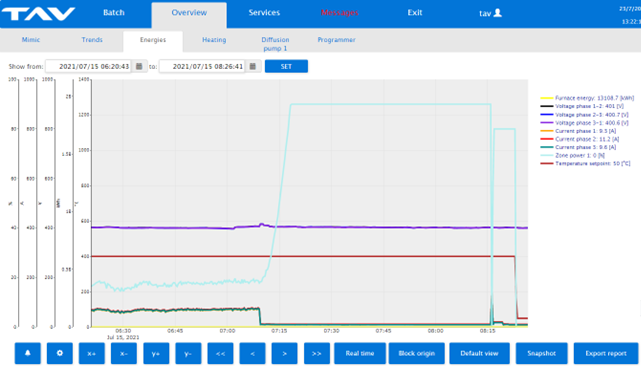
Pagina "Energies" del software di controllo dedicato TAV VACUUM FURNACES
In definitiva, una gestione efficiente dei sistemi ausiliari inciderà significativamente sui consumi energetici del vostro forno a vuoto, riducendo sia i costi operativi che l'impatto ambientale dei vostri trattamenti termici.
Per sapere di più sulle funzioni di risparmio energetico dei forni a vuoto TAV VACUUM FURNACES, contattateci all'indirizzo: info@tav-vacuumfurnaces.com.